
Simufact 2020 includes enhanced interoperability with Materialise software and Renishaw printers. Image courtesy of Simufact.
Latest News
November 21, 2019
Simufact announced Simufact Additive 2020 at the formnext conference in Germany this week. The software suite for optimizing metal-based additive manufacturing (AM) processes now provides cost estimation of the build process, and improves interoperability with Materialise build preparation software and Renishaw printers to streamline manufacturing processes.
With the new release, users can now estimate print job costs for single components or assemblies. Not limited to the build process, the capability also includes subsequent processes such as cutting, machining, drilling and grinding. This helps the user identify the best build variant by taking into account printing costs.
The software also interfaces to Materialise using the 3MF industry standard 3D printing data exchange format. 3MF enables simple and reliable data transfer with third-party software and reduces timely efforts for the model set up.
Simufact Additive 2020 includes an integrated Renishaw QuantAM API for build job preparation and export, which provides the user an error-free-data transmission from Simufact Additive directly to Renishaw printers. This functionality also improves productivity because the entire work process from design to printed part is possible within the software, the company says. More interfaces are under development to allow easy connection to other printers as well.
This new software release applies new Adaptive Voxel Meshing technology to improve the simulation speed by automatically adjusting the voxel sizes in the part. This provides more immediate results to users, and makes the simulation more reliable and robust, the company says.
The Hybrid Manufacturing feature helps users combine Powder Bed Fusion additive manufacturing processes with conventional manufacturing. Simufact Additive 2020 makes it possible to define a given part upon which the printing will begin, including any internal stresses. As a result, stresses and distortions of the complete assembly and all single parts can be investigated.
New DED Simulation
Simufact also announced a dedicated simulation solution for improving the quality of direct energy deposition (DED) metal AM processes. Offered as a module inside its Simufact Welding 2020 software, it enables the user to quickly set up robust DED simulation models by importing existing tool paths direct from G-Code instead of defining weld paths manually. The software evaluates the stresses, strains, distortions, thermal history and hot spots during the manufacturing to identify distortions that are out of tolerance, and recommend compensations. Based on this, the user can adapt the G-code to optimize the DED printing process and improve quality.
“We are seeing significant demand for our new simulation solution because it helps to optimize such cost-efficient deposition production processes. DED offers a lot of innovation potential for hybrid manufacturing that combines conventional manufacturing technologies with additive manufacturing.” said Dr. Hendrik Schafstall, CEO and Managing Director at Simufact Engineering.
Subscribe to our FREE magazine,
FREE email newsletters or both!Latest News
About the Author

DE’s editors contribute news and new product announcements to Digital Engineering.
Press releases may be sent to them via [email protected].
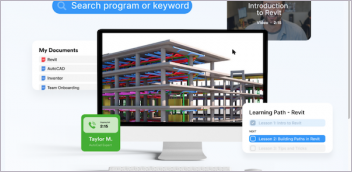

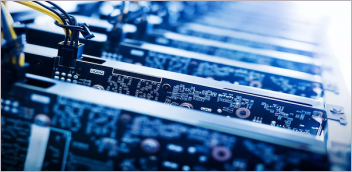
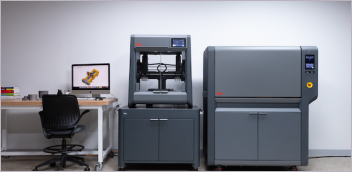