RP&M: Then and Now
What a difference a decade (or two) makes in the rapid manufacture of parts and prototypes.
Latest News
March 1, 2006
By Pamela J. Waterman
What a difference a decade (or two) makes in the rapid manufacture of parts and prototypes.
Nine years and 50 articles ago, DE Editorial Director Tony Lockwood announced his first assignment for me: write about rapid prototyping. “Um, how is that different from just making parts really fast?” I wondered. In his usual, helpful way he replied, “Ask around, you’ll find out. It’s really cool technology.”
Since then, I’ve attended the Society of Manufacturing Engineers (SME) Rapid Prototyping and Manufacturing Conference (first held in 1993) as it has moved from Detroit to Chicago to Cincinnati and back, visited countless vendors and service bureaus, earned SME’s Rapid Prototyping & Manufacturing (RP&M) Professional Certificate, and benefited from the goldmine of expertise shared by such community gurus as Terry Wohlers and Todd Grimm. I’m happy to report that Tony was right: this RP technology, in all its flavors, is definitely cool, and undeniably here to stay.
To explore the roots of additive rapid prototyping (there’s also subtractive), you actually need to go back two decades. A research chemist named Chuck Hull, while working at a company involved in material science, had one of those “ah-ha” moments involving liquid epoxies and acrylates spilled on the floor. Observing how quickly they hardened, he jumped on the idea of using lasers to purposely cure certain materials to build up a particular shape.
› › This 1988 statuette was built on a 3D Systems SLA-1 as part of an art contest. The file was created in Alias and built using liquid resin later cured in a UV oven. The part is almost 6 in. tall.
Just one year after starting his own business in 1986, Hull introduced a viable system whose CAD-driven laser selectively hardened areas of a pool of liquid photopolymer, layer by layer, to form fully 3D parts. The technology of this equipment, known as stereolithography apparatus (SLA), has since been continuously developed to produce durable, finely detailed parts as large as 1.5 meters (59 in.) across, in a variety of materials. That company was 3D Systems, and Hull still innovates as its chief technical officer; the rapid prototyping community considers him the granddaddy of all rapid prototyping.
‹ ‹ This 18-in. part was built in a new 3D Systems 7000 series machine. Its nanofilled material provides excellent dimensional stability and greater detail than previous systems. The part is within +/- 0.005 in. in all dimensions.
Over time, the RP world has seen its share of rising stars and not-quite-sustainable endeavors. You know you’ve been in this business a while if you remember Cubital, Helisys, Sanders Prototype, and Specific Surface. Or, if you’re just exploring the RP world, you’ll encounter a strong lineup of both ten-year-plus companies, including Stratasys, Solidscape, and Z Corporation, and more recent entrants such as POM and Solidica. 3D Systems continues a 20-year leadership role, during which it acquired another successful RP company, DTM, in 2001, gaining an additional product line based on selective laser sintering (SLS) technology. A Word from Our Users
Long before there were CAD files, inventive designers were taking the first steps toward digital fabrication (the full range of computer-controlled additive and subtractive processing). Lon Cooper, now a master model-maker at 42 Eagle Inc., started professional work in wood and clay back in 1969. He became interested in subtractive modeling systems first while working for Revell, the model kit company, then in positions in the aerospace and recreational vehicle industries. Cooper saw CAD emerging in its 2D form, and, independently, created physical 3D models by “egg-crating” (filling in with clay) the model slices generated in AutoCAD and cut from wood.
› › Because of improvements in direct-metal rapid prototyping, this turbine test rig, which is currently under evaluation, shows much more detail and finer surface finish than was possible just seven years ago. (Image courtesy of NASA Marshall Space Flight Center.)
At the same time, having watched the progress of 3D Systems’ SLA offerings, Cooper was sure that additive processing could be a viable modeling approach, too. His own efforts were limited by the number-crunching power of typical computer systems. “Around 1990 it took all day to do AutoCAD on a 386-turbo PC,” remembers Cooper, but he beta tested McNeel North America’s Rhino 3D design software, and used it successfully to create models cut from wax on a Roland subtractive RP (SRP) machine.
Since then, Cooper has made everything from jewelry to medical prostheses, using both Roland SRP equipment and 3D Systems SLA machines. “Whether taking cells and printing kidneys, or ‘faxing’ models into space to a NASA machine,” he observes, “the future of RP&M is non-stop.”
Already quite busy at NASA Marshall Space Flight Center is Ken Cooper (no relation to Lon), a structural materials engineer at the center’s rapid prototyping laboratory. He has been intrigued by Stratasys fused deposition modeling (FDM) RP systems since 1993. FDM technology uses a temperature-controlled head to extrude and deposit semi-liquid material that bonds and hardens in layers.
“It looked like FDM would function in microgravity or outer space,” Ken explains, where “we will need ways to fabricate replacement parts or new designs on the fly. We modified an FDM system and flew it on the zero-gravity experimental parabolic (KC-135) aircraft.”
‹ ‹ This camera housing is being produced by a current Roland MDX subtractive rapid prototyping (SRP) machine. It handles a wide variety of materials (not possible in the early days) and generates a smooth surface finish.
His laboratory group is also evaluating direct-metal RP systems for use on the Moon or Mars. Cooper notes that in his 13 years in the industry, he has seen RP machines get faster, more accurate, more user-friendly and reliable, but there’s still a way to go to reach true “manufacturing.” He adds, “Perhaps most important are the advances in materials, from waxes and acrylics to titanium and steel.”
Scicon Technologies, a service bureau based in Valencia, California, specializes in SLA and SLS parts for a very good reason. President and Founder Scott Turner started working at 3D Systems in 1986 as the company’s first training instructor for the new world of SLA products. Learning the systems inside and out, Turner started his own company in 1989, and has witnessed 3D Systems’ continuing improvements in machines, accuracy, material, and part-size capabilities.
“Originally our build size was 10 inches by 10 inches by 10 inches, and it took days to build a part,” states Turner. “Now we can make very large parts (up to 1.5m with the new Dual-Vat Viper Pro SLA) and run hundreds or thousands of parts at a time.” Like Ken Cooper, Turner sees the field of materials as where the action is. “Even five years ago, we had one or two materials, and now we have five or six.”
You know a process is successful when users won’t allow discussion of their systems or applications—not from dislike, but from a fierce desire to keep their techniques unknown to competitors. Such is the case for Soligen, an MIT-licensed 3D-printing (3DP) system developer, where some things are hard to improve upon.
› › Using current technology, ProMetal steel liners for this engine block were cast directly into aluminum. The five-year-old company uses either sand or metal powders with binders to create large (59 in. wide) parts. It is currently researching using inorganic, environmentally friendly binders so internal passages can be cleaned out with water.
Soligen President Yehoram Uziel says that from the beginning, his Direct Shell Production Casting (DSPC) systems have been extremely fast, reliable, and accurate for making molds to cast almost any metal. He points out that, over time, “The DSPC systems have not changed at all.” Instead, improvements over the years have focused on the bigger picture, incorporating such casting techniques as chilling, sophisticated core venting, and controlled-flow gating. The end parts are indeed rapidly made and extremely accurate, capable of high-temperature/high-pressure operation.
Rapid casting, direct metal parts, and production tooling are three areas where another 3DP licensee has grown its business. Five-year-old ProMetal uses either sand or metal powders with binders to create both mold/core sets and direct parts, with rapid castings now as large as 59 in. long. One of its current research areas involves inorganic, environmentally friendly binders that allow even complex, internal passages (typically found in engine blocks) to be cleaned out with water.
Visions for 2016According to Wohlers Report 2004, back in 1994 there were a total of 922 additive processing systems sold worldwide. Jump ahead to 2004 (the most recent data available) and the total figure stands at 14,381 installations.
These Stratasys models show improvement in both surface finish and fine-feature detail. The dragon model from 1998 was made on the Stratasys Genisys from polyester. It shows some of the “stairstepping” that was more common 10 years ago. The multipin connector (at right) was built from ABS plastic on the FDM Titan, a new machine that builds models at resolutions as fine as 0.005 in. What you can’t see are the much faster speeds possible with the new technology. Click images to enlarge.
Clearly, the RP&M players are not standing still. In fact, at 3D Systems, President and CEO Abe Reichental reports that Chuck Hull is as creative as ever, having just started up a new corporate R&D lab. The facility will anchor the company’s West Coast operations as the headquarters moves this year to a new location in South Carolina.
Z Corporation, yet another of the 3DP licensees, recently merged with Contex Scanning Technology and continues to improve its machines, materials, and price points. The latter consideration supports Scicon’s Turner as he observes, “At the end of the day, the laws of economics are almost as strong as the laws of physics.”
Still, NASA’s Ken Cooper envisions an RP system on its way to the moon in just another decade. Who knows? Perhaps DE’s next 10-year perspective will feature images of parts made on lunar-based equipment. Tony, put me down for it on the 2016 editorial calendar, I’m packing my bags.
Contributing Editor Pamela J. Waterman is an electrical engineer and freelance technical writer based in Arizona. You can contact her about this article by clicking here. Please reference “RP & M, April 2006” in your message.
Factors in the Future of RP&M
By the time Henry Ford had pretty well figured out how to build Model T cars, he realized he also needed to go help develop the highway infrastructure. One without the other just wasn’t going to go far.
For RP&M pioneer 3D Systems, the parallel challenge back in the late ’80s was the lack of widespread CAD system use. Company President and CEO Abe Reichental explains, “The highway infrastructure for us, in the early days, was the availability of affordable CAD seats, because that’s the prerequisite for any user to harness this capability. This was available only to an exclusive club of end-users who could afford the cost of solid-modeling CAD and the cost of the early SLA systems.”
“Today, to look ahead,” he states, “what’s going to accelerate the adoption of this technology, both in the early design iterations and all the way through the manufacturing process, is the introduction of more affordable systems.” The company’s plans include offering desktop 3D printers at prices comparable to today’s 2D plotters, as well as more engineered plastics and metals that mimic the properties of traditional materials. Reichental adds, “We need to give customers solutions that improve their own bottom line.—PW
Companies Mentioned
3D Systems, Inc.
Valencia, CA
42 Eagle, Inc.
Corona, CA
951-479-3741
Robert McNeel & Associates
Seattle, WA
ProMetal, Inc.
Irwin, PA
Roland Advanced Solutions Division
Irvine, CA
Scicon Technologies, Inc.
Valencia, CA
Solidscape, Inc.
Merrimack, NH
Soligen, Inc.
Northridge, CA
Stratasys, Inc.
Eden Prairie, MN
Wohlers Associates, Inc.
Ft. Collins, CO
T. A. Grimm & Associates, Inc.
Edgewood, KY
Z Corporation
Burlington, MA
Subscribe to our FREE magazine,
FREE email newsletters or both!Latest News
About the Author

Pamela Waterman worked as Digital Engineering’s contributing editor for two decades. Contact her via .(JavaScript must be enabled to view this email address).
Follow DE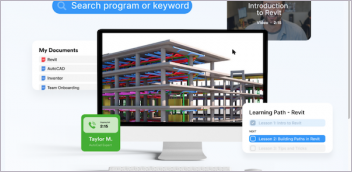

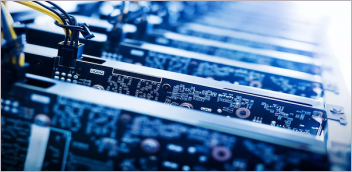
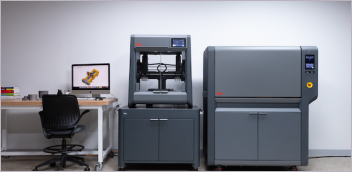