Transition to Simulation: Linear and Nonlinear Buckling
Buckling describes where structural failure can occur when compressive loads are applied to a slender structure.
Latest News
March 1, 2019
Buckle up. Where we are going, we don’t need roads. This month we’re taking a road trip into the world of buckling analysis. You may or may not have heard of this type of analysis; however, there is no doubt that you’ve witnessed the importance of this type of structural analysis at some point.
Whether designing slender fuel storage containers or predicting post-buckling behavior for a passenger car chassis design, you should consider buckling an essential component of a thorough structural analysis.
Simply put, buckling describes where structural failure can occur when compressive loads are applied to a slender structure. It’s a state in which a very small increase in loading conditions can cause a structure to collapse. We can separate buckling into two distinct categories: linear and nonlinear. Each type of analysis provides varying depths of detail, which we will discuss.
Linear Buckling
Like the approach we bounced off in a previous article about starting with a linear static structural analysis to develop a baseline and then progressing to nonlinear as required by the depth of engineering analysis required, the same concept can be applied to the study of buckling.
For starters, it’s good to complete the initial linear static structural analysis. These results will shed some light on the stress values displacement of your design. From this point, you can carry over the established loads and constraints from the linear static structural analysis then begin the buckling analysis.
Post-processing data will look familiar to modal analysis, as the results are grouped by amplitude per given mode. A numerical value associated with each mode is called the buckling factor of safety, which will highlight whether the loads applied per mode will make the structure susceptible to buckling. Buckling factor of safety is calculated as the critical load divided by the applied load.
With careful observation, you might notice that buckling factor of safety can have negative values appear in your results. These mysterious values are attributed to the direction of the force, but could also be understood as tensile loading opposing compression. A good rule of thumb is that the first mode is generally most significant, as this is where the structure is most likely to fail. If your first mode indicates values between 0 and 1, consider redesign or further analysis into the nonlinear buckling.
Nonlinear Buckling
As with all statements, there are always exceptions. If you find yourself analyzing a structure where large displacements occur prior to buckling, directional forces change during deformation prior to buckling or you’re dealing with nonlinear material properties, it’s safe to say that you should be pursuing a nonlinear approach. An oft-considered reason for skipping straight into a nonlinear analysis is the benefit of studying post-buckling behavior.
How will the structure behave physically after it buckles? Do you have symmetrical or asymmetrical buckling? Results in the nonlinear approach reflect closer to real-world values for what to expect with a buckling structure as you are not confined to the limitations of a linear analysis.
Arc length control method is commonly used to develop a nonlinear solution. Using this method, you can access post-processing result plots of load factor relative to displacement. This plot is generally coined as the equilibrium path to which the behavior of buckling could be accurately described.
The focus of a buckling analysis is on a structure’s stability, whereas a standard static analysis analyzes performance. Most structures actually fail from structural collapse due to buckling, and not from maximum yield stress. Be cautious in trusting linear buckling results, as its limitations generally draw large variations from that of nonlinear results. A careful understanding of limitations will prove vital in getting timely and accurate results in your next engineering task.
Subscribe to our FREE magazine,
FREE email newsletters or both!Latest News
About the Author

Donald Maloy is a consultant analyst based in the greater Boston area. He also works as a certified simulation and mechanical design instructor for a software reseller.
Follow DE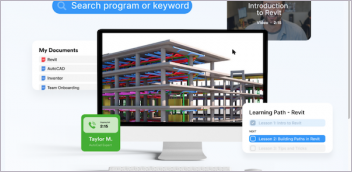

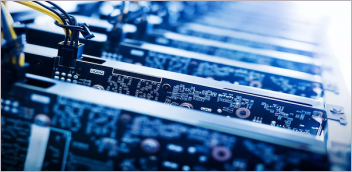
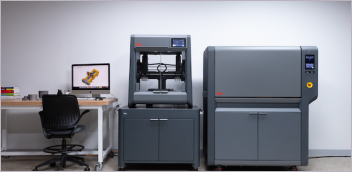