Latest News
January 1, 2007
By Ann Mazakas
In a move to capture more of the advanced milling market, the recent release of SolidCAM2007 R11 includes a new HSM (high-speed machining) module for complex 3D parts. Clearly targeted for mold, tool and die, aerospace, and other complex 3D milling applications, the HSM module offers technology often found in high-end CAM systems with something those other systems can’t — direct integration with SolidWorks.
Do not let the term HSM fool you though. The machining strategies in this new module make it a compelling choice for users with advanced machine tools as well as shops with older NC machines that are looking to improve productivity with reduced air-cutting and smoothing arcs that maintain continuous machine tool motion.
The goal of every high-speed CAM package is to keep the tool on the part as much as possible, moving as fast as possible. Toolpaths are smoothed to eliminate the problem of speed variations inherent in traditional toolpaths, where the tool must decelerate as it approaches a sharp change in direction and then accelerate again on the way back out. Toolpaths designed specifically for high-speed applications let the machine cut at consistent speeds with a constant cutter load that produces less pressure and vibration from the tool, which not only supports faster feed rates and faster spindle speeds at greater depths than traditional toolpaths, but also extends tool life and machine life as well.
![]() |
SolidCAM |
![]() |
SolidCAM |
Contour Roughing (left) uses helical lead-ins and smooth cutting passes to remove the maximum amount of material as fast as possible to prepare for finishing operations. Rest Machining (right) is an excellent choice for parts with vertical walls. It picks vertical, horizontal, and inclined corners out from the top down for a better machining technique.
All the roughing and finishing strategies in the SolidCAM HSM module produce smooth, gouge-free cutting passes. Retracts to high Z levels are kept to a minimum and do not go any higher than necessary, minimizing air cutting. Lead-ins and lead-outs are generated tangentially to the toolpath and also undergo a smoothing process.
A Module with DifferencesAlthough SolidCAM already offers a 3D Milling module, the SolidCAM HSM module is significantly different. The first thing users will notice is the new interface for HSM operations, which more closely mimics the tree structure within SolidWorks. The design of the interface simplifies the process of creating operations by guiding the user through the process of selecting geometry, cutting tools, machining parameters, and the links that define how the generated passes are linked together into toolpaths. If a step is missed, the system warns you.
![]() |
SolidCAM |
> > Morphed Machining uses flow boundaries to create a toolpath that adapts to the shape of the part.
Similar to other high-end systems, SolidCAM HSM generates a triangular mesh for all the faces of the 3D model geometry to improve surface accuracy. A faceting tolerance gives the user full control over the accuracy of the triangulated mesh.
The SolidCAM HSM module offers unique strategies where the machining parameters and linking strategies are defined separately. Cutting passes are calculated from the machining parameters and the linking strategies define how those generated machining passes are linked together into toolpaths. This method makes it faster to try different machining strategies because passes aren’t recalculated each time a new linking strategy is used, so the user can generate passes once and then try different retract moves, linking strategies, and lead-ins and lead-outs. This is a big advantage for creating complex parts because of the minimal impact on processing time.
Anyone involved in complex milling knows the importance of complete control over the areas to be machined. Creating boundaries to control the limits of the toolpath in the HSM module is easy. In addition to boundaries, any HSM toolpath can be controlled by the surface slope-angle of the part.
![]() |
SolidCAM |
< < SolidCAM HSM supports single-pass and multiple-pass pencil milling to finish corners without cusp marks.
SolidCAM provides a comprehensive set of boundary creation tools. Users can create 2D boundaries on the x,y plane of the current coordinate system from a bounding box around selected faces, a silhouette of those faces projected onto the x,y plane or a user-defined boundary from selected edges or geometry elements. Or, the user can automatically create 3D curves to use as 3D boundaries. 3D boundaries can be created around shallow areas and, for semi-finish or finish operations, the system can create boundaries around rest areas left unmachined by previous operations and around theoretical rest areas left by an imaginary tool. The most useful is the 3D toolpath boundary created around areas where the tool is in contact with selected surfaces or faces.
For advanced milling applications, having the right roughing strategies is critical for producing a consistent amount of rough stock for the finishing passes. SolidCAM HSM offers three strategies.
Contour Roughing is the main strategy for clearing large volumes of material. A series of offset passes are automatically calculated to remove the maximum amount of material without leaving large cusps of material that might cause havoc for finishing operations.
![]() |
SolidCAM |
> > The new SolidCAM HSM interface closely mimics the tree structure in SolidWorks to guide the user through the process of selecting machining technology, geometry, cutting tools, boundaries, cutting passes and tool path linking strategies.
With mold makers in mind, Core Roughing begins the roughing passes outside the material and works inward toward the boundary of the core. For parts that include both core and cavity areas, SolidCAM automatically switches between core and cavity roughing within the same program.
To quickly remove the rest of the material before semi-finishing or finishing, Rest Roughing uses an updated stock model of the material remaining from a previous operation to avoid air cutting. A succession of rest finishing toolpaths from a series of successively smaller cutters can be easily created, even on very large jobs. Rest Roughing is also useful when machining castings by trimming the passes to the cast surface model, with appropriate stock allowance.
For the artisan in every machinist, SolidCAM HSM has 12 finishing strategies to choose from, giving the user plenty of control. Constant-Z and Linear Machining are the most widely used finishing strategies. Linear Machining typically is used to semi-finish cusps from roughing operations and to finish shallow areas, while Constant-Z Machining is the best strategy for steep walls. By limiting the Constant-Z passes to contact angles between 30 to 90 degrees, the steeper areas are machined, leaving the shallower area for more appropriate strategies such as Horizontal Machining. Another option is 3D Constant Stepover, which creates 3D passes offset at a constant distance.
![]() |
SolidCAM |
< < Seen from the side, it is apparent that smoothing is also applied to lead-ins and lead-outs with a minimum of retract moves.
For steep walls in a radial shape, Spiral Machining is ideal. This strategy creates a spiral toolpath that keeps the tool in constant contact with the workpiece. This strategy not only reduces retracts but it eliminates the witness line common with standard Z-level passes. For radial areas that include shallow curved surfaces, Radial Machining is another good choice.
For surfaces with differently shaped boundaries that need to blend together, Morphed Machining controls the toolpath using flow boundaries. Morphed passes flow across the surface in a close-to-parallel formation dictated by the boundaries around them. Each path echoes the shape of the previous one and takes on some characteristics of the next one, thus gradually changing shape.
To solve the myriad problems that occur in corners, SolidCAM HSM offers quite a few options. Pencil Milling works well for machining into corners where the surface radius is the same as the cutter, removing material that no other strategy can reach. Parallel Pencil Milling is an extension to pencil milling where the pencil toolpath is offset to create multiple passes. 3D Corner Offset machining is similar to Parallel Pencil Milling except that the entire model is machined. Pencil milling can cause serious problems in vertical corners because both the flute of the cutter and the radius come into full contact with the material. In this case, the Rest Machining strategy is a better option. Rest Machining picks the corners out from the top down resulting in a better machining technique. Steep and shallow areas can both be machined in a single toolpath with different rest machining strategies.
To round out the 12, Boundary Machining drops the cutter onto the surface and runs it along a single boundary or a set of boundaries. This is typically used for engraving text, chamfering along a profile or along a mold tool runner detail.
The capabilities of a topnotch CAM system are now available fully integrated into SolidWorks. SolidCAM has packed a lot of power into an easy-to-use interface. Shops with advanced machine tools, shops looking to implement new technology, or shops with standard machine tools that want to maximize their productivity will be pleased to see what SolidCAM HSM can do for them.
Ann Mazakas is the president of Intelligent Creations LLC, a provider of services to the manufacturing industry. With an extensive background in engineering and manufacturing, she has built an in-depth knowledge of the CAD/CAM software industry. Send your comments about this article through e-mail by clicking here. Please reference “Smooth Moves” in your message.
Contact
SolidCAM
Or-Yehuda, Israel
Subscribe to our FREE magazine,
FREE email newsletters or both!Latest News
About the Author

DE’s editors contribute news and new product announcements to Digital Engineering.
Press releases may be sent to them via [email protected].
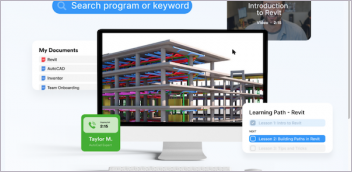

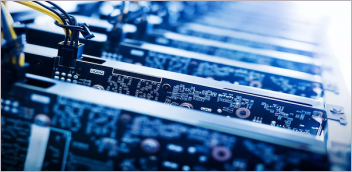
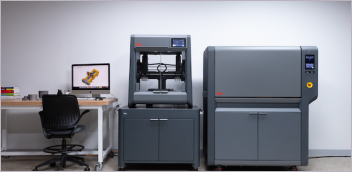