Latest News
August 1, 2013
By Josh Fredberg

With these smarts, however, comes complexity. Products are increasingly becoming an intricate and intermingled combination of software, electronics and hardware, yet they must be delivered to market with quality at a record pace. Extremely complex to design and build, smart devices incorporate thousands of parts that have to work together—putting systems-level engineering front and center.
The engineering challenge remains to ensure these products will operate as expected in the real world, despite their increasingly smaller size and number of multiple physics components. Products that take the market by storm—like the newest tablet or hybrid automobile—go hand in hand with leading-edge development processes that can quickly transform conceptual ideas into scalable, reliable and cost-effective products.
Integrating Analysis into the Design Process
We believe that immersing simulation into the design strategy can stimulate innovation; we call this Simulation Driven Product Development (SDPD). At the foundation of SDPD is the concept of virtual prototyping, in which real-world product performance is predicted and studied with simulation models instead of expensive, time-consuming hardware prototypes. However, gaining an edge in a competitive environment takes more than simply using simulation software—it requires the ability to rapidly test hundreds, even thousands, of designs in a short amount of time, and technology that is integrated into an entire product development process.
The reality remains that many companies perform simulation as a function separate from design, with engineers throwing projects over the wall to an analysis group. Often, this occurs in the final phases of product development, when changes require considerable time and money to perform. Moving simulation earlier in the conceptual stages of product development can shorten time to market and lower product development costs. In this way, SDPD elevates the role of analysis from a standalone troubleshooting tool to that of an integrated design approach for quickly creating and refining innovative designs.
Implementing SDPD
The pervasiveness of smart products and their complexities, combined with the need to do more with less, is a sign that it’s no longer business as usual—that the way simulation is deployed in organizations needs to change. To keep up with increasing market demand for these products, simplified simulation in a single-user environment allows non-expert users to leverage the technology, helping to decrease time to market.
Engineering simulation technology and its associated processes are critical to facilitating upfront simulation, efficient evaluation of alternative designs, iterative modification of designs based on simulation, and collaboration among different groups. Through the ability to quickly perform what-if studies and evaluate alternative configurations, simulation provides insight into product behavior and gives free reign to the imagination of product team members. In such an approach, simulation guides the direction of the design to optimally satisfy such requirements as performance, reliability, sustainability and cost. Hundreds of concept alternatives can be evaluated with simulation before detailed design is begun.
One of the greatest values of simulation-driven design for manufacturing companies is facilitating experimentation—and in turn, innovation. Senior executives know that innovation in product development as well as manufacturing processes is key to a company’s long-term potential in the market. In this respect, engineering simulation has been elevated from that of an obscure technology understood only by dedicated analysts to a critical component of a company’s corporate market strategy. The bottom line can be significant time reductions, cost savings, quality improvement and product design innovation.
That said, these and other necessary organizational changes require a significant investment in time and effort. This level of commitment defines how companies individually leverage simulation, and determines which firms will most likely lag behind while others reap the greatest business value from SDPD.
Josh Fredberg is vice president of marketing for ANSYS. Before joining the firm in 2009, he was senior vice president of product and market strategy at Parametric Technology Corp. (PTC), and has held leadership roles with both ARIBA and Andersen Consulting Strategic Services. Send e-mail about this article to [email protected].
Subscribe to our FREE magazine,
FREE email newsletters or both!Latest News
About the Author

DE’s editors contribute news and new product announcements to Digital Engineering.
Press releases may be sent to them via [email protected].
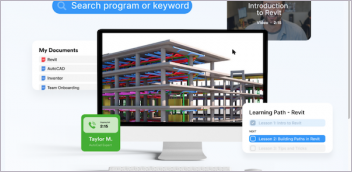

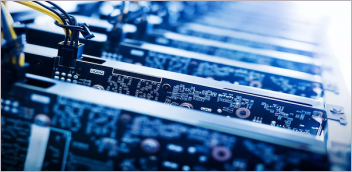
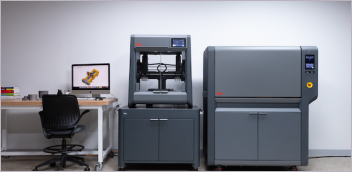