Making the Case for Simulation of Additive Manufacturing
Increase additive manufacturing efficiencies and lower production costs with upfront simulation.
September 1, 2018
Falling prices on printer hardware and a plethora of new materials and design tools have catapulted additive manufacturing (AM) from a part-time prototyping resource into a full-scale production method. Yet as companies engage in more widespread use of the technology, they are actively trying to formulate new design for AM (DfAM) practices to address longstanding challenges and to capitalize on the design freedom AM affords.
The overall 3D printing segment is enjoying explosive growth, but metal AM in particular is a rising star: Research firm Wohlers Associates estimates that 1,768 metal AM systems were sold in 2017, a leap from 983 units in 2016. Laser sintering is the most common metal AM process, and research shows the automotive, aerospace, and biomedical industries are leveraging the technology to successfully produce prototypes, tooling and end-use parts.
Companies are flocking to metal AM for a variety of reasons. The technology, coupled with topology optimization software, provides a real opportunity to consolidate parts and deliver improved functionality thanks to greater design freedom. Unlike traditional forging or casting methods, metal AM offers a greater opportunity to produce organic designs that are more lightweight, thus saving on material costs. The production method also unleashes mass customization and on-demand business models simply not possible or practical with conventional manufacturing. At the same time, metal AM provides an opportunity to more seamlessly sync manufacturing with design processes via emerging concepts like the digital thread.
Trial and Expensive Errors
While there’s growing recognition of metal AM’s value as a full-scale production method, challenges abound, especially as they relate to DfAM practices, which are still fairly nascent. Most companies don’t have on-staff expertise versed in metal AM technologies and materials let alone significant knowledge of design best practices in newer areas like building lattice structures, varying material properties to achieve outcomes, or proper orientation of parts to ensure a successful and efficient build.
“What’s shifted in the last year or so is that as companies go deeper, they realize a lot can go wrong,” explains Brent Stucker, director, additive manufacturing at ANSYS. “They are wasting massive amounts of money on trial and error, and they need help.”
The cost of running an AM printer, on average, is estimated to be around $100 per hour, and a single build can take upwards of 20 hours—or closer to 80 hours for highly complex parts. That’s $2,000 to $8,000 wasted every time a part fails and has to be reprinted.
Simulation Helps Solve Challenges
Rather than learning from expensive trial-and-error processes, simulation—and specifically simulation of additive manufacturing processes—is a much more efficient and cost effective way to optimize use of metal AM technology. AM simulation tools and DfAM practices working in concert can help companies avoid the high costs associated with outputting parts that don’t meet quality specifications or that deform on production.
Latest News
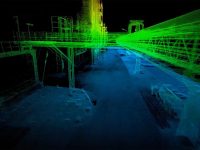
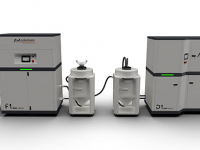
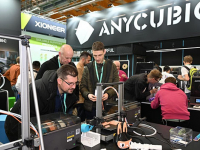
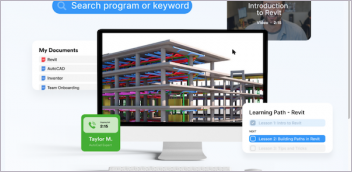

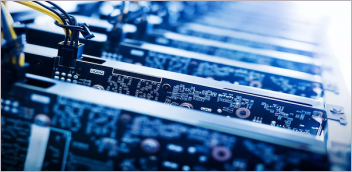
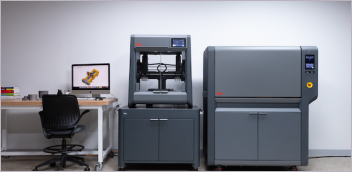