The Shift to 3D
While transitioning to 3D is gaining steam, 2D remains entrenched for a number of reasons.
Latest News
March 1, 2007
By Sara Ferris
The transition to 3D design software has been under way for the better part of a decade now, and the customer bases for SolidWorks and Inventor both now total half a million users or more. But vendors and market research firms alike believe that 3D has yet to make much of a dent in the 2D user base. Sandy Joung, PTC’s director of product marketing for Pro/Engineer and Mathcad, cites recent findings by the Aberdeen Group that 85% of the market remains working in 2D, but notes that PTC is seeing growing interest in 3D among small and mid-size businesses.
Image courtesy of Autodesk |
> > Integration of the dynamic simulation and stress analysis environments is enhanced in Inventor 2008 to offer more control over the loads to include in FEA simulations.
Bruce Boes, vice president of UGS’s Velocity Series, says that “well over half, maybe as much as three-quarters, of Solid Edge business is coming from people making that move from 2D.” SolidWorks reports that 70% of its new seats are sold to new customers, and roughly half of those are coming from a 2D environment.
Bruce Boes, UGS |
“There’s still a lot of folks out there using 2D that could benefit tremendously from 3D. They’re either afraid of it or don’t fully understand its benefits,” says Boes.
Reasons to Adopt 3DUsers of 3D CAD software cite many advantages over 2D. A 3D model provides much more detail, enabling designers to more clearly communicate product information and visualize complex parts and assemblies. 3D model data can be transferred to analysis and validation tools and used for CAM as well, increasing the accuracy of the results and saving time by eliminating the need to recreate data. Many features of 3D modeling programs increase productivity by automating aspects of the design process; for example, by enabling reuse of existing designs or allowing companies to generate families of parts.
Amy Bunszel, Autodesk |
The Aberdeen report, The Transition from 2D Drafting to 3D Modeling Benchmark Report: Improving Engineering Efficiency, surveyed 520 manufacturers and quantified the benefits of 3D. Best-in-class manufacturers typically require 1.4 fewer prototypes than average performers and six fewer change orders than laggard performers.
The main reason to move to 3D, though, is to keep up with the industry. “Companies are realizing their competition is getting to market faster,” says Amy Bunszel, director of the Autodesk Inventor product line. “Companies that want to be successful will have to adopt 3D.”
Image courtesy of Autodesk |
> > Enhancements to dynamic simulation in Inventor 2008 support analysis of the stress on parts at different points, or time steps, in the simulation cycle.
Aaron Kelly, SolidWorks director of product management, says many new customers approach SolidWorks because their competitors are already using the product. Boes goes so far as to say that those thinking about 3D are already falling behind. “The front edge is already moving to PLM,” Kelly says.
Greg Milliken, Alibre |
Greg Milliken, president of Alibre, believes that “it does hurt a business not to take advantage of 3D, if only to transfer data.”
Reasons to Keep 2D
An interesting finding in the Aberdeen report, corroborated by the various vendors, is that those who move to 3D don’t renounce 2D. Close to three-quarters of those who adopt 3D continue to use 2D software as well, says Chad Jackson, research director of product innovation and engineering at Aberdeen Group.
Chad Jackson, Aberdeen Group |
Part of the reason for that is the need to deal with legacy drawings that were done in 2D. There are also some tasks that are best performed in 2D: conceptual design, machine layout, diagrams, and schematics. Manufacturers in regulated fields such as medical devices may be required to produce and store 2D documentation for their products.
And as the market numbers indicate, it’s still a 2D world out there, so moving to 3D doesn’t remove the need to deliver 2D drawings to suppliers and machinists. Even though the maximum benefit from 3D occurs when companies optimize the use of model data for such tasks as analysis, simulation, and machining, many companies are content to revert to 2D when that’s what suppliers want. Though some companies do end up migrating to 3D to support OEM or customer demands, often the opposite is true.
Image courtesy of PTC |
< < PTC’s Pro/Engineer Mechanism Dynamics Option allows you to simulate real-world forces. This shock absorber assembly can be tested, in virtual space, for component clearance, interference, and performance throughout its complete range of motion.
Suppliers who stay with 2D, though, may be missing an opportunity. Those who adopt 3D can often get much better data from customers, in turn trimming the time they spend tweaking what customers send.
The Aberdeen Group found that the main reason companies stick with 2D software is that they can’t justify a switch to 3D. SolidWorks’ Kelly refers to this as inertia, or complacency: Companies are content with the way they’ve been doing things. Milliken agrees, noting that “the industry is resistant to change, even things that are obviously beneficial.”
Aaron Kelly, SolidWorks |
Some of the obstacles traditionally associated with adopting 3D are beginning to be less significant than they once were.
Cost is not so much of an obstacle with the advent of low-cost CAD applications like Alibre. From Milliken’s vantage point, price is an issue with many potential 3D users. Alibre’s approach is to offer a product with the most commonly used features and provide other benefits such as a lower price and easier accessibility.
SolidWorks’ Kelly notes that once companies identify the functionality they want, cost is not really an issue. One cost that companies sometimes don’t anticipate is new or upgraded hardware. Though vendors may claim that their software will run just fine on a 2D user’s existing hardware, the reality is that such programs require more horsepower than the typical 2D workstation, especially when you consider the complexity of today’s 3D assemblies. The Aberdeen report found that all of its best-in-class performers had invested in hardware upgrades as well as in 3D software.
Image courtesy of Autodesk |
> > This 3D model of a suspension loads analysis of an automotive a-frame and shock absorber was modeled with Autodesk Inventor.
Worries that 3D software is hard to use are disappearing. Not only are such products getting easier to use with each release, most vendors have developed tutorials and tools designed to cushion the change for 2D users.
Still, any change in software requires time spent on training and getting users up to speed. It’s virtually impossible to avoid some dip in user productivity. PTC’s Joung suggests that the issue is more complicated than simply learning a new program: “Learning how to design and conceptualize in 3D is a very different task,” she says, likening it to the difference between painting a picture and sculpting.
When adopting 3D design software, the key to success is establishing a goal. “What are your needs? Take the name tags off the solutions and find one that fits your needs,” says Jackson.
Kelly concurs: “They need to understand what they’re trying to accomplish. That’s going to dictate the solution they want.” He cited examples of goals such as reducing mistakes and using design analysis tools to cut the number of prototypes required.
Sandy Joung, PTC |
Though some vendors suggest that users can adopt 3D without changing their processes, companies are more likely to maximize the benefits of 3D by doing so. Jackson points out that the most successful companies in the Aberdeen survey took advantage of 3D’s extended and downstream capabilities such as model checking and design analysis.
Boes recommends that companies broaden their focus and also consider what they want to do after they adopt 3D: “Companies that are smart about this are looking two, three steps down the road.”
Kelly also recommends talking to resellers and to other customers, “customers who’ve used the product successfully.”
In planning their transitions, companies should anticipate the need to manage their 3D data. The ability of a 3D model to include much more information about the product is also one of its drawbacks: managing all the data associated with a 3D model becomes an issue.
Image courtesy of PTC |
> > With PTC’s Pro/Engineer Advanced Rendering Extension, marketing departments can create promotional materials that include stunning visuals showcasing all aspects of the product in its intended environment.
Companies should also plan in adequate transition time to get software installed and users trained. A frequently heard bit of advice was to make the transition at your own pace (though be careful not to drag the process out). Autodesk’s Bunszel suggests picking a representative design, either a new or existing product, and running a pilot program “to see where they need to change processes and workflows.”
Though 2D may be preferable for some tasks, it’s a rare company that won’t benefit from adding some 3D capability. The advantage of 3D becomes more apparent as product complexity increases and time to market diminishes. As Boes puts it, “The notion is to apply the right technology to the right thing at the right time.”
Sara Ferris is a freelance writer who’s covered the CAD industry since 1995. She was formerly editor-in-chief of Cadalyst magazine. Send your comments about this article through e-mail by clicking here. Please reference ” The Shift to 3D” in your message.
3D for All Stakeholders
Though still small compared with 2D, the 3D market supports a good number of software vendors. Alongside the Autodesks, PTCs, and SolidWorks are smaller vendors such as CoCreate, VX, IronCAD, and Alibre that have found a market niche to serve. One more product is poised to join the lineup at the end of March. Though SpaceClaim is a new company, it boasts a roster of mechanical CAD industry veterans, including CEO Mike Payne, formerly with Spatial Technologies, and Vice President of Product Development Daniel Dean, a cofounder of PTC.
The SpaceClaim mission is “putting 3D at the fingertips of everyone involved in mechanical design.” The key to this is SpaceClaim Professional, a nonparametric mechanical CAD application that uses an XML-based file format to facilitate data exchange with other MCAD applications and with PLM systems. In development for 18 months, SpaceClaim Professional extends 2D design concepts — sections, for example — to 3D to help current 2D users adopt it. The software is designed for Windows Vista, and its interface is modeled after Office 2007.
Image courtesy of SpaceClaim |
SpaceClaim estimates the total market for mechanical design software at about 5 million users. Of those, maybe 1 to 2 million engineers need the power of feature-based modeling systems, Payne says. Those in areas such as manufacturing, analysis, quality assurance, and conceptual design are the target market for SpaceClaim Professional. Feature-based systems are certainly powerful, Payne says, but they require lots of training and it can be difficult for those who didn’t build a model to change it. He views SpaceClaim as a complement to existing 3D systems. Conceptual engineers could use it to create quick models of design concepts, for example, then pass the data along to the 3D modelers.
Pricing for SpaceClaim Professional is $125 per seat per month based on a three-year license term. Data exchange add-ons and a TraceParts parts library will also be available. SpaceClaim will offer free view-only and student versions as well. The company plans to distribute the product through direct sales, a reseller channel, and its website.—SF
Alibre
Aberdeen Group
Autodesk
CoCreate
IronCAD
PTC
SolidWorks
SpaceClaim Corp.
UGS Corp.-Solid Edge
Subscribe to our FREE magazine,
FREE email newsletters or both!Latest News
About the Author

DE’s editors contribute news and new product announcements to Digital Engineering.
Press releases may be sent to them via [email protected].
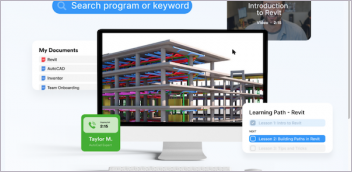

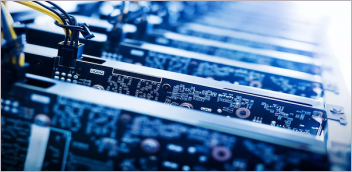
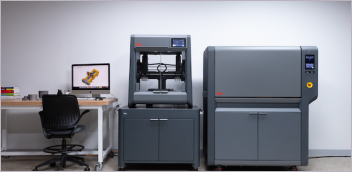