Thermwood Developing Large-scale Additive Manufacturing

This massive extruder is the business end of Thermwood’s equally massive AM system still in development. Courtesy of Thermwood.
Latest News
August 5, 2015
The news has been full of speculation lately that the 3D printing bubble has finally popped. Some columnists are attempting to correlate the massive interest in additive manufacturing (AM) to the Dot-com Bubble in the late 90s. That particular collapse brought down entire companies, and the business news has been watching (maybe hungrily) to see if the same happens with AM.
Even a serious financial meltdown wouldn’t spell the end of AM. The technology isn’t really so reliant on a couple companies that financial upheaval would kill it, and news out of Thermwood is proof. The CNC router company announced it would be working in-house to develop large-scale AM to add to its production facilities.

It seems likely that Thermwood developed its interest in AM as part of the group that worked on Local Motors’ Strati for the International Manufacturing Technology Show 2014.
The Strati was built using BAAM and secondary tooling was provided by Thermwood’s 5 Axis Model 70. It isn’t hard to imagine one of Thermwood’s engineers looking at the AM process and thinking, “We could do that.”
Like BAAM, Thermwood’s AM system will be large. Based on an existing frame for the Model 77, the system will be around 60 feet in length with a build envelope of 10x10x5 ft. Note those are feet, not inches. Thermwood will be using a carbon graphite filled thermoplastic as its material of choice.
The process involved is called near net shaping, and is essentially super-fast FDM using an oversized extruder. The extruder and associated support equipment itself measure in at a 20HP, 1 ¾ inch diameter, 24-1 L/D, and is capable of squeezing out over 100 pounds of material per hour.
The quick-and-dirty AM build produced by such a large system will require additional manufacturing to complete, and Thermwood is ready. The system will switch to subtractive mode once the additive process has finished. The six-axis print head will be joined by a five-axis CNC machining to produce complete (or near complete) products from one system.
The system is still in development, but is already capable of producing parts. According to its company blog, Thermwood is looking forward to putting the system in operation:
“Thermwood believes it is in a unique position to pursue this emerging technology since, at one time, it was a plastic processing company that operated large plastic extruders in a production environment. Thermwood is already a major manufacturer of the ‘Subtractive’ machinery part of the equation and this same technology is the basis of the ‘Additive equipment.”
Below you’ll find a virtual tour of Thermwood.
Source: Thermwood
Subscribe to our FREE magazine,
FREE email newsletters or both!Latest News
About the Author
John NewmanJohn Newman is a Digital Engineering contributor who focuses on 3D printing. Contact him via [email protected] and read his posts on Rapid Ready Technology.
Follow DE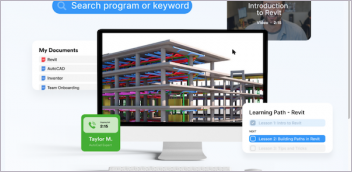

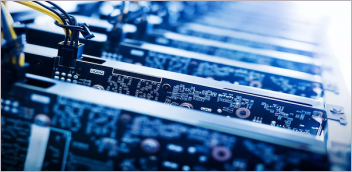
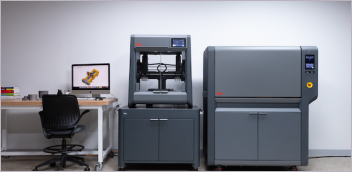