Simulation Transition: Meshing Nuts and Bolts
It’s essential to understand the fundamentals of how to adjust a mesh to obtain accurate and reliable results.
Latest News
May 1, 2019
One of the most enjoyable experiences in the process of building a race car is the first visit to the dyno. Tire pressures, high octane fuel and coolant are all carefully assessed prior to that first pull.
As the car’s baseline run displays power curve and peak horsepower, you’ll jump right to adjusting the air fuel ratio and ignition timing to squeeze as much power out of the engine as possible. This month we discuss this same process as it applies to finite element analysis (FEA).
It’s essential to understand the fundamentals of how to adjust a mesh to obtain accurate and reliable results. The FEA dyno session can be broken down into three distinct areas: mesh refinement, element quality and convergence of a result.
Mesh Refinement
To reduce computational resources and save time, you will probably consider starting your project with a coarse mesh. In doing this, mesh refinement is necessary in some areas to ensure that you have the fidelity required to obtain accurate results. Common considerations should be paid to areas with holes and to elements per shell thickness. Too few elements per hole, and the mesh is likely to provide false information for the stress, strain and displacement.
Refining the mesh with too many elements will work, but this may eat up time. This process is a careful balance between efficiency and accuracy, which comes from experience. Each vendor will generally have guidelines on what they recommend, based on their software.
Convergence Check
As you travel the path of tweaking and refining the mesh, you may notice that the stress values change. This process of evaluating whether stress values change is commonly referred to as a convergence check. The significance of this test is to understand if the stress values are accurately represented in your analysis.
We wouldn’t want to mistakenly interpret results from an inaccurate dataset. If your simulation software has P-adaptive meshing capabilities, you’ll notice that with several loops of refinement, the stress values will continue to climb or stabilize as the element size decreases.
Diverging stress values are often referred to as a stress singularity. Removing aspects of the CAD model through defeaturing can sometimes address these matters, as sharp re-entrant corners have infinite stress values. The types of goals you set for the analysis will ultimately drive the decision of refining your geometry to remove the singularity. In some cases, it may not be required.
Quality Checks
During the initial meshing of your part, you may have noticed that each element appears to be roughly the same size. But there are always a few stragglers that have some disproportionate edges.
When you generate a mesh, the software attempts to fill the entire volume of your part with elements under the parameters you have established. Often with organic shapes or quick transitions from thick to thin areas within the CAD model, the elements become slightly distorted. There are quality checks in place that can be plotted within the simulation software to assist you in uncovering this potential discrepancy.
Plotting the aspect ratio after the CAD model has meshed will show you the areas of high and low aspects. Elements with the ideal aspect ratio would be 1; however, this is not common. The higher the value, generally the less accurate the calculation.
Localized mesh refinement helps lower the aspect ratios. High aspect ratios are most concerning in areas of high stress, as they could very likely be throwing off the results.
Jacobian is another useful quality check that can only be used with elements that have nodes at midpoints within edges, or second-order elements. These types of elements can adapt to curved geometry better than linear elements and are often the choice elements. A Jacobian check ensures that the meshed elements have not developed concave distortion, which can lead to solution errors. If you receive negative values during this check type, mesh refinement and/or defeaturing will need to occur to resolve this problem.
Subscribe to our FREE magazine,
FREE email newsletters or both!Latest News
About the Author

Donald Maloy is a consultant analyst based in the greater Boston area. He also works as a certified simulation and mechanical design instructor for a software reseller.
Follow DE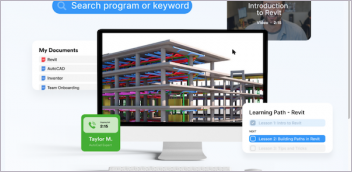

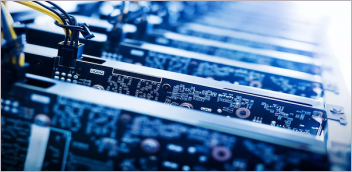
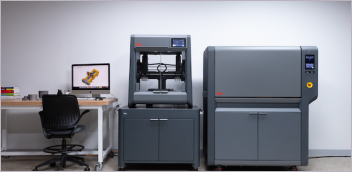