Latest News
November 17, 2020
Titan Robotics, Ltd. today announced a strategic collaboration with Jabil Inc. to accelerate the adoption of large-format, industrial additive manufacturing. Jabil Engineered Materials, a unit of Jabil, which develops innovative polymer formulations and compounds at its ISO 9001 Materials Innovation Center, is working with Titan to qualify and integrate customized materials for use on Titan’s pellet-based Atlas 3D printers.
Together, the companies are driving the production of large-format tooling for applications in sheet metal forming, composite layups, welding fixtures, molding, casting patterns and end-use parts on Titan Atlas printers to meet a need for increased part strength and faster printing speeds, companies say. Jabil’s specialized materials science expertise, combined with Titan’s robust printing performance, are ideally suited for addressing the growing list of rigorous industrial, as well as medical, defense and aerospace applications.
“Titan and Jabil are fulfilling a joint mission to move additive manufacturing into serial production and advanced manufacturing,” says Titan Robotics partner and CTO, Bill Macy. “By choosing Jabil’s engineered materials customized for applications with high-throughput pellet printing on the Atlas, we can help customers reduce costs, create products with mass customization, reduce cycle times and innovate quickly.”
Titan and Jabil have tested and validated new pellet formulations of Jabil’s carbon fiber reinforced nylon materials, which are designed to produce stronger, lighter and more flexible parts.
“Jabil takes a polymer science approach to developing engineered materials,” says Matt Torosian, director of additive product management at Jabil. “All of our materials are designed exclusively for additive manufacturing, so Titan receives pellets that embody all the necessary attributes to optimize performance and reliability.”
The collaboration between Titan Robotics and Jabil gives customers greater choices from a variety of high-performance pellet materials as well as the opportunity to create custom compounds to address specific requirements. By teaming, both organizations also offer an intermediate yet vital step to validate materials and part designs before customers print extremely large and costly, high-end final parts.
As an authorized distributor of Jabil’s 3D printing pellet materials, Titan will support Jabil’s ongoing development of new material formulations for pellet extrusion 3D printing on the Atlas platform.
About Pellet Extrusion on the Atlas
Pellet extrusion on the Atlas enables production additive manufacturing solutions by printing directly with plastic pellets instead of traditional filament. Pellet extrusion increases throughput and decreases material costs, while also expanding the materials that can be 3D printed.
Pellet Extrusion on the Atlas enables order of magnitude material cost savings compared to traditional 3D printing filaments and the ability to print with hundreds of grades of resins. From flexible, low durometer materials up to high-performance and highly filled engineering materials, pellet extrusion on the Atlas uses open market materials.
Pellet Extrusion on the Atlas also enables the ability to print large, production parts due to the faster print speeds and higher throughput on the Atlas. Flow rates range from 1 lb to 30 lbs per hour and prints speeds can top out at 30,000 mm/minute, reducing production time from days to hours.
The combination of reduced feedstock cost and faster print speeds provides reduced operational costs and faster cycle times with organic capacity.
Sources: Press materials received from the company and additional information gleaned from the company’s website.
Subscribe to our FREE magazine,
FREE email newsletters or both!Latest News
About the Author

DE’s editors contribute news and new product announcements to Digital Engineering.
Press releases may be sent to them via [email protected].
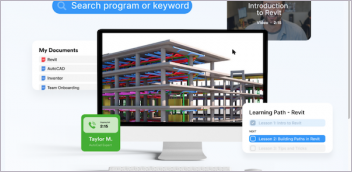

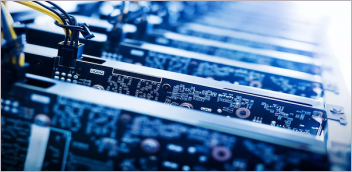
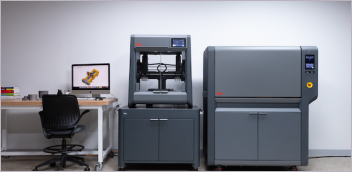