New & Noteworthy: Safe, Cost-Effective Metal 3D Printing - Anywhere
Desktop Metal’s Studio System offers turnkey metal printing for prototypes and batch manufacturing.

The Desktop Metal Studio System 2. Image courtesy of Desktop Metal.
Latest News
March 13, 2024
Metal 3D printing is rapidly expanding its presence in manufacturing, with systems capable of producing complex metal prototypes and parts at a high resolution. But the learning curve for this type of additive manufacturing can be high, which can make adoption difficult and costly.
The Desktop Metal Studio System™ provides an easy-to-use metal additive manufacturing platform that can be deployed safely in any environment, offering designers and manufacturers a cost-effective way to quickly turn their tools, jigs, and products into reality. The Desktop Metal solution provides all of the hardware, software, and feedstock needed to rapidly begin printing metal parts.
To produce high-quality prototypes or end-use parts with metal 3D printing often requires a significant amount of operational knowledge, and the additive manufacturing equipment is usually not office friendly. Like their machine shop cousins, some metal printers can generate a lot of material waste, heat, and fumes. For design engineers that want to print a metal prototype or casting, options are limited.
The Desktop Metal Studio System solves all of these challenges, offering the benefits of metal 3D printing that can be accessible in any office, studio or lab setting, in an easy-to-use package that includes both hardware and software.
The Studio System is easy to use and can be safely operated in any environment. Image courtesy of Desktop Metal.
The Studio System features a two-step print-and-sinter process that requires very little training or operator intervention. The furnace in the unit heats parts to remove the binders, then increases the temperature to provide industrial-strength sintering.
The Studio System’s Bound Metal Deposition™ (BMD) technology leverages safe-to-handle feedstock rods made of pre-bound metal powders and polymer binders that can be extruded into complex shapes and then sintered to full density. For users, this means there is no loose powder, no special powder handling requirements, no lasers, no solvents, and no need for specialized facilities to house and manage the print process. Designers can print parts or products in a design lab or even right in their office. The metal rods are available in a variety of alloys..
Desktop Metal Live Studio™ software intuitively guides users through the entire metal 3D printing workflow, including model preparation, automated sintering cycles, and job queueing. It automatically scales and orients parts and applies expert metallurgy to optimize fabrication.
The system also creates Separable Supports™ for complex shapes, which reduces the need for time-consuming post-processing. These supports are generated in the Live Studio software with strategic seams and printed with a ceramic release layer that can be easily broken away by hand.
The Studio System helps users take control of their prototyping processes, providing simplified and easy-to-manage metal printing that lets design and engineering teams focus less on the equipment and more on creating innovative parts and products. In-house metal printing enables rapid prototyping and design iteration, further accelerating the development process.
To learn more about Desktop Metals Studio System, visit the product webpage here, and visit the links below.
Case Study: How Ecrimesa Group Uses the Studio System for Rapid Prototyping
On-Demand Webinar: Walkthrough of Adopting Office Safe 3D Printing
Subscribe to our FREE magazine,
FREE email newsletters or both!Latest News
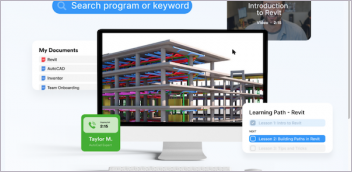

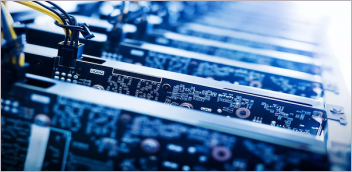
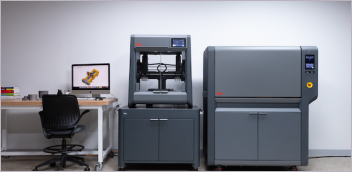