The Path to Production
GPU acceleration is fueling a new approach to additive manufacturing.

Image courtesy of Dyndrite.
Engineering Resource Center News
Engineering Resource Center Resources


Dell

Latest News
July 25, 2022
As adoption of additive manufacturing increases for both prototyping and production parts, new approaches will be needed to ensure part quality and reliability. 3D printer manufacturers, additive manufacturing software providers, and simulation software vendors have created a variety of tools to help improve print quality using a variety of approaches – simulating print processes, monitoring print progress/quality in real time, streamlining the CAD-to-print process, and adding customized AM interfaces to FEA solvers.
NVIDIA RTX™ GPU acceleration is also being leveraged to improve the performance of these tools. Solutions like Desktop Metal Live Sinter, ntopology, and Digimat from e-Xstream engineering (Hexagon Manufacturing) leverage the NVIDIA RTX GPU to better visualize workflows, simulate part deformation before a build, and calculate print time or material use, depending on the application. The NVIDIA RTX GPUs allow engineers to perform these tasks quickly and interactively.
Dyndrite has emerged as a key player on the CAM side when it comes to leveraging GPU acceleration to enable materials and process development as well as sophisticated toolpath generation. The company's Application Development Toolkit improves 3D printing toolpaths by importing CAD design files directly, and using advanced geometric analysis to drive the additive process. The fully native GPU kernel handles additive-specific computations and is naturally scalable with access to additional GPU nodes, both locally and in the cloud. The company developed the kernel using the NVIDIA® Quadro RTX™ 6000.
The Dyndrite technology is being licensed by other vendors to create GPU-accelerated tools as well. “Everything Dyndrite is doing is increasing the need for simulation,” says Harshil Goel, founder and CEO of Dyndrite. “We are expanding the number of ways you can create and assign sophisticated process parameters to different areas of parts, so much that the world will need more and more advanced simulation as we go forward due to the number of permutations of strategies possible.”
When it comes to GPU acceleration, however, Goel says the opportunities are much bigger than the standard rendering and simulation tasks most engineers are familiar with. The Dyndrite technology uses the NVIDIA RTX GPUs and the Dyndrite core geometry engine to analyze a geometry and cut it into different volumetric segments. “These volumetric segments are picking out important data about the part you are trying to print (an example might be a thin wall) and identifying where something special might need to happen,” Goel says. With this type of analysis, engineers can expand the envelope of printable materials, what types of parts they can print, the quality of the parts, and how fast the machine can print. (You can read more here.)
The Dyndrite software allows engineers to make complicated toolpaths with a GPU-accelerated approach to CAM that allows the assignment of multiple parameters across those volumetric segments. “That gives users power, freedom, and control over their manufacturing process, but can also lead to trillions of variations,” Goel says. “The only way to figure out the correct combination of those parameters is with the aid of GPU-accelerated simulation. We use the NVIDIA GPUs to make toolpaths, but the fact that we can make them so quickly, in such a sophisticated manner, puts pressure on the simulation solvers to speed up.”
(You can read more about the Dyndrite Toolpathing API in this blog, and dive deeper here.)
Additive manufacturing processes include a unique and complex set of parameters (depending on the specific additive process) that can affect print quality – material properties, gas flow, chemical dynamics, ambient temperature, material droplet volume.
“Every process requires compensations based on the hardware, the material, and the part being printed,” Goel says. “You need a way to analyze those parameters and apply corrections to create those toolpaths.”
What's more, the advancements being made in improving complex toolpath creation for 3D printing are also driving improvements for other manufacturing processes. This is important because, in many instances, additive manufacturing is combined with other processes to create a finished part. Controlling for multiple parameters across multiple production processes increases that complexity exponentially.
As the build envelope of the printers increases and designs become even more complex, the volume of data required to create a given part is rapidly growing. The only way to manage this explosion of data is by enlisting much more sophisticated software that uses the latest and greatest in compute and chip technology, Goel says. “At Dyndrite our goal is to use the NVIDIA RTX GPU not just for simulation and rendering, but for geometric analysis and compute. Any time anyone makes a decision about a manufacturing or design process, a GPU could be used to analyze what they are doing and help them make a more informed decision.”
Dyndrite has announced a number of partnerships over the past year that illustrate how the technology can be used to create better additive workflows, including the use of Dyndrite tools and technology by HP, DNA.am, Meteor Inkjet, Impossible Objects, and Azul 3D.
The company also has a developer council composed of all the leading AM brands, opining on the future of the company’s technology.
Ultimately, Goel thinks that NVIDIA RTX GPUs will play a key role on the manufacturing floor, and potentially within the 3D printing hardware. “You will need GPUs and high-powered compute in the machines or as close to the machines as possible,” he says. “That makes it possible to institute process monitoring and control locally and puts that large volume of data as close to end use as possible. Modern manufacturing machines are a great example of edge computing.”
Dyndrite is actively working with major simulation software vendors (including Ansys and Altair, both of which participate in the Dyndrite Developers Council) to create tools that will enable real-world, full-scale production applications for additive manufacturing. “The tools are NVIDIA RTX GPU-accelerated because we need to make very complicated things, and we are partnering with simulation vendors to connect all of our tools together so there is a closed loop,” Goel says. “The whole promise of additive is unlimited complexity, but you have to be able to tell the machine how to accomplish that. We are at a unique point in time where the manufacturing hardware has surpassed the software. Tools like Dyndrite bring compute and software to bear for the end user, so we reverse this trend and get to a production process as quickly as possible.”
More Dell Coverage
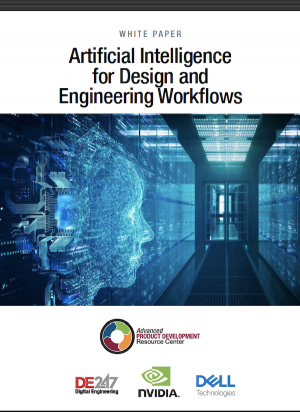
More Dyndrite Coverage
More NVIDIA Coverage
Subscribe to our FREE magazine,
FREE email newsletters or both!Latest News
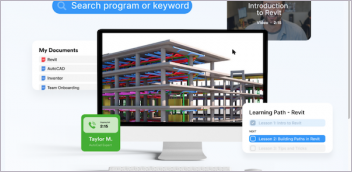

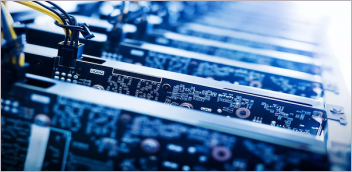
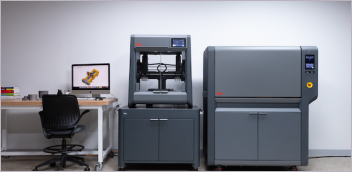