Student Develops New Additive Manufacturing Process

Robotic arm at work building an object via the new suspended deposition process. Courtesy of NSTRMNT
Latest News
July 24, 2013
With coffers burgeoning from sales, one might think that the largest additive manufacturing (AM) companies might be responsible for new developments in 3D printing, but it’s consistently institutes of higher learning that lead the way. Metal seems to be a commonly favored area of development, but not everything needs to be made from titanium or steel.
Brian Harms, a design research Masters Student at the Southern California Institute of Architecture (SCI-Arc) has advanced a new AM process he calls suspended deposition. In its current state, suspended deposition employs a robotic arm and liquid resin to build 3D objects in a tank of gel.
The gel acts as a support material for builds, allowing objects to be built with a light-curing resin material. Working in this manner allows for builds to proceed in three dimensions, rather than ending in a 3D object. Different parts of an object can be built up before returning to the base and working on a separate area, and alterations in the design can be achieved by adding to “finished” portions of the object during the same build.
One major distinction between this project and other rapid prototyping processes is the ability to utilize 3D vector-based toolpaths. Virtually all other processes use paths generated via contouring a digital model, and rely on the hardening of each successive layer before being able to move on to the next. –Brian Harms
In addition to building in three dimensions, the nature of the light-curing resin suspended in gel allows for subtractive methods. This amounts almost to an undo feature. If an area of a build needs to be altered or reconstructed due to an error, the resin can basically be scooped out before it hardens and replaced with a new shape.
Using a robotic arm to for AM isn’t the most cost-effective method of printing objects, but it probably wouldn’t require much effort to adapt Harm’s suspended deposition process to more standard forms of 3D printing. The power to save a build with one or more errors by simply undoing the problem areas might be nearly worth its weight in gold just to save on material waste.
Below you’ll find a video of the process.
Source: NSTRMNT
Subscribe to our FREE magazine,
FREE email newsletters or both!Latest News
About the Author
John NewmanJohn Newman is a Digital Engineering contributor who focuses on 3D printing. Contact him via [email protected] and read his posts on Rapid Ready Technology.
Follow DE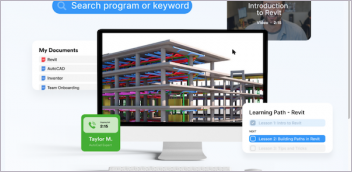

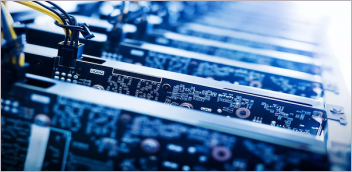
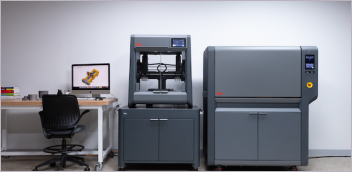