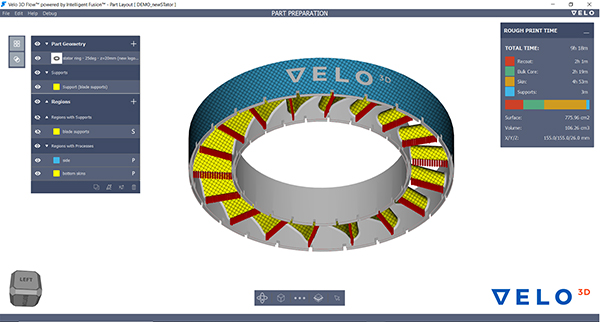
Flow is a simulation-driven, process aware print preparation software. Flow is made to enable predictable print outcomes while reducing print preparation time. Image courtesy of VELO3D.
Latest in 3D Printing Simulation
3D Printing Simulation Resources


Latest News
February 19, 2019
VELO3D, a 3D printer manufacturer, announces advances to its print preparation software, Flow. Driven by a integrated simulation engine, Flow is made to provide predictable print outcomes, while its native CAD workflow controls performance consistent with the design intent and helps reduce print preparation time, according to VELO3D. Working in concert with VELO3D’s Sapphire system Flow enables next-generation SupportFree additive manufacturing for parts.
Flow is specifically designed for Sapphire, VELO3D’s laser fusion metal additive manufacturing system. It includes tools that help with part orientation, support generation, simulated print predictions, per-surface process application, slice composer and process review. As a result, manufacturers can now print complex part geometries SupportFree, enabling volume manufacturing of parts, the company reports.
VELO3D’s ability to print low angles and overhangs below 5 degrees, as well as large inner diameters and tubes up to 40 mm without the need for supports, eliminates the need for difficult post-processing cleanup, the company reports.
Flow key features include:
A new physics-driven simulation engine has been built from the ground up, optimized for VELO3D process capabilities and the Sapphire system, the company reports.
The simulation utility predicts the print outcome, applying print deformation correction and validating the execution feasibility of the print prior to starting the build process.
A composer detects geometric features and applies the optimized print process to specific features.
The integration of print preparation, simulation and composing capabilities into a single software eliminates incompatibilities, simplifying the workflow. Native CAD workflow enables new user experience with smart selection, refinement and filtering of part features and reduces hundreds of manual steps to a few clicks.
“Build preparation software has always been an afterthought,” says Benny Buller, CEO of VELO3D. “VELO3D’s strategy is to offer an integrated hardware, software and process solution. The system is process driven, where the software manages the hardware and can predict and control the outcome. It is the only way to fulfill our mission to manufacture any design, assure accuracy and consistency and thus take additive manufacturing mainstream.”
More Info
Sources: Press materials received from the company and additional information gleaned from the company’s website.
Subscribe to our FREE magazine,
FREE email newsletters or both!Latest News
About the Author

DE’s editors contribute news and new product announcements to Digital Engineering.
Press releases may be sent to them via [email protected].
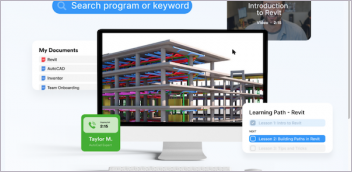

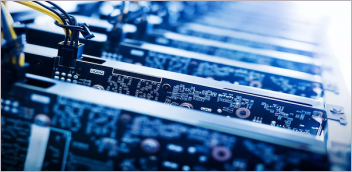
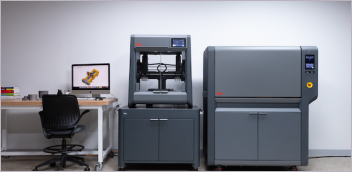