Solving for Trust: Restraints of AM Materials Simulation
Limited test data on materials performance for metals AM printers is slowing confidence in still-fledgling technology.

ANSYS’ Granta acquisition delivers tools dedicated to materials data management and selection, including the MI:Mat Analyzer app for visualizing test data. Image courtesy of ANSYS.
3D Printing Simulation News
3D Printing Simulation Resources


Dassault Systemes

Latest News
October 1, 2019
Advances in additive manufacturing (AM), particularly in metals, have shown huge promise as of late, ushering in capabilities that improve part precision, performance, form factors and prices to make the technology a competitive alternative to traditional production methods. Yet a lingering cloud on the AM metals horizon is the issue of trust, as engineers question whether the still-fledgling technology can consistently produce reliable parts on par with conventional practices like casting, forging and injection molding.
Simulation—of AM processes and, more importantly, of material performance—holds the key to resolving the trust issue. Simulating AM materials and processes allows engineers to virtually test drive how parts will hold up during and after the build process, helping to optimize designs for manufacturability while avoiding costly design miscues.
Although simulation is critical to building trust and accelerating the adoption of metals AM, engendering trust in the simulation models is another big hurdle. Inconsistencies between AM builds and simulation models have some early adopters worried that these shortcomings will impede their ability to optimize designs while dampening their enthusiasm for large-scale adoption of the still-nascent technology.
Part of the problem lies with the number of highly complex variables that must be fully vetted, including the impact of extreme heat and cooling that the metals AM process has on the thermal properties of materials. At the same time, there is still limited test data available to adequately validate simulation models across all possible permutations, and the available test data is considered a competitive advantage—a scenario that discourages sharing as well as open source innovation.
The result is a classic chicken-and-egg conundrum: Engineering organizations are reticent to adopt new metal AM technology without proper validation of part performance, but their reluctance to get on board is hampering the process of collecting, testing and validating data for effective AM materials simulation.
“Ideally, you could go straight from putting powder metals or polymers into a machine and get the results you want, but unfortunately, there are no shortcuts,” notes Dr. Rashid Miraj, director of technical operations for AlphaSTAR, the maker of Genoa 3DP, an additive manufacturing software suite.
“The reality is if you want to have a good simulation model, you have to start with real test data,” Miraj adds. “People have a tendency to think you can buy the [simulation] software, and bingo, you’re ready to go, but the challenge is bigger. Everyone needs to make a commitment to do some level of testing.”
Macro versus Micro
Access to reliable materials databases is critical for fueling AM process simulations and for ramping up test and validation initiatives. To fill the void, simulation provider ANSYS in January acquired Granta Design, a leading provider of materials data and materials information management software.
In addition to Granta’s rich materials library, the acquisition expands the ANSYS simulation portfolio with GRANTA MI, a system for enterprise materials information management; MI:Mat Analyzer, an app for visualizing test data; and CES Selector, which lets users explore the impact of materials on the behavior of their products.
“Ideally, you could go straight from putting powder metals or polymers into a machine and get the results you want, but unfortunately, there are no shortcuts.”
“Garbage in is garbage out, and that’s particularly true in the case of materials simulation in that you need to understand the properties of the powder you’re putting in the machine, you need the materials data and you need to understand what the appropriate materials assumptions are to give to the simulation so you can predict outcomes,” explains Brent Stucker, director of additive manufacturing for ANSYS.
Another complicating factor is the metals AM process itself, which creates huge thermal swings as material is heated, melted and cooled in a near instantaneous fashion. This process can produce voids, air pockets and deformations that are hard to correlate with the behavior resulting from traditional methods such as casting and forging, and next to impossible to predict without confidence in test data.
“You need to understand how the material is acting at all these different temperatures—these properties don’t exist anywhere in a handbook and there’s very little data,” Stucker says. “It’s a conundrum—we need a lot of data, but most companies don’t know what data they need.” For its part, ANSYS is conducting hundreds of design of experiments (DoE) to explore material behavior using various laser parameters and metal powders as a way to enhance and validate test data.
Like ANSYS, some of the larger aerospace companies, which are pioneering the use of metals 3D printing, are trying to build out materials test databases of their own. The exercise is a significant investment and considered a proprietary edge. As a result, companies are reticent to share this treasure trove of data, which in turn is hampering progress on the materials simulation and testing front.
“There aren’t many databases, and companies tend to keep them secret so they can’t compare information and gain confidence,” says Aaron Frankel, vice president, additive manufacturing software program for Siemens Digital Industries Software. “If you look at Airbus and Boeing, they are building similar components with the same materials—if they were open to sharing materials test data they could be more confident, especially if they were seeing the same results.”
“Will we evolve to a world where no test parts are needed? The answer is no; simulation is math and we always need to check what we are doing.”
Simulation software providers like Siemens Digital Industries Software and Dassault Systèmes are partnering with leading providers of materials databases as well as collaborating with customers and research labs to integrate materials intelligence into their AM simulation suites and to ensure materials test data is validated. Dassault Systèmes’ BIOVIA brand, which creates custom materials for companies, will also certify those new materials down to a molecular level to aid in test and validation.
Through its Simufact partnership, Materialise has integrated AM simulation into its Magics 3D Print suite. The Simulation Module, tailored specifically to the metals AM process, helps predict distortions and residual stresses on virtual 3D part models, helping to ensure material has the right microstructure and properties for quality control and to reduce the number of build failures.
As important as materials simulation is to metals AM adoption, organizations still need to prepare for physical test runs of 3D prints as part of an evolving validation and test process. “The more we can simulate, the fewer test parts we have to make,” notes Tim Van den Bogaert, software director for Materialise’s 3D print factory. “Will we evolve to a world where no test parts are needed? The answer is no; simulation is math and we always need to check what we are doing.”
Altair also has a partnership, with Amphyon, for software to help predict material behavior. However, predicting part behavior under operational loading after the 3D printing build process and subsequent heat treatment remains tricky, according to Ravi Kunju, senior vice president of simulation-driven design tools at Altair.
“Using the technologies we have today, it is possible to take the macro properties (residual stress) and map them to predict performance behavior more accurately than using nominal material properties of the base material everywhere,” Kunju says.
As it exists today, the process is calibrated for traditional methods like sheet metal forming and casting, but Kunju says it’s far trickier to extend it to metals AM. “For parts made from the selective laser melting 3D printing process, for example, it is challenging to accurately predict microscopic characteristics like gas entrapment and grain structure, which can lead to failures that are likely to occur due to fatigue,” he explains.
Additionally, the rapid pace of developments in the various AM technologies, coupled with the inability of organizations to select and focus on any one method, has resulted in a lack of standards for material characteristics, print process and part certification for the entire supply chain.
“Virtually capturing the physics during the build at the micro, meso or macro level is possible separately, but not all at the same time so as to get results in a reasonable fashion,” Kunju says. The build process has lot of variables that can severely affect the final properties like laser speed, hatch distance and laser path scan direction. In many cases, it is difficult to even assume that a few nested and identical physical parts will be identical on a single build plate, he adds.
“There are lots of assumptions to be made to predict exact material behavior at the macro level for which familiarity of the process and consensus on what are allowable levels of variation is essential,” Kunju says. “Ideally, technology can solve any complex problem; however, in this case, unless the industry as a community comes together and defines standards of acceptance based on criticality of the final part being manufactured, it will be hard to engineer a solution that is acceptable for all.”
As the standards and materials test processes continue to evolve, organizations should stay mindful of the current limitations of materials simulation to determine if metals AM production methods are suitable for their particular use case. The use of metals AM technology to produce parts for landing gear may be premature without fully validated materials test data due to safety concerns and federal regulations. However, the same rigor is not required for the production of a bracket that holds a mirror on a car, for example, making it a better candidate for the technology at this juncture.
Although vendors do their part to ramp up the materials test process, customers need to do their own due diligence performing physical tests of builds using different materials and printer parameters. Through this trial-and-error process of design of experiments, printing test coupons and weighted sensitivity studies, they can determine which parameters have the greatest effect on anomalies and start to build up a repository of test data to fuel simulation efforts.
“Some days I think we’ve made a lot of progress and other days I think we have a lot of progress to make,” says Rani Richardson, Dassault Systèmes’ director of lightweight engineering for CATIA technical sales. “Until we get parts into flight or in cars driving, there’s still a lot of work to do.”
More Ansys Coverage
More Dassault Systemes Coverage
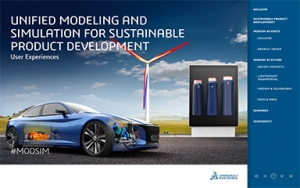
More Siemens Digital Industries Software Coverage
Subscribe to our FREE magazine,
FREE email newsletters or both!Latest News
About the Author

Beth Stackpole is a contributing editor to Digital Engineering. Send e-mail about this article to [email protected].
Follow DE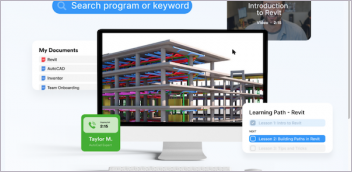

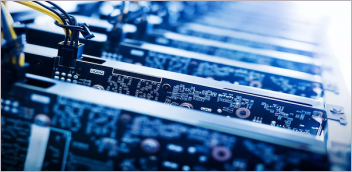
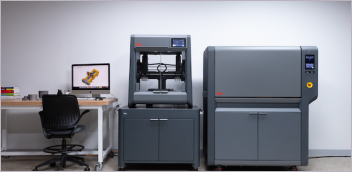