Supersonic Comeback
Engineering startups and government agencies revisit the possibility of supersonic flight.

Boom’s XB-1 is being built to validate technologies for Boom’s airliner. The data collected from XB-1 test flights will help the company refine its design and engineering, test key supersonic technologies and ensure efficiency, safety and reliability, according to the company. Image courtesy of Boom.
Latest News
December 1, 2018
Commercial air travel is poised to get a lot faster thanks to the efforts of a handful of new supersonic jet companies, new technology and potential regulatory changes that could enable overland supersonic flight.
It’s been more than 15 years since the Concorde ceased operation after a deadly crash and its financial viability became unsustainable. Supersonic jets are expensive to operate, consume a lot of fuel, create a lot of emissions and present a number of design challenges. But activity around high-speed flight is increasing.
In fact, some companies are looking past supersonic to even faster planes. Boeing unveiled its concept for a hypersonic passenger plane (which could fly at speeds above Mach 5) at the American Institute of Aeronautics and Astronautics conference this year. Although it could be decades before hypersonic passenger planes take to the skies, the company is investigating a number of different commercial and military applications.
The U.S. Air Force is also developing a hypersonic flight research vehicle, and Aerojet Rocketdyne has tested a dual-mode ramjet/scramjet engine that could support hypersonic aircraft as part of its work with NASA, the Air Force and Defense Advanced Research Projects Agency (DARPA).
The Chinese Academy of Sciences has also reported testing a scaled-down hypersonic jet in a wind tunnel that reached a top speed of 5,343 mph.
“The potential for hypersonic aircraft becoming a reality will require further advances in several technology areas as well as market demand,” says Boeing Spokesperson Brianna Jackson. “There are also infrastructure considerations both for operation at airports and maintenance.”
Supersonic Flight Testing
In the near term, commercial supersonic flights are closer to being a reality. A handful of companies are betting on demand for commercial supersonic aircraft (particularly business jets). Boom, Aerion and Spike Aerospace all have aircraft currently in various stages of design. Their biggest challenge will be ensuring a sustainable business model. Spike expects the market to be as big as 13 million passengers annually.
There are also regulatory hurdles. In the U.S., the Federal Aviation Administration (FAA) banned supersonic flight in the continental U.S. because of the noise these planes generate. However, most of the supersonic start-ups claim their designs can meet current noise standards for both sub- and supersonic flight, and can potentially meet more stringent future requirements.
This is a preliminary design for a passenger-carrying hypersonic vehicle concept that could have commercial and military applications. It is just one of several hypersonic vehicle concepts spanning a wide range of potential applications being studied by Boeing. Image courtesy of Boeing.
In April, NASA signed a $247.5 million contract with Lockheed Martin to develop a quiet supersonic plane (the X-59 QueSST) as a low-boom flight demonstrator to test out its new design concepts. In November, NASA was scheduled to conduct a test using a modified F/A-18 Hornet combat jet to see if it could reduce the sonic boom to a “sonic thump.”
In October, the U.S. Senate added language to the FAA reauthorization bill that could help facilitate supersonic flights, calling on the agency to set certification standards to enable civilian supersonic flights in U.S. airspace and to consider repealing its 1973 ban. The Senate had considered a straight repeal of the ban, but removed that language at the request of environmental and public health groups concerned about noise and emissions.
“That means, supersonic aircraft today must be efficient and comply with the latest strict takeoff and landing noise requirements, as well as current emissions standards,” says Jeff Miller, vice president of marketing and communications at Aerion Supersonic. “An extremely efficient aerodynamic airframe is absolutely essential, and Aerion has accomplished this with unique design tools and a team of some of the world’s best aerodynamicists.”
Aerion is currently working with GE Aviation, Lockheed Martin and Honeywell to develop its AS2 supersonic business jet.
Optimizing Economics and Noise
The physics challenges of supersonic flight are well known, says Eli Dourado, global policy director at Boom. “But while the world has known how to build supersonic aircraft for decades, the technology to make them economical is more recent,” he says. “Boom isn’t reinventing the wheel—we’re using only existing technology that’s already flying on other aircraft. Instead, we’re solving an optimization problem.”
A full-scale engineering mockup was created by Aerion to advance the cockpit and cabin design of the AS2. Image courtesy of Aerion.
A shortage of suitable powerplants has also presented a challenge, particularly with tightening noise emissions. GE and Aerion announced the new GE Affinity turbofan engine earlier this year, which the companies say is the first new civil supersonic jet engine released in 55 years. According to Aerion, it meets Stage 5 takeoff and landing noise rules and current emission standards. Aerion expects to finish its preliminary design phase in 2020, and the company claims to be on track to fly by 2023.
“Quieting a supersonic engine to meet subsonic regulations is an enormous challenge, and can drive engine fan size (and drag) in the opposite direction required for efficient supersonic flight and long range,” Miller says. “Aerion and GE Aviation have been studying this challenge for about five years, and were quite proud to announce the Affinity engine. Our challenge was to design the AS2 business jet to fly very efficiently at both supersonic and subsonic speeds.”
Future hypersonic aircraft present other types of problems. “The highly integrated nature of air-breathing hypersonic vehicles make them very difficult to properly design, and extreme heating from air friction requires hypersonic vehicles be made of very high-temperature materials and structures that are both light and durable,” says Boeing’s Jackson. “Integrating the engines and airframe in a manner that achieves high performance across a very large operating envelope adds to the design challenge.”
43% of DE 2018 survey respondents ranked regulatory challenges as an extremely/very important challenge in their day-to-day work.
Technology Gives Supersonic Flight a Lift
Advancements in engine performance, materials and design technology are also making it easier for smaller startups like Spike, Aerion and Boom to make a serious play in aerospace industry.
Carbon composites are certified for flight on commercial airliners, for example, and turbofan engines are becoming more quiet and efficient.
“We also have access to significantly more computing power than designers even a decade ago—parallel computing enables us to run more simulations in less time, optimizing our design to maximize aerodynamic efficiency and minimize unnecessary structure,” says Boom’s Dourado. “With today’s technology, we’re able to build a supersonic airliner that makes financial sense at today’s business-class ticket prices.”
GE and Aerion announced the new GE Affinity turbofan engine earlier this year, which the companies say is the first new civil supersonic jet engine released in 55 years. Image courtesy of Aerion.
Boom is using cloud computing and simulation for its designs, reducing the need for engineering staff and wind tunnel testing. The company turned to the cloud because the necessary high-performance computing (HPC) infrastructure would have been cost prohibitive to deploy on site. The company is running all of its simulations on Rescale’s compute platform, and uses Rescale’s ScaleX Enterprise administration portal to help coordinate budgets, teams and security.
Boom runs Navier-Stokes unstructured computational fluid dynamics (CFD) simulations of the flight envelope using customized HPC clusters on the cloud and accessing as many as 512 cores (with capacity to expand beyond that). Using simulation in this way has helped accelerate design development, as engineers can evaluate 100 configurations at once and achieve a 6x speedup for each job. They can also scale up and down without a huge investment in IT overhead.
“Boom’s computational fluid dynamics software is the workhorse of our design process,” Dourado says. “Instead of building and testing costly wind tunnel models each time we make a tweak to the loft, we rely on CFD simulation. To be sure, we still return to the wind tunnel from time to time, but the primary purpose of these physical tests is to validate the fidelity of our CFD results.”
Boston-based Spike Aerospace has partnered with MAYA Simulation and Siemens PLM Software to use CAE and simulation to reduce the sonic boom generated by its plane via optimized aerodynamics. Simulation has made it possible for the small company to design the plane without a prohibitive investment in physical prototypes and testing. The company plans to fly a supersonic business jet (the 18-passenger S-512) by 2021, with commercial availability in 2023.
According to Aerion, propulsion advances will drive new development as well. “The AS2 airframe will be built of carbon fiber composite materials,” Miller says. “These materials and construction techniques are now well understood and in common use within the industry. The same applies to fly-by-wire technology, although Aerion will employ the most advanced fly-by-wire systems (previously only in military aircraft and the latest business jets), including active-control side sticks, which provide tactile and visual feedback to pilots.”
Adding Materials to the Equation
Materials will also be critical for future hypersonic jets, which generate enormous amounts of heat. Researchers at NASA and Binghamton University have tested boron nitride nanotubes for this application, because their heat resistance could enable travel at five to 10 times the speed of sound.
A rendering of the Spike S-512 supersonic business jet. Image courtesy of Spike Aerospace.
Aerion relies heavily on simulation and modeling for transonic and supersonic airflows, which Miller says has allowed for rapid design iterations and airframe shape optimization. The company uses tools developed through its Palo Alto, CA, subsidiary, Aerion Technologies Corp.
“The insight from these tools allows us to make rapid decisions that would traditionally require much more expensive testing and detailed design work,” says Alex Egeler, vice president of software for Aerion Technologies. “Using an internally developed framework, the AS2 design team has run millions of automated designs and analyses between the cloud and on-premises hardware for the aerodynamic shape of the aircraft.”
The company has developed a modular, object-oriented configuration design software tool to perform trade studies and improve the AS2 performance based on the program updates and insight from working in collaboration with GE Aviation and Lockheed Martin, according to Egeler. The software can optimize the design of the aircraft and fly a simulated mission to determine key performance metrics.
Honeywell is also researching the potential for “boom mapping” software that can help pilots know when atmospheric conditions could allow the boom to get too close to the ground. Aerion has dubbed this technology “Boomless Cruise,” and it can potentially measure the Mach cutoff speed (usually between Mach 1.1 and 1.2) even in variable atmospheric conditions.
“Flight at Mach 1.2 over the U.S. would be about 50% faster than today’s airliners,” Miller says. “This would be a breakthrough for flight over land.”
New high-temperature composites and other materials are making it easier to create faster aircraft. Boeing, Airbus and Embraer have all manufactured airliners at least partially made from carbon fiber, and the material has many advantages over aircraft-grade aluminum when designing a supersonic aircraft, according to Boom’s Dourado.
“Carbon composites are much more thermally stable than aluminum—the Concorde’s metal fuselage would grow by about a foot when experiencing the high temperatures of Mach-2 flight,” Dourado says. “But in 2018, we’re able to design a lighter airframe out of carbon composites that won’t expand or contract to the same degree.”
He adds that supersonic airplanes benefit from careful aircraft shaping that minimizes drag and improves fuel efficiency. “While it’s easy to fabricate cylindrical tubes out of aluminum, it’s much harder to manufacture the kind of curved, area-ruled forms that reduce wave drag at supersonic speeds,” Dourado says. “Carbon composites, on the other hand, are easier to fabricate in the shapes we need.”
According to Boeing, key innovations that could enable hypersonic flight include lighter and more durable high-temperature materials, increased hypersonic engine performance and size, advanced sensing and analysis technologies for system health monitoring and intervention, and active control of hypersonic engine performance and stability.
Regulatory Changes May be On the Way
While supersonic aircraft designers have reduced aircraft noise, the rules limiting that noise are getting more stringent.
In 2020, new airport noise limits take effect (as part of regulations known as Stage 5 in the U.S. and Chapter 14 globally). Supersonic aircraft currently in development have to comply with those new rules. Aerion already replaced the original Pratt & Whitney engine for its aircraft with the GE engine because of the upcoming regulations. The AS2 is designed to fly at Mach 1.4 over water, but could potentially reach Mach 1.2 over land without its sonic boom reaching the ground.
The rules limiting supersonic travel helped sink the Concorde, but the companies Digital Engineering spoke to say they can succeed by designing their aircraft to meet existing standards and by limiting supersonic flight to certain geographies or over water.
Nearly a third of DE 2018 survey respondents are currently developing products using advanced materials. Of those who are not, 20% say they expect to be developing products using advanced materials within the next two years.
“In some cases, rules for supersonic airplanes that cruise at altitudes up to 60,000 feet simply don’t exist, and we will work with regulators to come up with solutions that allow progress without compromising safety,” says Boom’s Dourado. “In light of widespread prohibitions on overland supersonic flight due to the issue of sonic boom, we baseline a subsonic cruise speed over land and a Mach-2.2 supersonic cruise only over water. Even with this constraint, there is a market for nearly 2,000 of our airliners, and hundreds of routes worldwide have enough premium-cabin demand that the aircraft makes economic sense.”
“The AS2 requires no regulatory changes to enter service, as it will comply with the latest noise and emissions standards,” says Aerion Supersonic’s Miller. However, he adds that potential changes at the FAA under the new reauthorization bill could lead to development of even faster jets and more over-land flights.
Hypersonic jets will have to clear additional hurdles. Civil hypersonic flight is likely decades away and flight at speeds above Mach 5 is still extremely inefficient. Costs of operating both supersonic and hypersonic planes will be high.
However, the stars seem to be aligning for commercial supersonic flights in the near term. With the work of NASA and others in reducing the effect of sonic booms, new materials and efforts on the part of companies like Spike, Boom and Aerion to improve the efficiency of these planes (and in some cases to meet existing noise standards), the start of commercial flights, at least over water, is probably just a few years away. Most of the companies featured in this article are aiming to put planes in the air between 2021 and 2022.
Subscribe to our FREE magazine,
FREE email newsletters or both!Latest News
About the Author

Brian Albright is the editorial director of Digital Engineering. Contact him at [email protected].
Follow DE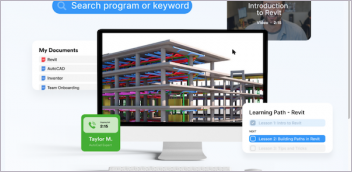

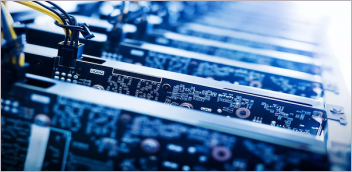
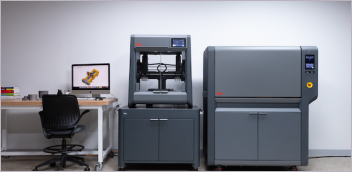