
AgustaWestland AW101—Leonardo helicopters. Image courtesy of Leonardo, SFM Technology and BigRep.
March 14, 2023
Helicopters use automatic folding software, folding in their blades like a bumblebee, explains SFM Technology. Stabilization remains a key priority for smooth embarkation possible. This is achieved by using a main rotor blade restraint cradle.
“When a helicopter is on board a ship, it has the facility to fold its helicopter blades back,” says Gary Wilson, head of Technical Sales at SFM Technology's AeroAddtive division. “Once the helicopter blades are folded back at sea, it's still windy, and the blades can flap. So, these blades need to be restrained so this flapping doesn't occur.”
For the aerospace and defense company Leonardo, tasked by the Ministry of Defence to provide AgustaWestland AW101s for the Royal Navy, they found that their pre-existing main rotor blade restraint cradles were not living up to their standard. Leonardo turned to SFM Technology and its AeroAdditive section to provide a solution. The result was the first main rotor blade restraint cradle—measuring 900x230x160 mm—created with 3D printing.
SFM turned to additive manufacturing.
“This is quite a long process, so we had a look at many aspects of 3D printing,” says Wilson. “We must look at cost, efficiency, and of course, the size, which pushed us to BigRep. Eventually, we looked at the BigRep PRO as we had to look at a production 3D printer, which I believe the BigRep PRO can provide. The machine is used as a production machine, so every rotor blade restraint cradle will be going to the end customer.”
SFM Technology found through stress-testing that their 3D-printed printed parts performed better than original, non-printed parts. By using Hi-Temp CF—a carbon fiber reinforced material with high-strength properties—the blades have resistance to wear and tear and any external pressure.
“To date, we have printed 30 cradles, consisting of 60 halves, since January,” Wilson says. “If we were to do that in a traditional way, we would have done about a quarter of that. So, you can see that 3D printing is far quicker, as we don’t have any adjustments to make, or if we do, they’re very minor and can be quickly overcome.”
Advantages of Hi-Temp CF
“We carried out many tests to establish which was the most suitable material within the budget given,” Wilson says. “Having looked at the data sheets, we felt that Hi Temp had a slight advantage over the other BigRep materials.”
Once the support material is removed, sandpaper and its equivalents are used to smooth the surface. Then bushes are inserted in the hinges, before using helicoil inserts when required. Once the cradle is painted to the customer’s specs, the rest of the metal parts are added along with the foam on the inside of the cradle, protecting the main rotor blade when the restraint cradle is fitted.
“In the aerospace industry, there are many designers still slightly nervous about 3D printing. By using these cradles, we can demonstrate that 3D printing can be used in the aerospace industry quite comfortably from a strength, repeatability, and quality side,” Wilson says.
SFM Technology are now looking to use the BigRep PRO as a batch 3D printer, able to sequence production, according to Wilson.
Sources: Press materials received from the company and additional information gleaned from the company’s website.
Subscribe to our FREE magazine,
FREE email newsletters or both!About the Author

DE’s editors contribute news and new product announcements to Digital Engineering.
Press releases may be sent to them via [email protected].
Related Topics
All topics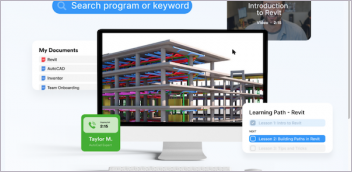

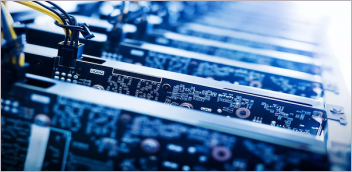
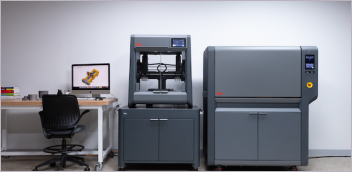