Latest News
September 1, 2013
Needless to say, the steel industry isn’t content to sit by and watch new materials erode their market. They are working hard to come up with new and better steel all the time to fend off the increasing competition from composites and aluminum. And for manufacturers like the auto industry, steel has the appeal of the familiar.
How Strong is Ultra-Strong?
“The auto industry is really trying to squeeze as much as they can out of steel auto bodies,” says Regu Ramoo, vice president of engineering at Altair Engineering. “The Acura 2007 MDX, for example, has seven different grades of high-strength steel in the body.”
And what, exactly, is high-strength steel? You can categorize steel broadly into three grades: everyday mild steel, high-strength steel, and ultra-high-strength steel. These categories, and the divisions between them, are somewhat arbitrary: Definitions change over time, and may vary depending on your source.
“Traditionally, anything that is not mild steel was referred to as high-strength steel or HSLA,” says Ramoo, referring to the acronym for high-strength low-alloy. “So, by American Iron & Steel Institute standards, anything above 275 MPa yield strength is HSLA.” (MPa = megapascals, or newtons per millimeter squared).
It used to be that the top end for high-strength steel had a yield strength of around 550 MPa, about twice that of commodity mild steel, Ramoo adds. Anything above that was considered ultra-high-strength, exotic or special-purpose. These days, with the top end in the vicinity of 1,700 MPa, definitions have shifted.
“Most automotive engineers today would consider high-strength or advanced high-strength to start at about 350 MPa,” says Ramoo. “We would designate steels above 950 MPa as ultra-high.”
Not surprisingly, high-strength and ultra-high-strength steels cost considerably more than mild steel. They are also more difficult to stamp and form.
As steel gets stronger, it becomes less malleable, says Ramoo: “The allowable elongation—the allowable strain-to-failure—is less. Your typical steel can go up to about 50% strain-to-failure. In really high-strength steel, you’re talking about maybe less than 10% strain-to-failure.”
Forming and Joining
Ultra-high-strength steel is still formable, just less so. It may require special processes such as hot forming, which can add to the complexity and cost.
But when it comes to formability, Ramoo says, you just can’t beat steel. “There are very few parts you cannot make out of steel, and the cycle time to stamp out steel parts is so much shorter,” he says. “They have that inherent advantage over composites. When you need high volumes, you can’t go with composites because the cycle time is so long.”
Those stamped steel parts are not only faster to make, they are much more consistent than composite parts. It’s also much easier to join steel parts.
“We understand welding of steel parts far more than we understand welding aluminum—and far more than we understand joining composites,” Ramoo explains. “There are a lot of things we just don’t know about aluminum and composites. It might be fine for the first three years, but after five years, what’s going to happen to the join? Is it going to creep? Are the bolts going to loosen? Will it become brittle?”
Ramoo points out that you can even weld steel of different strengths together in a blank to create fancy, tailor-welded blanks, to get multiple grades of steel through a single part—a sort of steel composite, if you will.
We Love Steel
Let’s face it, steel’s the standard. Consequently, it’s easier to work new kinds of steel into the existing manufacturing process than totally new materials.
“Look at the current infrastructure,” says Ramoo. “Everything in most auto plants is designed for a steel body right now.
“The cost penalty for high-strength steel is smaller than for aluminum and composites,” he continues, “and there are a lot of parts that you can improve by replacing them with the new grades of higher-strength steel. There’s a lot of room for automakers to lighten the steel body without having to resort to aluminum and composites.”
Steel is cheap, it’s recyclable, and we understand how to work with it pretty well. While composites certainly have their place in today’s auto industry, steel’s not going to be replaced anytime soon.
Contributing Editor Mark Clarkson is DE’s expert in visualization, computer animation, and graphics. His newest book is Photoshop Elements by Example. Visit him on the web at MarkClarkson.com or send e-mail about this article to [email protected].
More Info
American Iron & Steel Institute
Subscribe to our FREE magazine,
FREE email newsletters or both!Latest News
About the Author
Mark ClarksonContributing Editor Mark Clarkson is Digital Engineering’s expert in visualization, computer animation, and graphics. His newest book is Photoshop Elements by Example. Visit him on the web at MarkClarkson.com or send e-mail about this article to [email protected].
Follow DE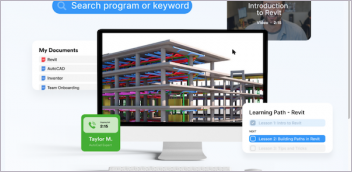

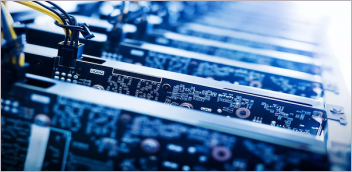
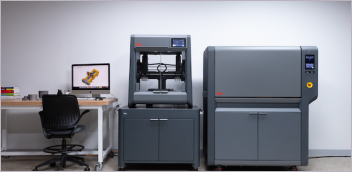