Latest News
August 1, 2006
By Ann Mazakas
With help from GibbsCAM, Victory builds the next generation of motorcycles.
Imagine yourself in Las Vegas. You’ve never played dice, but you break the bank on your first roll. Farfetched? Of course, but something like that actually happened when Victory Motorcycles introduced the first all-new American-made motorcycle from a major company in nearly 60 years—the Victory V92C. Before it was even available to consumers, Cycle World magazine named it “Best Cruiser.”
That was back in 1998. Today, Victory’s winning ways continue, and accelerate, with its latest cruiser, the Victory Vegas Jackpot, providing manufacturing lessons you can take to the bank.
In its early days, Victory’s fabrication equipment and build area was located in a 12-foot wide converted hallway in Osceola, WI. Today, those functions are handled from a new, 127,000 square foot advanced development facility in Wyoming, MN. Here, lead development machinist Jerome Jasmer’s prototyping department is geared to produce the next generation of world-class motorcycles.
![]() |
Victory Motorcycles. |
> > The chromed bracket is mounted on the rear fender of the Victory Vegas Jackpot lending a finished custom appearance even without the passenger seat attached.
Victory’s designers and engineers create their designs in Pro/Engineer. These designs are then sent to Jasmer’s fabrication shop where the CAD data is readied for real-life manufacturing with GibbsCAM from Gibbs and Associates. To enable Pro/E data to be transferred into and out of GibbsCAM, a Pro/E data exchange option, which is built on PTC’s Granite Interoperability Kernel, is offered. Granite allows GibbsCAM to directly access geometry and attributes in the Pro/E file.
Jasmer created toolpaths directly onto the Pro/Engineer solids data using GibbsCAM SolidSurfacer and then points out a tricky bracket as an example of the application’s ease of use.
![]() |
GibbsCAM |
< < The underside of the passenger seat bracket as it was imported into GibbsCAM.
“We prototyped a bracket for holding the passenger seat onto the back fender of the new Vegas Jackpot,” he recalls. “We wanted it to have a custom look, both when the passenger seat was mounted and when it was not, so exposed bolt holes on the fender were out of the question.”
Compounding his challenge: almost every surface was contoured—the only flat surfaces were at the bottom of the counter bores and on the seating surfaces opposite the counter bores.
GibbsCAM made it easy for Jasmer to try different machining strategies, compare cycle times, and run the simulator to compare finish quality before adopting the process most ideal for creating the part.
![]() |
GibbsCAM |
> > GibbsCAM’s Cut Part Rendering allows the machining process to be simulated and visually verified.
“On some of the steep grooved areas,” he points out, “I used a 3mm or even a 2mm ball-end mill to get down into tight areas. Of course, it had to clean up well so we could chrome it. With GibbsCAM’s associativity, I could change my machining parameters or tooling and easily regenerate the toolpath. Then using GibbsCAM’s Cut Part Rendering simulation I could really see what the tool was going to do and whether I was going to end up with a little mark where the tool stopped.”
![]() |
GibbsCAM |
< < Jerome Jasmer and Gordon Nelson, Design Technologist, study toolpath issues using GibbsCAM’s Cut Part Rendering simulation.
Iterating through a variety of different tooling and parameter settings, Jasmer was able to come up with the ideal combination that would produce the necessary surface finish.
GibbsCAM’s Cut Part Rendering graphically depicts the machining process for visual verification before sending the program to the shop floor. Jasmer also uses it for another function: “Because I’m running my toolholders close to everything, I’ll preview the toolpath in a virtual environment first just to make sure nothing interferes. What you see in Cut Part Rendering is what the machine’s going to do. It prevents a lot of scrap and crashes.”
![]() |
GibbsCAM |
> > The top of the passenger seat bracket as it was imported into GibbsCAM.
At every step, Jerome Jasmer found a GibbsCAM functionality to make prototyping an intuitive and productive process. “Maybe it’s because GibbsCAM works the way that machinists think that makes it so easy to use,” observes Jasmer. “Because of this, I really enjoy working with GibbsCAM. And that translates into my being very productive.”
And that translates into another winning hand for Victory Motorcycles and the Victory Vegas Jackpot.
Ann Mazakas is the owner and president of Intelligent Creations LLC, a provider of services to the manufacturing industry. Send your comments about this article by clicking here. Please reference “Victory, September 2006” in your message.
Interested in receiving a free poster of the Victory Vegas Jackpot motorcycle along with information on what GibbsCAM can do for your milling, turning, and multi-task machining? Click here and enter offer code “MDM-016DE” to request your free poster and GibbsCAM information. Offer valid until October 31, 2006 or while supplies last.
Gibbs and Associates
Moorpark, CA
PTC
Needham, MA
Victory Motorcycles
Wyoming, MN
Subscribe to our FREE magazine,
FREE email newsletters or both!Latest News
About the Author

DE’s editors contribute news and new product announcements to Digital Engineering.
Press releases may be sent to them via [email protected].
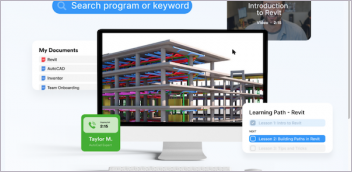

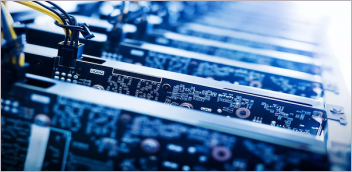
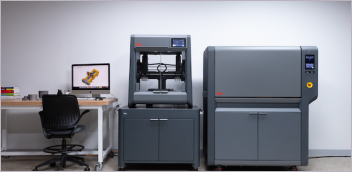