University of Michigan Researchers Tout High-Speed 3D Printing Approach
The process employs dual light sources in place of an oxygen membrane to print at 100 times the print speed of conventional offerings.

University of Michigan’s high-speed 3D printing process is a vat polymerization technique based on SLA. Image courtesy of University of Michigan.
Latest News
February 6, 2019
Scale and performance are two of the primary speed bumps in the way of using stereolithography (SLA) 3D printing techniques as a viable full-scale production method. But a research team at the University of Michigan is aiming to change that dynamic with a novel take it claims can print up to 100 times faster than conventional 3D printing processes.
While existing SLA methods and other forms of conventional 3D printing lends themselves to prototyping applications, they fall short as a substitute for injection molding practices for production runs with 10,000 parts or less, notes Timothy Scott, Ph.D., an associate professor in the Department of Chemical Engineering at the University of Michigan, and one of the authors of a paper outlining the new approach.
In particular, SLA additive manufacturing, which uses photopolymerizable resin and a light source to cure the cross-sectional layers of geometry making up the part, can be especially slow since performance is limited by the need to initiate time-consuming separation or recoating steps between the layers of the output. Print speeds in most available SLA systems range from only a few millimeters to several centimeters an hour, and the process often yields parts with ridged surfaces, which are not suitable for production-grade products, the paper noted.
Rapid, Continuous Additive Manufacturing
The University of Michigan’s research team has developed an AM system that does away with this multi-step, layer-by-layer process in favor of what it dubs a “rapid, continuous additive manufacturing process that employs volumetric polymerization inhibition patterning.” The team’s uses two illumination sources at different wavelengths to control the solidification of resin, which allows for the solidification of the resin in more sophisticated patterns. The approach also addresses the common limitation of similar technologies—that the resin tends to solidify on areas where the light shines, which can hamper production or introduce imperfections that derail the print run, Scott explains.
As the paper explains:
“Patterned illumination from below through a transparent glass window initiates polymerization of the resin, while illumination at a second wavelength inhibits the polymerization reaction immediately adjacent to the glass window, eliminating adhesion and enabling continuous operation.”
The outcome is vastly increased print speeds of approximately 2m/hour; in addition, the process is compatible with a wide variety of resins, including more viscous varieties, Scott says.
“You can use viscous resins to achieve greater accuracy of part size and the materials are also much more desirable for a finished product,” he adds. “When you are producing end parts, you need a fast process and you want to ensure you have sufficient mechanical and thermal properties. The intent of our process is to achieve both using the dual wavelength set up.”
Other companies, most notably Carbon, have commercialized other alternatives to vat printing or SLA technology. Instead of dual light sources, Carbon’s patented Continuous Liquid Interface Production (CLIP) method employs an oxygen membrane to create a thin polymerization-free window and achieve higher production speeds.
To create a proof-of-concept printer (it is not yet even a formal prototype), the Michigan development team designed a custom build head with Autodesk Fusion 360 and fabricated it out of nylon using Markforged Mark II 3D printing technology. National Instruments' LabVIEW VI was used to develop motion controls, and test models were designed using DesignSpark Mechanical 2.0 and Autodesk Fusion 360 and exported as STL files. Autodesk Netfabb 2017 also played a role in creating images slices.
Currently, the research team is talking to industry players about the possibility of commercializing the technology; it has also applied for three patents to protect the more innovative aspects.
More Autodesk Coverage
Subscribe to our FREE magazine,
FREE email newsletters or both!Latest News
About the Author

Beth Stackpole is a contributing editor to Digital Engineering. Send e-mail about this article to [email protected].
Follow DE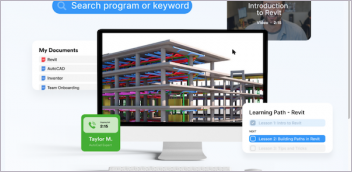

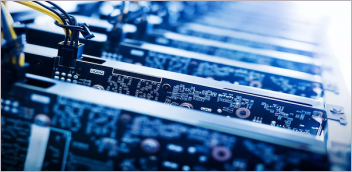
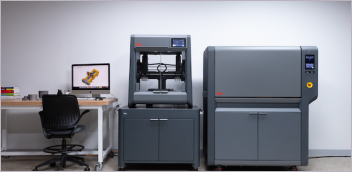