Latest News
January 7, 2014
By Anthony J. Lockwood
Dear Desktop Engineering Reader:
Wind can be vexatious. You have to work with it. Today’s Check it Out link takes you to a short piece about a collaboration with some plant engineers and CFD (computational fluid dynamics) mavens from IMAGINiT Technologies, a division of Rand Worldwide, to work with the wind. I think you’ll find it interesting.
![]() Image courtesy of National Energy Technology Laboratory. |
The story outline is that the summer winds caused headaches for an electric power generator in the southwest US. Summer is a good time to be in the power business in the southwest because of all those ACs running, so you want to be as efficient as possible to maximize your revenues.
Steam turbines are key to generating electricity, as you know. Air-cooled condensers (ACCs) can be an efficient method to minimize water use in dry areas, although their use appears to be becoming widespread in all regions, since they also eliminate water as a regulatory issue to satisfy during new plant construction or retrofits. Basically, ACCs condense steam discharged from the turbine and return water to the boiler. Huge fans suck in cooler outside air that’s used to cool the steam and the fans send the hot air away outside. Here lay the problem.
When the summer wind blew from a particular direction, the evacuated hot air would be drawn back into the ACC. This reduced efficiency, increased backpressure in the turbines, and decreased power output. To improve summertime power generating efficiency, plant engineers knew that they needed to increase the fan flow rate and improve flow uniformity across all ACC unit fans. And that meant some sort of accommodation with the hot summer winds.
That simply-stated goal wasn’t a simple solution to come up with. The company had spent about 10, labor-intensive years working on the problem with no special improvement. A full-bore CFD analysis of the airflow around the plant and across the ACCs had been ruled out as too expensive until a supplier turned them on to IMAGINiT. A similar project in the northeast demonstrated that there was a clear return on investment in CFD analysis, so the plant engineers opted to work with the IMAGINiT CFD Analysis group and leverage its expertise to solve their ongoing problem.
The article reports on how IMAGINiT’s CFD Analysis group worked with the plant engineers to come up with a solution involving directing plates. It touches on building 3D CAD models of the plant as well as simulating the airflows and air temperatures around the facility, the ACCs, fan stack exhaust, and wind speed, direction and temperatures.
Ultimately, all the CFD simulations and collaboration efforts worked—overall airflow increased by 2% and flow balance by 42%. Perhaps a better measure of the project’s success is that the power producer plans to work with IMAGINiT on comparable problems at some of its other plants.
This is a nice, tidy read. The moral of the story is that you might be just blowing out a lot of hot air if you rule out highly complex, in-depth CFD analyses because you presume the investment is not worth the effort or the costs out of your league. Your return on investment might prove you wrong. You won’t know until you learn more. Hit the link over there and download today’s Check it Out paper and see for yourself.
Thanks, Pal. – Lockwood
Anthony J. Lockwood
Editor at Large
Desktop Engineering
Subscribe to our FREE magazine,
FREE email newsletters or both!Latest News
About the Author

Anthony J. Lockwood is Digital Engineering’s founding editor. He is now retired. Contact him via [email protected].
Follow DE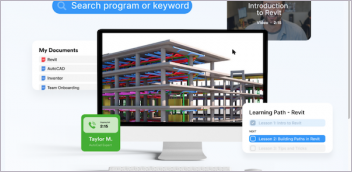

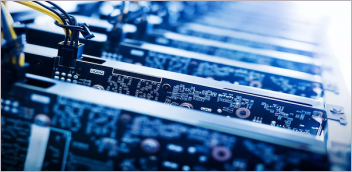
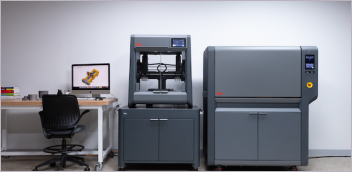