uPrint Sweepstakes Winner Explains Benefits of Personalized Design
Latest News
July 13, 2012
It’s been a little more than a month since executive editor Steve Robbins and I journeyed to Redwood City, California, and delivered a 3D printer to DE Rapid Ready Sweepstakes winner Maegan Spencer, a R&D engineer at Avinger Inc. So last week, I returned to find out how Maegan has been using her prize, a uPrint SE 3D Print Pack.
Avinger, which develops cutting-edge micro devices to treat peripheral artery disease, is no stranger to 3D printing. It’s part of the way the company prototypes and tests new devices under consideration. In fact, the professional-grade 3D printer that Avinger engineers relied on was having a difficult time keeping up with the volume of print jobs in the queue. Even as it operated 24/7, the company still needed to send out some overflow print jobs to service bureaus to cope with the demand. So the uPrint SE that Maegan won was a welcomed addition.
But the benefits of the secondary printer were not confined to higher volumes. The ability to print concepts on the fly led to custom-designed troubleshooting devices for work and fun projects to enrich the staff’s weekend adventures.
Personal Creativity
From her waterfront office, Maegan greeted me with several devices produced in the new 3D printer: a personal iPad stand (designed by Nick Spinelli, Avinger), a tube cutter (designed by Charles McNall, Avinger), and a tailor-made test-device holder (designed by Charles McNall, Avinger). Why did someone feel the need to design an iPad stand, I asked her. Couldn’t he just go to the nearest Apple store and buy one off the shelf?
“We’re engineers. We like to design our own devices,” Maegan reminded me. “We’ve all looked at the company printer and thought, ‘What if I can just print whatever I want?’ A lot of those things have now been printed out.”
Maegan, who cuts the waves and climbs cliffs for fun, uses the 3D printer to create and produce her own crampons (traction-producing gear for ice climbing) and surfboard fins. She also designed and printed a housing unit for a coffee sensor, capable of alerting her when her coffee is cool enough to drink.
In-House Convenience
Three years ago, without in-house 3D printing, Avinger engineers were routinely forced to make agonizing decisions about which versions to send to the bureaus for prototyping, and which versions to leave unexplored. “We would go back and forth on whose [design] get scaled up, whose wouldn’t—It was a big deal,” said Maegan. “Now, we can print almost anything we want to show.”
Avinger devices, designed in SolidWorks, have metal walls with thicknesses measured in 1/1,000th of an inch—in dimensions below a sesame seed’s size or the whites of a person’s trimmed fingernails. “Our devices go inside a patient’s arteries, typically between 4-6 millimeters in diameter,” said Maegan. “Fatigues and stress points on these are important for us to know about. As engineers we have intuitions about where these stresses are. In SolidWorks we can even try out some iterations and resolve these stress points and distribute the loads.”
So when engineers print 3D prototypes, they typically print parts 14 times larger than the actual size. “If I have to go into a board meeting to explain how a complex hinge mechanism works, showing the audience a CAD model immediately distances me from a large number of people who are not engineers,” Maegan explained. “What’s great about a 3D print model is, everyone can play with it as if it were a toy. You put it in their hands; they can discover how it works on their own.”
The secondary 3D printer now serves as the backup system when the primary printer is taken offline for maintenance. Avinger staff is thankful that, even when one printer is out of commission, they don’t have to deal with the turnaround time and delays associated with sending out jobs to service bureaus.
“There’s some magic about having the machine here,” said Maegan. “Sometimes, when we’re in a hurry to get something done, we have to pause the job in progress, and swap it out with more urgent jobs. When someone just had a Aha-moment, they can remove the part and change it.”
One-of-a-Kind Gadgets
The tube-cutter designed by Avinger engineers is different from a standard one you might pick up at Walmart or Office Depot. It contains a v-shaped groove, which lets engineers lay down the tube in precise alignment, and a screw-controlled pocket, which limits the cutting angle to the desired slant. “What’s nice about this is, now I don’t have to go to a machine shop and have someone cut tubes for me,” said Maegan. “And if I have to cut 20 in a row, I can set it up very easily. We designed it specifically to do one task, and we printed a couple of them so our technicians don’t have to [risk cutting themselves.] And the cuts are very consistent.”
The test-device holder designed and printed in the uPrint SE has six pockets, which allows Avinger engineers to drive six devices simultaneously. “They’re all connected through a belt, so if I turn one, all six turn,” explained Maegan. “This is specifically designed for testing our devices—something you can’t buy. This is a novel approach—getting a fixture done in a day that you can use right away. People really enjoy designing these things because you have to bring different ideas.”
In a sense, Avinger is using 3D printers not just to print the prototypes they need, but also to print the gadgets they need to improve the prototyping process.
Responsible Printing
When it comes to high-volume print jobs, Maegan and her colleagues at Avinger are judicious in their choices, partly in consideration of the impact on the environment. “We don’t want to print every idea we have, because we’re creating plastic parts that may outlive us,” she cautioned. With high volume printing, the material cost also has to be factored in as part of the budget. “So we do have to be smart about what we print. We have to make educated guesses about which ideas we should test.” Many of these educated guesses are aided by SolidWorks. By digitally simulating and weeding out concepts that are less promising, engineers can identify concepts that may not be worthy of physical prototyping.
When not engaged in professional workflow, the idle printer churns out what the staff calls “fun projects.” Maegan’s nephew was one of the beneficiaries, who received a bobble-headed action figure, courtesy of Maegan’s 3D printer.
For more, watch the video clips below where Maegan demonstrated the devices printed in the uPrint SE printer.
Subscribe to our FREE magazine,
FREE email newsletters or both!Latest News
About the Author

Kenneth Wong is Digital Engineering’s resident blogger and senior editor. Email him at [email protected] or share your thoughts on this article at digitaleng.news/facebook.
Follow DE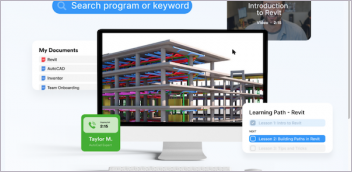

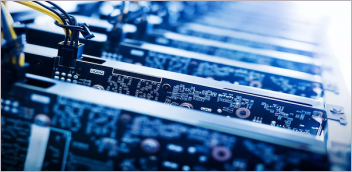
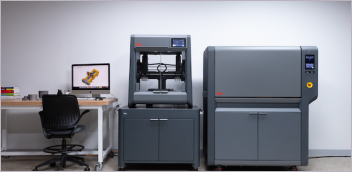