
The University of Wales team ready to test 3D printed improvements to four kitesufing boards. Courtesy of Stratasys.
Latest News
October 21, 2014
The 3D printing era has brought with it the dawn of design freedom. In place of rigid designs based on traditional manufacturing methods, additive manufacturing (AM) gives designers a method of generating digital designs that can be brought to life and perfected through rapid prototyping. It’s easier to take risks when the development cycle is written in days, rather than months.
The University of Wales is in the midst of offering a demonstration of the potential of the new design paradigm by building a kitesurfing board manufactured with a Stratasys AM system. The board uses high tech materials to increase durability while reducing overall weight. The project is part of a contest to see if a kitesurfing board can cross the Bristol Channel more quickly than an automobile can navigate around the watery barrier.
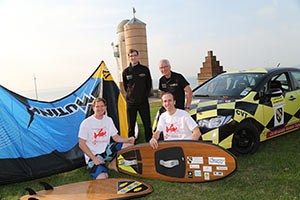
“The use of 3D printing in product design, and especially in the extreme sports market, is revolutionizing the manufacturing process and the speed to which companies can bring new products to market. We wanted our students to witness this first hand,” said Ross Head, product design manager for Cerebra at the University of Wales TSD Swansea, and one of the challenge kite surfers.
New parts for the board were built on a Stratasys Fortus AM system, and reinforced with carbon fiber. 3D printed parts include board fins, which were redesigned specifically for the water and wind conditions the team expects to encounter in the Bristol Channel. The team also printed bespoke inserts for the foot straps to ensure maximum strength.
The university produced a total of four boards, and was able to move quickly from idea to prototype, thanks to AM.
“Stratasys 3D printing was essential to our ability to undertake this project at all. We would literally design, 3D print, fit and test the parts on the boards – all in one day. We would then tweak the designs as necessary and have another set of parts 3D printed overnight,” added Head. “The fact that we could 3D print end-use parts that could perform in the harsh sea environment, quicker and cheaper than any other manufacturing process, takes product development to a new and higher level for us.”
As indicated by Head, this isn’t the first time 3D printing has been used to improve equipment for extreme sports. Other efforts include a surfboard, a snowboard, and parts for cycling enthusiasts. Below you’ll find a video about the kitesurfing board.
Source: Stratasys
Subscribe to our FREE magazine,
FREE email newsletters or both!Latest News
About the Author
John NewmanJohn Newman is a Digital Engineering contributor who focuses on 3D printing. Contact him via [email protected] and read his posts on Rapid Ready Technology.
Follow DE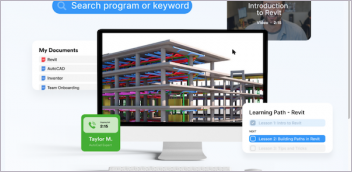

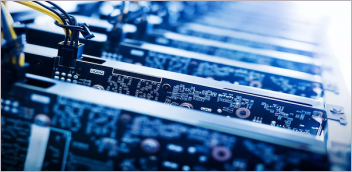
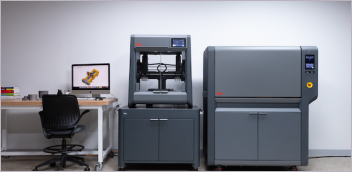