Solidscape Launches 3ZStudio

Solidscape’s newest offering, the 3ZStudio. Courtesy of Solidscape.
Latest News
September 4, 2012
3D printing has made its way into all kinds of industry. Along with the dental industry, jewelry manufacturers have accepted additive manufacturing (AM) with a certain amount of glee. The power to create investment casting molds using CAD and a 3D printer makes the entire process of manufacturing jewelry faster and less finicky.
Solidscape has released a new system, the 3ZStudio, designed specifically for the jewelry industry. The system comes with touchscreen operation, featuring universal language icons. At 21.4 x 18 x 16 in. (558 x 495 x 419 mm) the 3Zstudio is a desktop sized 3D printer making it easier to install in an office.
The new system has a build envelope of 6 x 6 x 2 in. (152.4 x 152.4 x 50.8 mm) with a resolution of 5000 x 5000 dpi (197 X 197 dots/mm) in X, Y 8000 dpi (158 dots/mm) in Z. Accuracy clocks in at ± 0.0010 inch/inch (±.0254mm).
The 3Zstudio uses Solidscape’s own 3Z Model material, which is a non-toxic, organic compound that, according to the company, vaporizes completely during burnout leaving no ash behind. Support material is provided by 3Z Support, which is a wax blend that has been designed with the intent of easy removal.
“Our partners share our excitement about bringing to the custom retail jewelry market Solidscape’s legendary high precision at an affordable price of $24,650 USD,” said Fabio Esposito, vice president of worldwide sales and marketing, Solidscape, Inc. “Until now jewelry retailers were forced to choose between the precision they needed, a performance level that fits their business and a price they could afford.”
Below you’ll find a video about the 3Zstudio.
Source: Solidscape
Subscribe to our FREE magazine,
FREE email newsletters or both!Latest News
About the Author
John NewmanJohn Newman is a Digital Engineering contributor who focuses on 3D printing. Contact him via [email protected] and read his posts on Rapid Ready Technology.
Follow DE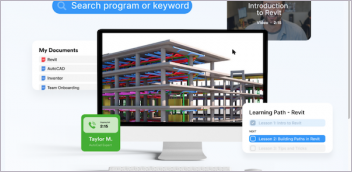

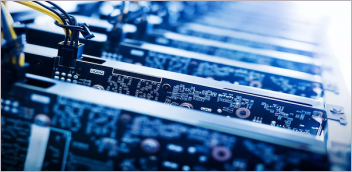
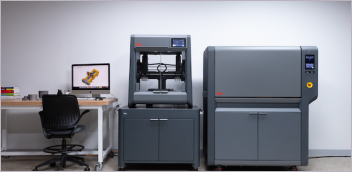