Latest News
May 1, 2012
By Pamela J. Waterman
What happens when you drill a hole in a multi-layer composite? Is there damage that will cause trouble when that structure is in use? And how precisely can you layer it in the first place? These are just some of the issues addressed at the 2012 SME Composites Manufacturing conference that took place in Mesa, AZ, in March.
Attendees heard about the increasingly important role that composites play in the design and manufacture of manned vehicles, wind-turbine blades and a host of applications in-between, plus new ways of dealing with them—many involving simulation for design and manufacturing.
For example, the new Boeing AH-64D Apache Block III combat helicopter uses an increased horsepower engine whose successful operation depends on redesigning a number of subsystems, with improvements that incorporate composites.
First, the new composite horizontal stabilizer saves 15.8 lbs. over the same design in metal, and also reduces the part count by 93. It still has a metallic torque box, but the skins and bars are composites. Second, the 256-in.-long main rotor blade will now be all composite, with a glass/epoxy hybrid spar laminate structure and a Nomex fiber core. And third, designers have achieved a 4-lb. weight reduction on the aft avionics pass-through doors, whose concurrent part-count reduction also makes them easier to manufacture.
Software Solutions
With so many operational benefits dictating the expanded use of composites, it was not surprising that several presentations addressed relevant software simulation tools for both design and production.
Bill Hasenjaeger is the product marketing manager for CGtech, developers of VERICUT software that simulates computer numerically controlled (CNC) machining to detect errors, potential collisions or areas of inefficiency. His company has used this experience to create VERICUT Composite Simulation (VCS), a package that reads CAD models and NC programs, and simulates the sequence of NC programs on a virtual machine.
Hasenjaeger talked about the need for process simulation software to verify the accuracy of automated fiber-placement (AFP) programs. In the real world of manufacturing, one or more bands of material are laid at the rate of 2,000 in. per minute. He emphasized, “On curved surfaces, you will have gaps and overlaps,” as the tape unrolls and is laid in position over a tool’s surface. Therefore, verifying the layout process and performing a design-for-manufacturing analysis are both critical tasks addressed by VCS software.
Dr. Shuji Usui, lead developer and computational mechanics engineer at Third Wave Systems, tackled another very relevant question: What happens to the microstructure of a composite material when holes are drilled into it?
![]() |
The simulation shows microstructure damage when drilling a hole through amulti-layer composite. The composite delaminates and shreds. Image courtesy Third Wave Systems. |
Third Wave Systems markets predictive, physics-based material modeling software used by companies to improve machining processes and is currently involved in early-stage R&D efforts related to composites modeling. The company’s AdvantEdge FEM software is a CAE solution traditionally targeted to the optimization of metal cutting, enabling users to analyze machining processes in 2D and 3D environments. Users are typically looking to improve part quality, increase material removal rates, and extend tool life.
Usui has now applied finite element (FE) modeling to predict the damage caused when twist-drilling holes into composites. He modeled a Constant Virtual Drill Bit with CATIA and NX software, then ran the model through AdvantEdge FEM on both composite and aluminum materials for comparison.
Cutting energy for metal includes plastic work (heat) plus friction, while cutting energy for composites must account for surface energy (transverse cracks) plus friction. Usui employed an unstructured mesh to solve the isotropic (metal) problem, and a structured mesh to handle the brittle behavior of the orthotropic (composite) problem, modeling each ply individually. AdvantEdge FEM was able to simulate a punch-shear test similar to the entry of a twist drill-bit, generating detailed animation graphics of layer delamination and fiber-shard splitting as the drill advanced.
Current Third Wave Systems work involves simulating various lay-up designs where layers are 90° to each other, 45°, -45°, etc. So far, the -45° orientation seems to result in the most internal damage. Usui is comparing the simulated results with laboratory experiments on an aluminum block and a graphite/epoxy composite. Future simulations will include the effects of the drill wearing down and cutting at an oblique angle.
John Schibler, chief engineer and IPT lead, Attack Helicopter Programs, for The Boeing Co., gave the keynote presentation about the Apache Helicopter program and its use of composites. He wrapped up his talk by noting a major wish-list item: room-temperature-curing composites. It would reduce the costs associated with autoclave curing, and allow the use of embedded-electronics sensors (which currently can’t handle autoclave heat).
For more conference information, see SME.org/composites and consider joining the SME Plastics, Composites and Coatings (PCC) technical community (SME.org/pcc). DE
Contributing Editor Pamela Waterman, DE’s simulation expert, is an electrical engineer and freelance technical writer based in Arizona. You can send her e-mail to [email protected].
Subscribe to our FREE magazine,
FREE email newsletters or both!Latest News
About the Author

Pamela Waterman worked as Digital Engineering’s contributing editor for two decades. Contact her via .(JavaScript must be enabled to view this email address).
Follow DE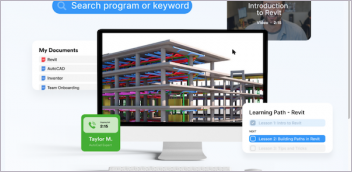

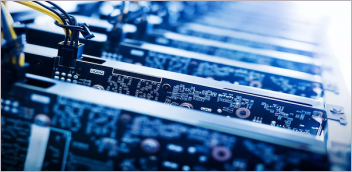
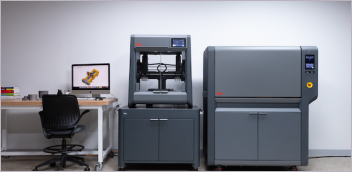