Scanning Supercars
How Creaform's portable, hand-held scanning unit helped a New Zealand company develop a model of its handmade supercar.
Latest News
April 1, 2007
By Patrice Parent
Supercars are high-performance, street-legal sports cars designed to fulfill the fantasies of the wealthy while eliciting awe and envy in the rest of us. They are typically exotic and rare, and one New Zealand company has recently filled a perceived gap in the competitive yet potentially highly profitable international supercar market with its own specimen.
The Hulme F1 |
< < A fast scanning method was used to duplicate this fast Hulme F1, a handmade supercar.
Therein lay the problem for Hulme Supercars. When the final version was ready to go into production, the one-of-a-kind body that wrapped the dual overhead-cam 301 c.i. BMW M5 V8 engine had to be reproduced, but there were no CAD files from which molds could be built. A full 3D scan of the Hulme F1’s exterior would be necessary to create a CAD model.
To save some time, the company turned to ScaNZ 3D in Hamilton, New Zealand. The car was transported to a garage near ScaNZ 3D so that it could be scanned indoors, during a brief stop in its journey from Wellington to Auckland on a promotional tour around the North Island of New Zealand.
ScaNZ 3D, recently appointed as the New Zealand distributor of the HandyScan 3D, was preparing for the scanner’s launch event the following evening. As an application engineer for Creaform, maker of the HandyScan 3D hand-held scanner, I was assigned to provide product demonstrations and training in its use to ScaNZ 3D’s team. Since this was the first major project for ScaNZ 3D using the HandyScan 3D, I supervised the scan work. But because the HandyScan 3D is so easy to use, a ScaNZ 3D technician who was still undergoing hands-on training helped set up the car for scanning and performed several of the scans using a second HandyScan unit.
Courtesy Creaform |
> > The author demonstrates the proper use of the Creaform HandyScan 3D to the staff at ScaNZ 3D in New Zealand.
We were able to cut the typical scanning time by using two HandyScan 3D units to scan different parts of the car simultaneously, which is one unique feature of our system. It allows the user to easily register scans under a common reference or coordinate system. This is possible because one single mapping file (positioning features file) is created, copied, and then opened by the VxScan software resident in two separate computers. Since the coordinate system of the scan was directly linked to the positioning file, using the same file with two scanners would generate scans that were in the same coordinate system and therefore correctly aligned in relation to each other.
We used targets or positioning features to position the scanner in space. These reflective and self-adhesive targets are manually affixed to the surface of the object and are used by the cameras in the scanner to create a positioning or reference grid. After a brief session affixing the reflective targets and making minor adjustments to the indoor lightning to reduce reflections on the car, everything was good to go.


The complete scan work was finished in less than a third of the time it would have taken to scan using traditional methods.
The complete scan work was finished overnight, shaving several hours off the time it would take to scan the car with a traditional arm-mounted scanner or laser line probe. Engineers estimated the scanning took less than 35% of time required to complete the same task if an articulated arm and laser line probe had been used. The handheld nature of the HandyScan allows much more freedom and simplicity. Post-processing of the captured data is also significantly faster, since the VxScan companion software directly outputs data in the STL file format. Therefore, all the time usually spent working on processing a point-cloud file is avoided.
To guarantee the best results, the engineers studied the correct balance between scan resolution and the number of scans. A box of 1,500mm in size was defined inside VxScan to reduce the number of separate scans while optimizing the resolution and to meet the client requirements. VxScan’s multiresolution function was also used in order to define feature lines and fine details.
A unique feature of the HandyScan 3D is that the user can see the surface of the object appear in real time on a computer screen. This helped immensely with the Hulme F1 project because it meant we were able to capture a complete data set without holes. This alone saved time and avoided frustration during postprocessing, and enabled a rapid turnaround on the job. Otherwise, the car’s owners might have had to withdraw it from a scheduled promotional show.
Since every scan was in the same coordinate system, no alignment was needed prior to the actual stitching of the scans. At the end of the scanning session all the scan results were combined to produce the end result: one single and clean mesh of the whole car.
“It was just so easy,” exclaimed Luke Cawley, ScaNZ 3D’s head technical engineer. “I knew that the HandyScan 3D would be much simpler to use than almost any other method, but the ease with which we completed the scan surprised me.”
Patrice Parent received his degree in mechanical engineering from Laval University in Quebec City. He is an application engineer with Creaform. Send your comments about this article through e-mail by clicking here. Please reference “Scanning Supercars” in your message.
HandyScan3D vs. Other Scanners
The HandyScan 3D is portable, easy to use, reliable, and accurate. According to Creaform, the four main reasons users choose it are:
1) Since the scan is referenced using markers or positioning targets, it does not matter if an object is moved during the scan session, since all the targets will move together by the same amount. (On the other hand, an arm-mounted scanner is usually mounted on a heavy-duty tripod. The car or other object cannot move at all during scanning because the whole scan is referenced by the base of the arm, which must remain static.)
Drawing of the Hulme F1 |
2) The HandyScan 3D’s targets file and the coordinate system will always be the same. With a traditional system a minimum of four tooling balls would need to be affixed on the part to reference one scan to another. The spheres need to be scanned with a high degree of accuracy in every scan, along with the actual surface, and then aligned together in order to align the different scans.
3) The HandyScan 3D’s portability makes it much easier to transport to perform onsite scan work. It easily fits as a carry-on item in almost any commercial airplane. Other systems are barely transportable.
4) The HandyScan 3D interfaces directly via plug-ins to some of the most popular CAD/CAM post-treatment software packages currently in the market, including Geomagic, Polyworks, Rapidform, and SolidWorks. Users also have the option of importing the STL files to any software package that can handle such files.
Company Info
HandyScan 3D
Creaform, Inc.
Quebec City, QUE
Hulme Supercars
Auckland, New Zealand
ScaNZ 3D
Hamilton, New Zealand
Subscribe to our FREE magazine,
FREE email newsletters or both!Latest News
About the Author

DE’s editors contribute news and new product announcements to Digital Engineering.
Press releases may be sent to them via [email protected].
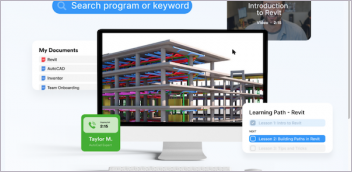

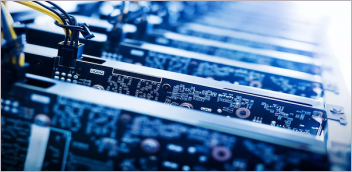
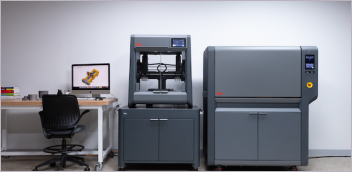