Latest News
February 1, 2017
Think for a minute about the trends that are shaping our world: the Internet of Things, additive manufacturing (AM) and the push for sustainability, just to name a few. It’s not an exaggeration to say that we’re undergoing the most fundamental changes in manufacturing since the introduction of the assembly line more than a century ago. According to The Boston Consulting Group, these technological changes will create around $15 trillion of value in the new economy.
That’s the good news. The downside of this revolution is the incredible levels of product complexity that these changes will require. Just take the example of a pump. A decade ago, this would be a simple metal, mechanical device. Now it includes onboard electronics and wireless communications. It has multiple composite materials and it is being deployed in environments as varied as a mountaintop in Alaska to the sweltering sand dunes of Saudi Arabia. Designing equipment for such conditions could challenge even the most experienced engineer.
Because of continuous enhancements, simulation solutions can meet these challenges. Engineers can now simulate more complex physical phenomena than ever before using structural, thermal, electromagnetic, fluidic and controls simulation, either in isolation or in coupled multiphysics studies. Computing power and usability have improved so much that companies large and small, established and startup, are using engineering simulation today. Design engineers can test thousands of versions of a product in a matter of minutes or hours, depending on the available computing resources.
The ability to virtually test so many versions of a product has been the classical application of engineering simulation, typically referred to as digital prototyping. It has replaced the old and cumbersome build-and-test method of product innovation. Now, driven by market and technological pressures, engineering simulation is being used earlier in the design cycle—the digital exploration phase—and is also reaching beyond product development into the operations realm in the form of digital twins.
A New Digital Stage
In the digital exploration stage, engineers use simulation to fully explore all the possible parameters of a new product—temperatures, pressures, voltages, resistances, flows, strength, material properties and more—to identify unique combinations that may never have been considered, while simultaneously eliminating obvious outlying designs. Performing digital exploration upfront in the design process reduces the number of variations that need to be tested in the digital prototyping phase.
In an exciting and relatively new extension of the technology, digital twins offer the most potential for growth by inserting engineering simulation into the operations end of industry. A digital twin is a virtual copy of an actual operating machine rendered as an engineering simulation model. Sensors on the machine relay data—temperature, vibration, impact and loading—to the digital twin, and the twin evolves in step with the machine. The constant feedback can be beneficial in two ways: It can help engineers to optimize the operation of a machine or a system, and it can predict adverse conditions long before they happen.
Take a wind farm generating electricity as an example. Depending on the wind speed and direction, it may make sense to tilt the turbine blades to maximize wind capture and electricity generation. Because of the interaction between neighboring wind turbines, shutting down some of the turbines may optimize the output in certain wind conditions. Digital twins of each turbine in the wind farm can make such decisions easy. Also, engineers might notice deteriorating performance of a certain turbine blade in the wind farm, and can replace it during a scheduled downtime, rather than making an untimely shutdown. The collected data from digital twins could also be used to improve the design of the next version of the wind turbine. The cost savings from optimal performance, improved maintenance and enhanced future designs could be immense.
Combining the physical and the digital worlds brings enormous opportunities and challenges. Expanding simulation from its traditional role as a validation tool and bringing it to new engineering audiences throughout the product lifecycle will spur innovation, lower development and operational costs, and improve time to market. At ANSYS, we are incredibly confident about the opportunities ahead, and are excited to be a part of this latest technological revolution.
Ajei Gopal is CEO of ANSYS. Send email about this commentary to [email protected].
Subscribe to our FREE magazine,
FREE email newsletters or both!Latest News
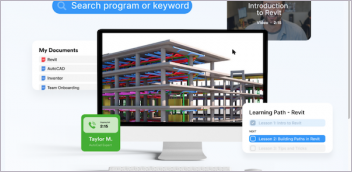

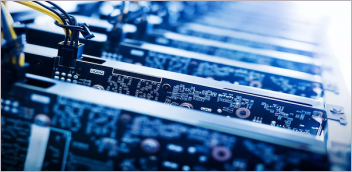
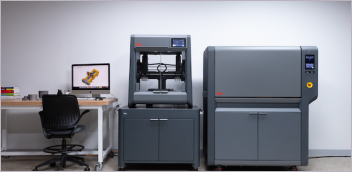