
Bi-modulus elastic model is a feature in MultiMech 19.0 that allows users to realistically predict the mechanical behavior of carbon fiber. Image courtesy of MultiMechanics.
Latest News
May 1, 2019
MultiMechanics, a developer of multiscale composite modeling and simulation software, has announced the release of MultiMech 19.0. MultiMech is a multiscale finite element software platform that helps companies virtually predict failure in advanced materials at an unprecedented level of speed and accuracy.
MultiMechanics says MultiMech offers true multiscale technology, extending the flexibility and robustness of Finite Element modeling down to the microstructural level. The result is the ability to strongly couple macro and micromechanical responses, integrating materials engineering to part design.
MultiMechanics was founded in 2010 to provide new solutions for simulating composite performance. Using standard CAE solutions on these advanced materials was proving to be inefficient in both time and accuracy. Testing and certification was costing manufacturers millions. To help address these challenges, MultiMechanics wrote an all new solver designed specifically for composites. One of the company’s first clients was the US Army Research Laboratory, which needed better software to explore impact applications for composites.
MultiMechanics says the 19.0 update of MultiMech delivers new material models, new damage scenarios, faster run times, and expands integration with commonly-used FEA systems.
MultiMechanics claims the solver in MultiMech 19.0 is 1.5 times faster than the previous version, allowing engineers to take advantage of the accuracy of a concurrent multiscale approach while benefiting from increased speed.
The software now offers parallel runs in Optimizer, which reduces the runtime of DoE jobs using MultiMechanics’ Optimizer to get answers faster.
There are new material and failure models, including continuum damage models for orthotropic materials and new damage laws that will allow users to capture unique material behavior with higher accuracy.
MultiMech 19.0 offers enhancements to the nonlinear solver, with an improved automated time step and optional displacement convergence check, as well as the ability to check for large displacements in the nonlinear solver.
The MultiMech material database has been redesigned and enhanced to speed up the workflow. Users can now create their own database of material cards to be used with MultiMech, including material definitions for individual constituents, as well as define an entire Representative Volume Element as an entry to the material database. MultiMechanics says it is easy to create, import, export and share a material database with other users within an organization.
MultiMech 19.0 includes a streamlined tool to run Dynamic Mechanical Analyzer (DMA) tests virtually. With this tool, users can characterize the viscoelastic behavior of complex microstructures in all directions, at different temperatures and frequencies.
Also new in MultiMech 19.0 is ANSYS DX integration. Users can perform Optimization studies at both the macro and micro scale using ANSYS DX’s unique capabilities.
The update is now available to registered users.
To learn more about MultiMechanics MultiMech 19.0, click here.
For case studies and a product overview, click here.
For a video on using MultiMech, click here.
For a replay of the release webinar, click here.
Read the DE report on the release of MultiMech 19.0.
See why DE’s Editors selected MultiMech19.0 as their Pick of the Week.
Sources: Press materials received from the company and additional information gleaned from the company’s website.
More MultiMechanics Coverage
Subscribe to our FREE magazine,
FREE email newsletters or both!Latest News
About the Author

DE’s editors contribute news and new product announcements to Digital Engineering.
Press releases may be sent to them via [email protected].
Related Topics
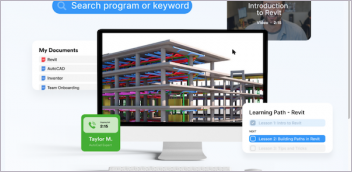

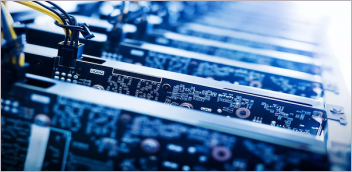
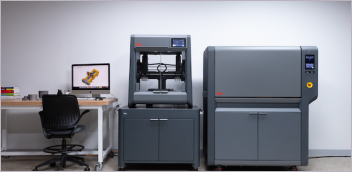