Latest News
December 31, 2013
Dear Desktop Engineering Reader:
This is either your last Check it Out column of the old year or your first of the New Year. Either way, today’s Check it Out link takes you to a nice, easy read that encapsulates what makes this all fun, especially when I’m trying to describe to people what goes into design engineering. Even though it’s just four pages, “The A to Z of Breaking a World Water Speed Record” packs in all the design engineer’s CAD/CAE tools, a bunch of cool images, and a surprising amount of technical details.
![]() |
The gist of the story is that back in 2008 Voxdale BVBA, a design, engineering, and research outfit based in Antwerp, Belgium, got a job from Bernico International, the speedboat manufacturer. The assignment sounds like one of those simple somethings that your boss hands you with an uncharacteristic grin: Design a Formula 2 class speedboat that’ll break the world record and the then speed barrier of 100 mph.
Now, F2 class speedboats for you non-Popeyes like me out there appear to be those two-person, rear-engine affairs. Well, definitely rear engine. F2 class speedboats are the ones that you see on ESPN zooming across a lake with most of the boat hovering just inches above the water. As you might imagine, designing such a boat is not inexpensive, so you don’t go building physical prototypes in your typical design cycle. This reality, of course, makes simulation invaluable.
So, Koen Beyers and his Voxdale colleagues got cracking right on it. Voxdale’s expertise lies in simulation for structural analysis, thermal management, and flow optimization. It does work for clients doing R&D, medical, environmental, and energy projects. And that’s where the whole engineering toolkit comes into the story.
First, they 3D scanned an existing Bernico speedboat hull and body to reverse engineer a baseline design. Then, working within their Pro/Engineer (now PTC Creo) CAD/CAE environment, they did surface modeling, mechanical integration and engineering, structural optimization using Pro/Mechania, thermal engine management, lightweight material selection, and design for cost and assembly. Still within Pro/E, they did their aerodynamics analyses using FloEFD 3D CFD (computational fluid dynamics), a fluid flow and heat transfer analysis package from Mentor Graphics. FloEFD fully embeds within systems like PTC Creo, meaning that it’s intended to be design engineer friendly and full-featured simultaneously.
The article dwells a bit on the details of the FloEFD simulations because they turned out to be the key to Voxdale’s innovations. Or as Beyers puts it “CAD/CFD/CAE simulation certainly stimulates radical innovation and leads to workable solutions.” Simulating design ideas early and frequently all during the process enabled Voxdale to reduce drag off of components throughout the new boat’s shape, including the cockpit and rear deck. They even reduced drag in the pilots’ helmets.
The upshot is that Voxdale met the challenge and the craft set the record. You can watch the record-setting tear by hitting a link at the end of the white paper. (Hint: Depending on your screen, you may need to capture the link and paste it in your browser.) The image where a FloEFD CFD hull pressure contours prediction is superimposed on the craft might just be 2013’s best. This is good stuff.
Thanks, Pal. Happy New Year. – Lockwood
Anthony J. Lockwood
Editor at Large, Desktop Engineering
Subscribe to our FREE magazine,
FREE email newsletters or both!Latest News
About the Author

Anthony J. Lockwood is Digital Engineering’s founding editor. He is now retired. Contact him via [email protected].
Follow DE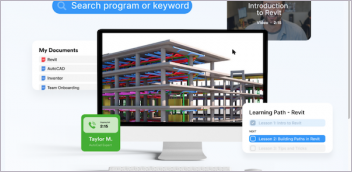

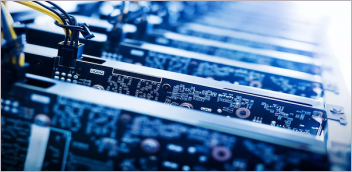
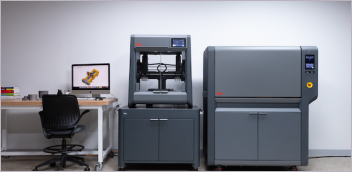