Sensors 101
Choosing the right sensor for the job isn't straightforward, but knowing the factors to consider can help you achieve your goals--and avoid unhappy surprises.
Latest News
January 1, 2011
By Barbara G. Goode
![]() An airbag sensor is an example of a device whose application requires fast response time. Image courtesy STMicroelectronics. |
Life is good for engineers looking to add functionality to their designs and enable product differentiation. Why? Because such functionality depends upon sensors, and now more than ever, sensors are available to detect every type of physical phenomenon conceivable. What’s more, sensors are more reliable and capable, smaller and much more affordable than ever before.
How Sensors Work
The function that a sensor performs is to detect a physical parameter and transduce its energy to a signal that can be understood. Thus, many people use the words “sensor,” “detector” and “transducer” interchangeably—and sometimes the word “monitor.” Implied in the act of detection or sensing is measurement of the strength of the phenomenon, and so the terms “sensing” and “measurement” can likewise mean the same thing.
Analog sensor signals are processed—digitized and often amplified—before the data is transmitted either to a controller, which evaluates it and may perform some responsive action, or to a data storage unit for the purpose of subsequent analysis.
Sensors can measure physical phenomena either directly, or indirectly, by inference. Tire Rack, Inc., for example, does a good job of explaining the difference using the example of tire pressure monitoring: “Direct systems attach a pressure sensor/transmitter to the vehicle’s wheels. An in-vehicle receiver warns the driver if the pressure in any tire falls below a predetermined level.” On the other hand, “indirect systems use the vehicle’s antilock braking system’s wheel speed sensors to compare the rotational speed of one tire versus the others. If a tire is low on pressure, it will roll at a different number of revolutions per mile than the other three and alert the vehicle’s onboard computer.”
Although many parameters can be measured directly or indirectly, some, like velocity, can be measured only indirectly. Similarly, phenomena can be measured either through contact with a sensor (that is, by a contact sensor) or without (that is, by a non-contact sensor). Contact sensors tend to be more reliable, but are not always practical or preferable because physical contact can have an effect on the measured parameter. Beyond that, the two approaches have distinct capabilities.
For instance, contact temperature sensors have a more sluggish response rate (seconds) than do non-contact (milliseconds). Watlow, a supplier of temperature sensors, outlines the pros and cons of contact and non-contact temperature sensing online at Din-a-Mite.com. Among the characteristics of each are:
Contact temperature sensor
- relatively rugged and accurate;
- economical;
- wide application range;
- simple to apply
- can cause wear on components; and
- acts as a heatsink, alters readings on small objects
Non-contact temperature sensor
- relatively rugged;
- can sense temperature of irregularly shaped objects, and objects in motion
- cannot sense temperature of gases;
- will not deface, mar, contaminate or interfere with the process;
- will not act as a heatsink;
- field-of-view (spot size) restrictions;
- ambient temperature restrictions; and
- indicated temperature affected by environmental conditions (dust, smoke, etc.)
![]() Sensors like Freescale’s MMA7660FC three-axis accelerometer enable product differentiation as well as basic functionality. Image courtesy of Freescale. |
Critical Concepts
Important concepts in sensing include sensitivity, which is the smallest amount of change in the measured phenomenon able to generate a detectable change in output. Similarly, resolution is the smallest unit of change evident in the signal generated.
The range of a sensor refers to the span within which it can deliver accurate measurements. For instance, a pressure sensor may have a range of 0 to 25 psi. Exposing it to conditions beyond this range can result in bad data or destruction of the sensor.
Precision and accuracy are often confused: Precision indicates a sensor’s ability to repeatedly produce the same output when measuring a phenomenon that remains stable. By contrast, the accuracy of a sensor is the maximum difference between the actual value of the measured phenomenon (for instance, temperature as measured by a calibration standard) and the value that the sensor outputs.
Along the same lines, offset is the reading that a sensor will produce compared with what it ought to produce—either when the output should be zero, or when it should correspond to a particular reading under a certain set of conditions (realistically, a sensor’s output will be ideal only at one point).
Response time is the increment of time that it takes a sensor to produce a settled output within an acceptable range of tolerance once it is exposed to the measurand (the quantity being determined by measurement), while linearity is the ability of the sensor to produce an output signal proportional to changes in the measured property over the working range of the device.
By contrast, dynamic linearity measures a sensor’s ability to represent changes in the property being measured. And hysteresis represents the ability of a sensor to respond to changes in the measured property, both up and down within the range.
When looking at sensor options, you must understand your needs in these various areas. For instance, an accelerometer in an automobile that deploys an airbag in response to a crash must have quick response time, but a temperature sensor that monitors liquid in a large tank need not.
![]() Temperature is the physical phenomenon most often measured. The most commonly used sensors for measuring temperature include both resistance temperature detectors (RTDs) and thermistors (left), and thermocouples (right). Images courtesy Omega Engineering, Inc. |
Sensor Resources Temperature sensing Pressure sensing General sensing |
What will you sense, and how?
Ideally, a sensor measures the property of interest—and is influenced by nothing else. For each property you may want to measure, there are multiple technologies available to accomplish the task. But not all of the sensor types may be suited to your application.
For instance, options for sensing temperature include resistance temperature detectors (RTDs), thermocouples and thermistors (thermal resistors)—each of which has different capabilities. Thermocouples are inexpensive and rugged, and have a wide range, but they are not known for accuracy. Thermistors are relatively cost-efficient, but have a narrow temperature range—though within that range they tend to be accurate. Likewise, RTDs are accurate within narrow temperature ranges, but costly. On the other hand, they offer repeatability and long-term stability, among other benefits.
And so it is with every measurand. Engineers can use sensors to measure many dozens of distinct phenomena, including acceleration, chemical composition and gas, displacement, flow, force, motion, pressure, proximity, position and presence; strain, torque, velocity, vibration, and viscosity. Multiple options exist for detection of each phenomenon, and every type of sensor has a specific range of capabilities.
Thus, it’s important to understand the particular demands of your application, in addition to the strengths, limitations and common sources of error inherent in each technology.
More Info:
Freescale
Omega Engineering
STMicrosystems
Tire Rack, Inc.
Watlow
Barbara G. Goode served as editor-in-chief for Sensors magazine for nine years, and currently holds the same position at BioOptics World, which covers optics and photonics for life science applications. Contact her via [email protected].
Subscribe to our FREE magazine,
FREE email newsletters or both!Latest News
About the Author

DE’s editors contribute news and new product announcements to Digital Engineering.
Press releases may be sent to them via [email protected].
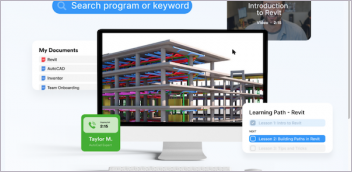

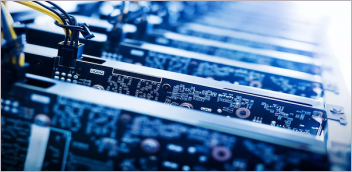
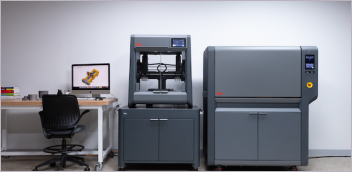