US DoE Puts $2.85 Million Toward 3D Printing Modular Wind Blades
Funding was awarded to Purdue University and its industry partners, including Thermwood, TPI Composites Inc. and Dassault Systèmes.

The Thermwood LSAM Additive Manufacturing Laboratory. Image courtesy of Thermwood
Additive Manufacturing News
Additive Manufacturing Resources


Dassault Systemes

Latest News
October 13, 2023
The U.S. Department of Energy (DOE) has awarded $2,849,000 to the Composites Manufacturing Simulation Center (CMSC) of Purdue University and its industry partners, including Thermwood, TPI Composites Inc., Dassault Systèmes, Dimensional Innovations, and Techmer PM.
The DOE-funded Purdue program, “Additive Manufacturing of Modular Tools with Integrated Heating for Large-Scale Wind Blade Manufacturing,” is led by Eduardo Barocio, director of the Composites Additive Manufacturing and Simulation (CAMS) Industrial Consortium.
“The primary goal of the program is to develop the foundation for automation in manufacturing of tooling for large-scale wind blades that can accommodate continuous changes in blade geometry and scale,” says Barocio. “This will be accomplished through modular construction, wherein modules are 3D printed with carbon fiber/thermoplastic composites by a technology called extrusion deposition additive manufacturing, which was first developed at the DOE’s Manufacturing Demonstration Facility in the Oak Ridge National Laboratory.”
Specific targets for the program include developing a module design for wind blades equal to or greater in length than 80 m; reducing the time required to manufacture and assemble wind blade tooling by at least 40% over conventional tool manufacture; enhancing tool performance by at least 15%; effecting weight reductions of by a minimum of 25% over conventional tools; and lowering the manufacturing cost of a wind blade tool by at least 35%.
Barocio is the founder and director of the Thermwood LSAM Research Lab at the Indiana Manufacturing Institute in Purdue Research Park. He is also the founding director of the Composites Additive Manufacturing and Simulation Industrial Consortium, whose mission is to shape the future of large-scale additive manufacturing by providing education, simulation tools, characterization and best practices.
“The proposed program provides the foundation for automated manufacturing technology in wind blade tooling manufacture,” says Barocio. “These same technologies can be applied to manufacturing of all the elements of the wind energy system and, as such, the program provides a pioneering development that can leverage technology within the United States for a major source of clean energy, wind.”
The program will develop and demonstrate seven specific innovations. These include automating the 3D printing of large-scale modules and developing robust joining technology and inline heating elements deposition for conduction heating. Others include 3D printed cooling channels for convective cooling; new composite materials systems for economy and performance; support frame weight reduction; and tool deformation prediction and control, with decision-making by a digital twin for 3D printing design and manufacturing.
Overall, the DOE awarded $30 million for 13 projects across 10 states that will reshape the design, materials, and sustainability of large wind blades for offshore and land-based applications. Large wind blades face significant challenges in design and materials, particularly for offshore applications. The selected projects will tackle these challenges, focusing on sustainability, efficiency and technological advancements to make wind energy more effective.
Advanced lightweight composite materials have emerged as pivotal in enhancing wind power generation and vehicular applications. The DOE projects were picked for their potential to bolster the manufacturability of these composite materials. The projects focus on three primary challenges: large wind blade additive manufacturing; additive manufacturing of wind turbine components; and advanced manufacturing, materials, and sustainability for large wind blades.
“These projects, alongside the Purdue program, will address the remaining challenges in wind turbine manufacturing and build on previous work in automation, digitalization, wind blade sustainability, and modular blade construction and joining,” says R. Byron Pipes, executive director of the Composites Manufacturing Simulation Center at Purdue. “Successful demonstration of automation in the manufacture of alternate energy systems can enhance their wider use while sustaining the industry in the United States.”
In other DoE funding-related news, GE Research has selected voxeljet as its partner for a $14.9 million award in federal funding for the development and commercialization of the large sand binder jet 3D printer, also referred to as Advanced Casting Cell (ACC), to accelerate the U.S. transition to clean power.
Sources: Press materials received from the company and additional information gleaned from the company’s website.
More Dassault Systemes Coverage
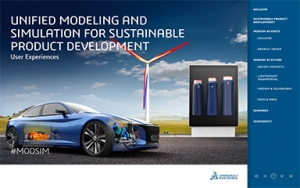
Subscribe to our FREE magazine,
FREE email newsletters or both!Latest News
About the Author

DE’s editors contribute news and new product announcements to Digital Engineering.
Press releases may be sent to them via [email protected].
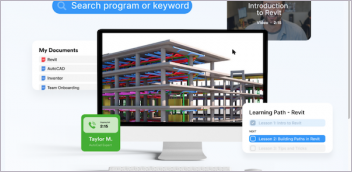

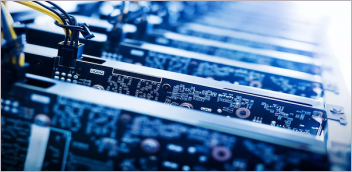
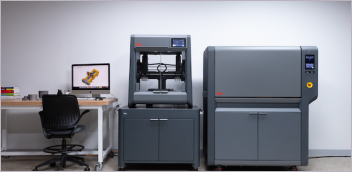