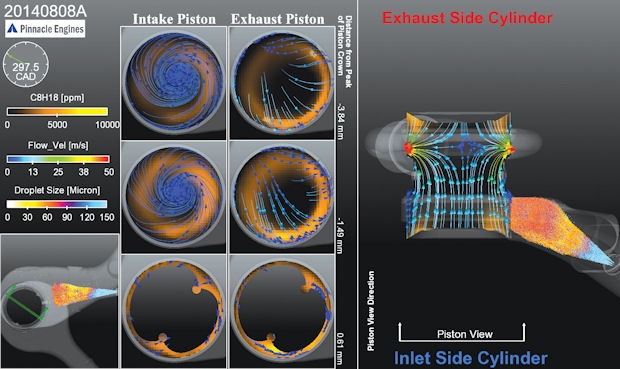
Simulating the activities inside the engine using CONVERGE CFD gives Pinnacle Engines valuable insights into how a piston crown shape affects the flow of fuel.
Latest News
February 1, 2015

You can learn a lot about the inner working of an engine from physical tests—how it heats up, cools down, behaves during acceleration and more. Looking at the test cell data from a dynamometer, Tony Willcox, director of simulation and controls at Pinnacle Engines, can gauge the engine’s average performance characteristics such as torque, power, fuel flow, and emissions. He can examine crank-angle-resolved data to analyze cylinder and port pressures, rotation speed and piston position during a series of combustion events. But Willcox and the simulation team at Pinnacle are also interested in what they cannot see or measure.
To extract every last joule of energy from fuel, they would need to peel off the engine cover and look inside to reduce energy loss from spark to exhaust. And that’s where they run into the limitations of physical tests. “Optical engine technologies exist that enable some visibility into the cylinder,” he says, “but they present their own sets of challenges. For example, their configurations are limited, and it’s very expensive to implement them.”
Another option is digital simulation. Using an advanced computational fluid dynamics (CFD) software program, Willcox can digitally recreate the fuel spray, mixing, air motion and combustion event to match the values collected from the physical test. Once he’s done that, he essentially has a digital version of the event, constructed in pixels—terabytes of them. This gives him the ability to see on a computer screen what’s happening inside the engine at every slice of time and space.
Converging on Combustion
“There are things we can’t measure in a test, but can mimic in simulation,” Willcox says. “For instance, we could turn off heat transfer to see what the engine’s efficiency would be without heat loss in the cylinder. Or we could turn off the leakages through the piston rings. With these options, we can better understand the impact of different factors on our design.”
Pinnacle Engines specializes in four-stroke, spark-ignited, opposed-piston, reciprocating sleeve-valve engines. The company states its mission as developing “engine architecture that provides 30–50% improvements in fuel economy without the typical cost penalty.” Its choice of software is CONVERGE CFD from Convergent Science, Madison, WI.
“We picked CONVERGE because it has a reputation for accuracy and it includes a detailed chemistry flame propagation model that enables predictions on our architecture without heavily relying on empirical models developed around conventional systems,” Willcox said. “There are characteristics in CONVERGE that don’t exist in other software, or are not as well-developed. For instance, CONVERGE’s chemistry model that estimates flame propagation using detailed chemistry in a sensible timeframe.”
Experimenting in the Cloud
Pinnacle Engines’ opposed-piston design has lots of design freedom. In a design optimization project, everything—from the shape of the piston crown to the induction and exhaust port shapes to the position and timing of the fuel delivery—is a candidate for revision. To arrive at the best geometry, Willcox and his colleagues can experiment with the digital model to see what happens to the engine’s efficiency, or how the flames propagate inside the cylinder. For that, Pinnacle Engines needs to conduct what’s known among the simulation experts as Design of Experiments (DOE).

Pinnacle Engines has a 172-core cluster onsite, dedicated to running two simultaneous 24/7 simulation jobs. Even if the company is willing to put its day-to-day simulation tasks on hold to run a DOE on the server, it still must address the need for additional software licenses. Typical simulation software licenses allow you to run simulation jobs one at a time. Some special HPC (high-performance computing) licensing programs allow you to distribute one large job on multiple machines—an ideal setup for those with in-house data centers. But DOE demands more than that. To be effective and timely, DOE sessions have to consider many design variations running in parallel on many computing cores.
“Is it possible to run the jobs one parameter at a time? Yes, possibly, but not within the timeframe we want the answer back,” says Willcox. “When we need an answer, we need it in a matter of days. We can’t wait for weeks. There are too many parameters to sweep, so even if we had the hardware, we wouldn’t be able to investigate all of them.” Unless the design parameters can be calculated in parallel.
The answer is on-demand computing infrastructure, specifically designed for DOE-type simulation. The answer, in this case, also turns out to be just 40 miles away from Pinnacle Engines’ San Carlos, CA, headquarters. San Francisco-based Rescale, a cloud simulation supplier, offers a scalable on-demand platform—a combination of software and hardware—for those seeking to do precisely what Pinnacle Engines wants to do. The company makes its solution directly available in the web browser. It also has a partnership with Convergent Science, which simplifies acquiring additional licenses for parallel simulation runs.
On its website, Rescale provides a chart that serves as a guide to calculate the cores and licenses you’d need to run a DOE and the associated cost.
“If you intend to run a certain type of simulation over and over, it makes sense to buy the hardware and bring it in-house with upfront investment,” Willcox says. “But that still limits you to doing one simulation at a time. It won’t let you do anything else in parallel.”
Crowning Achievement
From the simulation and seeing the flame propagation, Willcox and his colleagues gain valuable insights. “We found that one piston crown shape was causing the flame propagation to not reach certain regions of the cylinder, which resulted in unburned (wasted) fuel,” says Willcox. “Subsequent simulations on other piston shapes and test data showed matching and significant improvements in fuel economy. With such an open architecture, there are unique opportunities to improve engine performance by coupling un-measurable three-dimensional phenomena that are not obvious when simply measuring average test data such as hydrocarbon emissions or cylinder pressure.”
Willcox and his colleagues are now verifying a new piston-crown design through simulation and physical testing. “We ran simulation first [on the new design], saw an improvement, and then followed with testing the hardware,” he says. “Simulation predicted [a] 9.5% improvement in BSFC (brake-specific fuel consumption), test data was 10% at that load and speed. [The difference] was due to reducing unburned fuel (HC) emissions with new the new piston geometry by not inhibiting flame propagation near the end of the combustion event.”
Pinnacle Engines is undertaking an ambitious project to calibrate the CFD model to match its physical data. “[It] is not a simple or short process,” Willcox says. “We have been focusing on model tuning and calibration for more than one year (approaching 1 million CPU hours) and still do not have what I would deem an acceptable match to test data.”
Conventional use of internal combustion engine simulation has been, at best, an approximation—“a tool for relative accuracy,” Willcox says. But the ability to examine a sweep of parameters within a reasonable time makes simulation model tuning much more accurate. “We’re getting closer to accurately matching and predicting all measured channels ... which leaves us with confidence in the calculated values of the parameters that are not measurable inside our engine,” he says.
More Info
Subscribe to our FREE magazine,
FREE email newsletters or both!Latest News
About the Author

Kenneth Wong is Digital Engineering’s resident blogger and senior editor. Email him at [email protected] or share your thoughts on this article at digitaleng.news/facebook.
Follow DE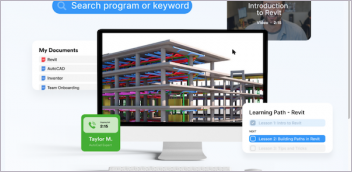

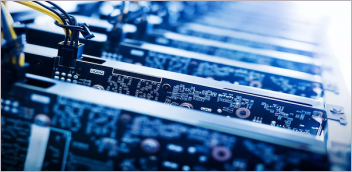
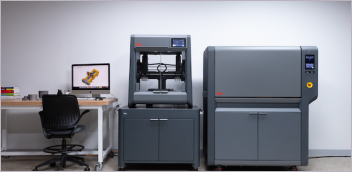