There’s More to Miniaturization than Size
Latest News
August 1, 2017
Printed electronics stand poised to transform the semiconductor industry, but probably not in the way that you expect. Early adopters of the technology hoped that lower manufacturing and material expenses would help reduce the cost of devices entering the market, but these benefits have yet to be realized. On the brighter side, the rewards delivered by the new fabrication process are turning out to be more profound than lower sticker prices.
The reason printed electronics have not delivered the expected cost reductions is that the complexity of the manufacturing processes has eliminated much of the cost savings. According to IDTechEx (https://goo.gl/m23vMZ), the technology will likely experience “pharmaceutical-like pricing” in the short term, driven by producers’ need to recoup their initial investments in new equipment and materials. As a result, the technology can offer greater performance—but only at a higher price than printed circuit board (PCB)-based devices.
Nonetheless, the pairing of additive manufacturing with other emerging technologies enables form factors that clear the way for a whole new class of applications, such as wearable and structural electronics. Increasingly, manufacturers focus their efforts on creating value from factors like thinness, reduced weight, stretchability and flexibility. These factors have proven to be stronger drivers than cost reduction.
Manufacturing Enters the Fast Track
Today, manufacturers rely heavily on traditional semiconductor processes to fabricate electronics. Unfortunately, these systems increasingly fail to deliver the performance necessary to meet market demands because they introduce inefficiencies that deny manufacturers the agility to react to production challenges.
The source of these inefficiencies lies in production systems’ inability to handle design fixes and modifications quickly and cost-effectively. The changes range from rerouting a printed circult board trace or modifying a component value to substituting a different part.
Making these types of alterations at the design stage can significantly impact systems all the way down to the factory floor. Plant managers may have to reconfigure production lines, change the bill of materials and update technical documentation. All this costs time and money, extending time to market and raising the price of the product.
Recent technological advances, however, enable printed electronics to address these shortcomings. Companies like Pulse Electronics and Optomec have introduced a generation of printers that enable direct printing onto 3D surfaces. The technology allows manufacturers and engineers to create and integrate various electronic components—such as antennae, sensors and electrical circuits—on a flexible substrate.
These manufacturing capabilities have the potential to revolutionize how products are made. In particular, the agility that they impart allows engineers to update designs simply by adjusting printer instructions.
Pushing the Limits of Miniaturization
As impressive as printed electronics’ streamlining effect on manufacturing is, its greatest impact will be in design. By changing the mechanical properties of electronics, the flexible and stretchable technology will expand the limits of miniaturization by redefining the form of electronics and the concept of usable space.
In the wearable arena, device designs no longer have to accommodate rectangular shapes and rigid surfaces. Devices can conform to users’ bodies and seamlessly integrate into what they wear. Printed electronics also give designers new opportunities for using flexible sensors and displays. Another area where transformation of the concept of usable space comes into play is structural electronics. With this technology, the electronics become part of the structure. Potential applications include cars with printed organic light-emitting diodes inside and outside of the roof, as well as printed photovoltaics over the outside of the vehicle, acting as a supercapacitor skin, replacing the battery as energy storage.
Market analysts trying to explain the rise of printed electronics point to a number of economic factors. But if you step back and look at the emergence of wearables, smart interfaces and structural implementations, you realize that printed electronics have arrived at the right place, at the right time.
More Info:
Subscribe to our FREE magazine,
FREE email newsletters or both!Latest News
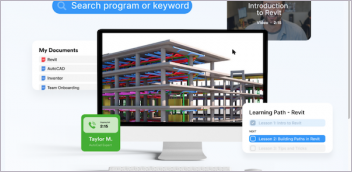

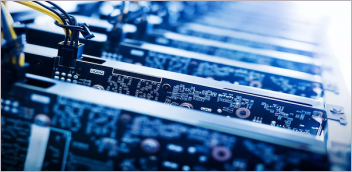
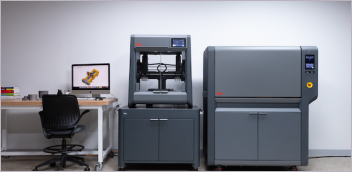