When Generative Design and Additive Manufacturing Come Together
Mergers and acquisitions forge new path for the duo

Finding the need for a powerful design software for metal 3D printing, Desktop Metal developed its own software, called Live Parts. Image courtesy of Desktop Metal.
Engineering Resource Center News
Engineering Resource Center Resources


Latest News
February 7, 2020
Generative Design (GD) and Additive Manufacturing (AM) is, many believe, a perfect combo, a match made in manufacturing heaven. Each brings out the best in the other. Each has its own strengths, but together they are formidable.
As a way of modeling complex 3D forms, GD algorithms often produce membrane-like lattice structures unimaginable to human engineers, and impossible to construct manually in conventional modeling software. Such forms are also impractical to produce using traditional machining. AM is very often the only reasonable means to fabricate the geometry proposed by GD algorithms.
Similarly, AM is a sophisticated manufacturing technology looking for a challenge. Geometry conceived in classic parametric CAD programs is too simple to benefit from AM. To justify investing in AM, not just in the hardware and material costs but also in dedicated training and process development, pioneering enterprises need a new kind of software that can design unprecedented topology. GD turns out to be this type of software.
In the last decade, the union of GD and AM is getting stronger, sealed in a number of notable mergers and acquisitions.
PTC’s Path to Generative Design
In November 2018, PTC snatched up the generative design software startup Frustum for $70 million. PTC was credited with advancing parametric CAD through its flagship product Pro/ENGINEER, later rebranded as PTC Creo. Frustum, on the other hand, is a different breed of modeler. It’s a generative design software that seeks to leverage additive manufacturing (AM).
In the post-acquisition Q&A, Jesse Coors-Blankenship, founder of Frustum and Sr. VP of Technology at PTC, pointed out his software could let PTC users “create complex geometries optimized for additive manufacturing; and deliver better products faster.” Furthermore, he noted, “With generative, engineers can take advantage of advanced manufacturing techniques and embrace additive manufacturing.”
“Creo will be able to recommend design approaches using generative design,” said PTC in its announcement of the acquisition. Jim Heppelmann, president and CEO of PTC, noted, “Frustum will elevate Creo to a leading position in the world of design and simulation.”
An Additive Twist to MSC Software
Last June, Hexagon’s Manufacturing Intelligence, a division of Hexagon, acquired AMendate, a German-based startup with software that generates and optimizes designs specifically for AM. The acquisition brings AMendate under the wings of Hexagon’s MSC Software, the division dedicated to simulation.
“The AMendate acquisition directly addresses a major obstacle during design for companies shifting to additive manufacturing processes,” said Paolo Guglielmini, CEO, MSC Software, in the announcement of the acquisition. “It enhances our Smart Factory solutions by minimizing time-to-print.”
Such acquisitions show CAD and PLM titans’ appetite for GD startups, now becoming an essential ingredient in their strategy to conquer AM. Developing one’s own GD technology from scratch is not impossible, but acquiring a promising startup is a much quicker path.
Dreamcatcher is Dead; Long Live Dreamcatcher
Having developed its own generative design technology and tested it in its Project Dreamcatcher, Autodesk didn’t feel the need to go hunting for startups. Dreamcatcher no longer exists—for good reasons. The technology has been integrated into Autodesk Fusion 360, a cloud-augmented CAD/CAM/CAE suite, and Netfabb, an AM design and simulation program.
In February 2019, when ABI Research published its Generative Design Competitive Assessment, Autodesk claimed the top spot. The other vendors in the list were ANSYS, Altair, Autodesk, Dassault Systèmes, GRM Consulting, ParaMatters, PTC, nTopology, and Siemens.
“Autodesk emerged as the leader with innovative capabilities and an integration of generative design tools within its Fusion 360 product, and Siemens came up second, setting itself apart with the generative design tools for electrical systems development in its Capital software suite. Siemens has also built generative design tools into its HEEDS, Mentor Graphics, NX, NX Nastran, and Simcenter 3D products,” according to Pierce Owen, Principal Analyst of Industrial Solution, ABI Research. “Meanwhile, PTC topped out the innovation scores thanks to the capabilities of Frustum, a recent acquisition.”
The Hardware Maker’s Software
Desktop Metal’s core business is developing and selling metal-based 3D printing systems. Nevertheless, finding the need for a robust GD software for its systems, the company decided to develop one. The outcome, currently still in development, is called Live Parts.
Live Parts is described as an interactive modeling software with built-in FEA (finite element analysis) validation. Recent Beta upgrades to the software include the ability to use AM design constraints. In other words, if you tell the software you plan to produce your part in AM, the software is intelligent enough to avoid the type of geometry that will cause problems in AM production.
“Live Parts runs in the cloud on NVIDIA GPU-accelerated virtual machines to deliver real-time generative design to any device with an internet connection,” the company explained.
Interactive GD and the GPU
Initially, Frustum came online as a cloud-hosted software, but in October 2018, it released a Windows OS version. Explaining the strategy shift, Coors-Blankenship said, “The web version doesn’t give us access to the GPU [in the user’s personal machine]. We’re introducing what we call interactive generative design. In order to realize that, we really needed to be able to leverage the CPU and GPU directly on the user’s machine.”
GD’s algorithm-driven method—running simulations and experimenting with hundreds of design variants to identify the best possible topology—is a compute-intensive process, best executed on highly-parallel GPUs. To make this process “interactive” means to produce the optimized results in near-real-time speed, without subjecting the user to wait for the number crunching. This in part explains Frustum’s need to harvest the GPU’s processing power.
“If you move the location of a pin or a hole in the Windows version, for example, the design will automatically update,” Coors-Blankenship said. “To make that level of interactivity possible, we need to access the CPU and GPU on your local machine, because the software can then respond without the lag time.”
Similarly, ANSYS achieved its “interactive simulation” with Discovery Live by leveraging NVIDIA GPUs. Whereas traditional simulation software requires a certain wait time to process and reveal the results, Discovery Live promises instantaneous results. For the software to run, the system requires a professional-class NVIDIA GPU.
Doing the Heavy Lifting in Lightweighting
As automakers and aerospace firms look to large-scale AM projects as a way to consolidate assemblies and develop light-weight designs, GD software’s importance is expected to grow. It makes independent GD startups such, such as ParaMatters and nTopology, attractive acquisition targets. It also makes the GPU an essential part of the engineers’ equipment and server setups.
Subscribe to our FREE magazine,
FREE email newsletters or both!Latest News
Related Topics
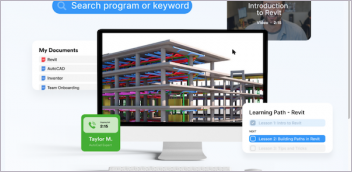

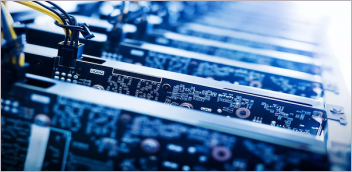
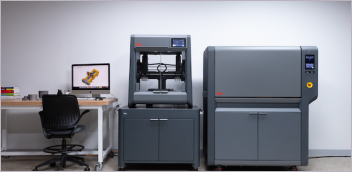