Latest News
December 1, 2009
By Steve Robbins
![]() |
Recently I attended COMSOL’s user conference. Though it was one of many user events I’ve attended over the years, this year’s was different from all the others. The company announced the release of COMSOL Multiphysics 4.0, and while simulation has increasingly become faster, this package makes it easier.
During a demonstration in which the software design team was running the program through its paces, engineers in the ballroom kept interrupting the speaker with suggestions on what variables to use, how to define geometry, how to set boundary conditions, and move around the interface. Talk about intuitive!
What really stayed with me from this experience was how fast and easy to use multiphysics has become. This ease of use gives speed and power to the engineer. It helps to move simulations to the very front of engineering design. Simulation software of all stripes is not only faster, but the ease of use in all steps of the modeling process gives the designer the ability to change variables in minutes, solve FEA and CFD analysis quickly, and use visualization tools to check the results.
Simulation-based modeling is saving time and materials, and resulting in better products. Changes at the manufacturing stage are reduced. Products get to market quicker. It is interesting to note that the same cycle changes are occurring on the other side of the design process as well. Product inspection is actually beginning to occur well before the manufacturing team takes over.
It used to be an engineer on the factory floor would grab a product sample from the line and set it on the granite table. He then got to work measuring tolerances, comparing metrics on 2D drawings. It took lots of storage and time.
Aerospace manufacturers, however, have already embraced the world of model based definition (MBD). I learned this at a meeting with Dave Olson of Verisurf the other day. From design to manufacture, the move to paperless design and the use of 3D models has become a significant driver in simplifying processes and saving time getting to market. It’s a change that happened in analysis and simulation a decade ago.
These days, the design team is in control of the simulation, which is now often completed before the actual parametric CAD model is created. Now using MBD, inspection and quality assurance of parts can be accomplished using reverse engineering technology and by comparing metrics to the same 3D CAD model that is used by today’s CAM software for manufacturing. There’s no 2D drawing involved, all the tolerances exist in the CAD model, and the process takes minutes, not days. The complete enterprise and supply chain benefit. Suppliers can compare scanned data to their customers’ models and mistakes are corrected before manufacturing runs. Quality control in real-time.
I have heard from multiple sources that the design-release cycle for American automobile manufacturers is moving from four years to 18 months. It’s proof the combination of faster IT technology and easy-to-use simulation and design solutions can be a tremendous driver in today’s competitive environment. It drives innovations that will help all of us do our jobs better and improve the world we live in.
Speaking of improving the world, I would like to thank all of the companies that submitted projects to the Change the World Challenge this year. As you read through this issue I think you will be impressed with the designs engineers like yourselves have created. I look forward to seeing your submissions for our second-annual contest next year.
Steve Robbins is the CEO of Level 5 Communications and executive editor of DE. Send comments about this subject to [email protected].
Subscribe to our FREE magazine,
FREE email newsletters or both!Latest News
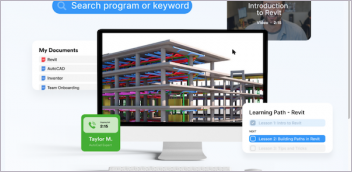

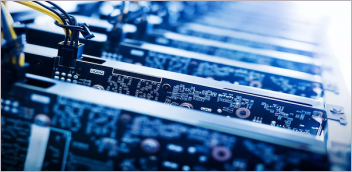
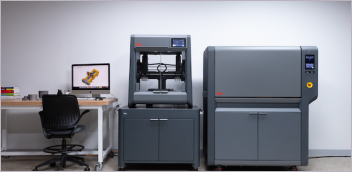