Siemens Debuts Manage MyMachines
Manage MyMachines is a MindApp for enhanced transparency at the digital enterprise.
Latest News
February 4, 2019
Siemens' new Manage MyMachines is one of the MindApps within the rapidly emerging Mindsphere concept. This cloud-based “platform as a service” enables the full data tracking of machine kinematics as well as production data and Manage MyMachines serves as the initial point of entry into this digital world, combined with edge technology.
Digitalization is no longer an intimidating notion for all types of companies in the manufacturing world. In fact, it is or soon will be an essential component in the operating philosophies at all companies. In response to this exciting evolution of Industry 4.0, Siemens opens the door to the digital world with Manage MyMachines, creating new and viable possibilities for increasing productivity, in combination with the highest achievable quality output and adherence to production schedules, plus reduced maintenance and service costs. “Simply stated, this concept will be a gateway to the digital factory for all of our associates in the machine tool world, including builders, integrators and end users of all shapes and sizes,” says Sascha Fisher, head of the machine tool systems group at Siemens in the U.S.
For the builder, this development translates into an immediate ability to monitor the global install base. Shops and production departments, in tandem with their system integrators and other business partners, will benefit from a transparent display of all CNC equipment
on the floor, regardless of location, brand, function or usage.
As a MindApp within the Mindsphere portfolio, Manage MyMachines is integrated in the cloud-based, open IoT operating system, as it allows access to all critical machine tool information, from bearing temperature to production by shift or job, all in a selectable priority scale, based upon user needs. Unexpected line downtimes and off-normal machine kinematic conditions can be quickly identified and rectified. Better yet, predictive maintenance can be programmed, so an upcoming failure can be anticipated, with alerts sent to a local distributor, for example, to deliver the needed components.
Complete asset management is further possible via Manage MyMachines, as resource consumption and energy usage are trackable, all in the cloud and all accessible through the app in real time.
Sources: Press materials received from the company and additional information gleaned from the company’s website.
More Siemens Digital Industries Software Coverage
For More Info
Subscribe to our FREE magazine,
FREE email newsletters or both!Latest News
About the Author

DE’s editors contribute news and new product announcements to Digital Engineering.
Press releases may be sent to them via [email protected].
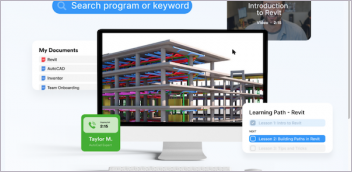

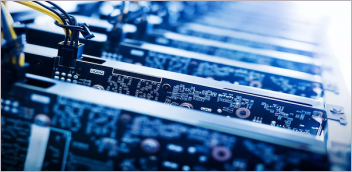
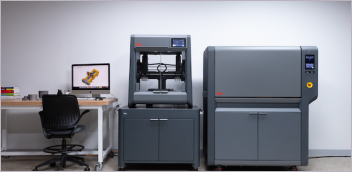