How to Get the Most Out of Additive Manufacturing
When evaluating Direct Digital Manufacturing for production, take a methodical analysis of cost, design, assembly, materials, and process to fully understand its benefits.

September 9, 2019
While additive manufacturing (AM) has mostly been used as a prototyping tool, in the past five years it has matured as a means of enhancing multiple stages of the product development process, including the production of end-use parts—a process termed Direct Digital Manufacturing (DDM).
A recent report published by Gartner predicts that, “By 2020, nearly 65% of discrete manufactures that expect to use 3D printers will be using them to produce components of the products they sell or service” (2016, Pete Basiliere, Research Vice President).
It has been difficult to recognize AM’s production manufacturing viability, as many have not yet shed the perception that AM is just a tool for prototyping. Thus, design engineers may be uncertain about how to use AM technologies and whether the available materials will meet their design needs.
Fortunately, the industry has made strides to produce machines and develop materials that are productionoriented. As a result, DDM is coming of age. The adoption of DDM leads to innovative product designs, shattering long-held manufacturing barriers, and making product development both less risky and more efficient.
Fill out the information below to download the resource.
Latest News
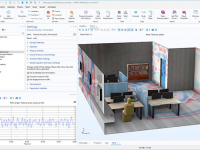
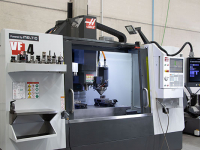
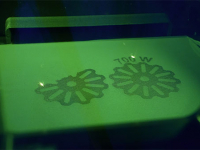
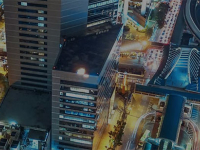
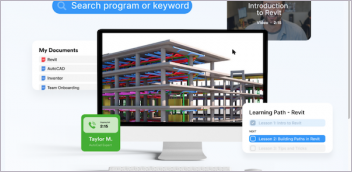

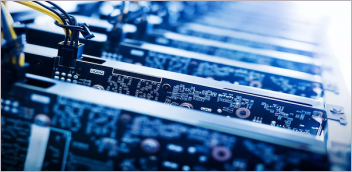
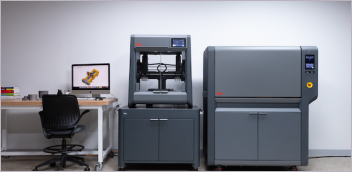