Latest News
December 1, 2006
By Kishore Boyalakuntla
The guiding principle of material use—to use as little as possible to meet design requirements—hasn’t changed in decades. It might be the only facet of material use that hasn’t.
Material use has always been a fundamental element of product design, but over the last few years the factors influencing material choice have grown increasingly complex. Costs for basic metals, particularly copper and steel, have been rising for years with no signs of ebbing. The spiraling cost of oil drives up the price of plastics, which not so long ago represented a cost-effective replacement for expensive metals.
The image on the left shows a clutchplate design before analysis. On the right, the image shows our clutchplate design under regular loads.
In addition to the purchase price, companies doing business in the European Union must now comply with strict new regulations for use and disposal of hazardous materials and non-hazardous materials that represent long-term environmental threats. Finally, product lifecycles are shrinking. Material choice and use are major factors in designing products with a set lifespan and predictable failure rates. Products with less mass over a shorter lifespan have better profit margins than products with extra mass and the same lifecycle.
In addition to properties like weight, strength, and heat resistance, designers must also consider disposal costs. These issues complicate the product designer’s decisions for materials that can meet design requirements. MCAD and CAE technologies are pivotal tools in developing products for optimal material use. Parametric MCAD/CAE tools enable engineers to experiment with different geometries for parts and subassemblies without manually recalculating the effects on the rest of the design.
MCAD and CAE software cannot, however, tell the designer how a new design will perform as a physical object, or whether a material with different properties might perform better in a given task than some other task. Those tasks are your analysis software’s responsibility and, until about five years ago, only trained analysts using complex analysis software could anticipate a design’s performance. Since then, however, desktop analysis software has put those capabilities in front-line designers’ hands. Gains in accuracy and ease of use enable designers to test material performance and minimize mass throughout the design process without risk of causing expensive design errors. Companies that have infused analysis into their design processes have already improved quality and shortened design cycles. Now they’re positioned to gain an edge in a world increasingly concerned about the environmental and societal impacts of the products it manufactures, uses, discards or recycles.
Analysis technology’s most obvious role in smart material use is for optimization. Optimization means designing parts and assemblies with as little mass as possible, yet with enough to resist failures under normal operating conditions.
These two clutchplate images depict iterations of the gradual reduction of the clutchplate’s thickness.
Paired with a good MCAD package, analysis software is a key tool for optimizing designs without driving up production costs. It is a low-cost alternative to physical prototyping to test every design iteration, which for years was the only way to determine before production how well a new product would perform. Prototypes are expensive and time consuming to build—every one is a custom job. As the only vehicle for predicting a product’s performance, prototypes limited how aggressively designers could reduce mass to save material. With each failure likely to cost another prototype, designers were less likely to reduce mass aggressively, preferring instead to accept the extra weight and cost as the price of meeting deadlines and controlling development costs. While each individual unit was no worse off for the extra mass, costs mount quickly over large production runs. With steel prices anywhere from $500 to $750 per ton, an extra 1.5 pounds of steel in a truck brake assembly erodes the profit margin on each unit.
Together, analysis and MCAD software provide a cost-effective alternative to prototyping that encourages designers to experiment with lighter-weight designs. Most companies still prototype their designs before production, but they only need one or two at the most, and those prototypes perform better.
In a design process based on MCAD and analysis, designers create parts geometries in their MCAD package. When the part or assembly is fully modeled, designers use analysis software to apply varying forces to different surfaces to simulate real-life conditions. The analysis software reports on properties such as deflection, fluid flow, and mechanical collisions. Designers use these initial results to modify the design for top performance. Then they can start looking for material savings.
For example, if an I-beam shows almost no deflection under a standard load at three-quarters of a centimeter, the designer might reduce its thickness in gradual increments to 0.3 centimeters and find it still supports the load. At 0.25 centimeters, however, finite element analysis shows that the beam deforms too much to meet design requirements. The designer stays with 0.3 centimeters, which is less than the original thickness but still provides a comfortable safety margin over the failure point.
This image depicts the thickness that the engineer chose to minimize material use while still exceeding design requirements.
The designer opts to re-design the component using a lower performing polycarbonate that costs the same as the original choice. To compensate, the designer adds mass to the housing design so it won’t deflect when it gets hot. Analysis reveals that the added mass resists failure and doesn’t hamper the unit’s performance. In this instance, analysis technology helped the designer reduce material costs by adding mass—using more polycarbonate, but at a lower long-term cost.
Choosing the best material for a job and deciding how much of it to use is one of a designer’s most basic challenges. With an ever-growing web of cost and regulatory issues complicating the task, designers need tools that automate and simplify material decisions. Desktop analysis software provides the combination of easy use and accuracy that can help them make the right decisions.
Kishore Boyalakuntla is national technical manager for analysis products at SolidWorks. Send your comments about this article through e-mail by clicking here. Please reference “Waste Neither Time, December 2006” in your message.
SolidWorks Corp.
Concord, MA
Subscribe to our FREE magazine,
FREE email newsletters or both!Latest News
About the Author

DE’s editors contribute news and new product announcements to Digital Engineering.
Press releases may be sent to them via [email protected].
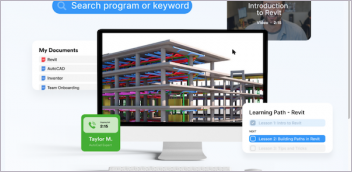

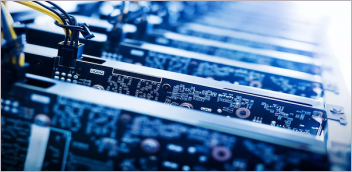
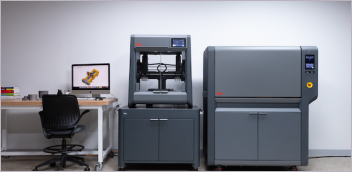