Robots to the Rescue
The Fukushima Daiichi nuclear disaster and other recent events have led the U.S. Department of Defense to issue a challenge intended to foster innovation around humanoid disaster-response robots.
Design Exploration and Optimization News
Design Exploration and Optimization Resources


Latest News
June 1, 2013

There’s Thor, RoboSimian, CHIMP, Hubo and a pack of other contenders. Some are big, all are brawny, and each has keen powers of perception and dexterity.
They’re not superheroes, per se, but they do have superhuman powers.
They are among the custom robots competing in Track 1 of the Defense Advanced Research Projects Agency (DARPA) Robotics Challenge, an event designed to spur the development of robotics technology to aid in disaster-response operations.
The devastation of recent natural and manmade disasters, including the Deepwater Horizon oil spill and the earthquake-decimated Fukushima Daiichi nuclear reactor plant, highlight mankind’s inability to respond effectively to certain disaster situations. Recovery operators are often unable to get close enough to complete a mission because of safety or inaccessibility obstacles like nuclear contamination, structural instability or intense temperatures.
The Robot Brigade
While today’s robots are certainly helping assuage these harsh situations—for example, robots were used to clean up and get the crippled Fukushima plant back online—there are few specifically designed for this kind of work. Most aren’t equipped to navigate environments scaled to the human world, according to DARPA officials.
This glaring gap in robotics technology was the genesis for the DARPA Robotics Challenge. The goal of the program is to task the brightest minds in robotics to develop new technology that can execute complex tasks in dangerous and degraded human-engineered environments using vehicles and tools commonly available in populated areas. Improvements in the areas of supervised autonomy, mounted and dismounted mobility, dexterity, strength and platform endurance are among the chief requirements for building a robot that’s actually capable of performing disaster response at the scale DARPA envisions, according to Gill Pratt, Ph.D., DARPA program manager. What they collectively enable, he explains, is a robot that is adaptable, capable of operating in an environment that’s engineered for humans, even if it’s degraded by a disaster, and generally robust enough to complete an actual mission from beginning to end.
“There have been great advances made in robotics, especially humanoid robots, both in the United States and internationally over the last decade. But most were developed and evaluated in labs and other controlled spaces,” Pratt explains. “With the DARPA Challenge, we are looking to improve the capabilities of the robots by putting them into real-world situations, with their great variability and sometimes without skilled human operators to direct every movement the robot makes. If successful, we will be raising the bar for the field of robotics, moving the technology closer to working in unpredictable environments.”
The Heart of the Challenge
Enabling supervised autonomy in robots will be a key to success. What this means, Pratt says, is shifting the process of directing robots from tele-operation, where human operators give a robot step-by-step commands, to task-level autonomy, where operators give commands like “Open the door” or “Climb the stairs,” and the robot is able to figure out the basic steps necessary and complete those tasks by itself. This is necessary in a disaster-response robot, Pratt notes, because there is no guarantee of a clear communication channel between human and robot at the scene of any disaster.
Achieving supervised autonomy will demand improvements in sensors, hardware and software. It might also include machine learning, which will leverage new algorithms to control the robot’s interaction with its environment and enable perception and tactile feedback, Pratt says. It also requires a relatively simple user interface so that humans who are not experts in robotics can issue commands and confidently anticipate the response.
To prove their mettle in the DARPA program, robot challengers will be faced with a disaster scenario that will require them to perform a series of operations, including:
- drive a utility vehicle at the site;
- travel across rubble;
- remove debris blocking an entryway;
- open doors to enter a building;
- climb a ladder and traverse an industrial walkway;
- use a power tool;
- locate and close a valve near a leaking pipe; and
- attach a connector like a wire harness or fire hose.
The teams will be evaluated on their ability to complete the simulated tasks on Atlas, the robot designed by Boston Dynamics based on its Atlas humanoid robot platform and designed specifically for this competition. From there, teams will move on to the physical part of the challenge, with trials set for December 2013. The final leg of the contest will be held in December 2014, where teams have their robots tackle an end-to-end disaster scenario—with the winner nabbing a $2 million prize.
While a substantial heap of prize money can certainly be a draw, leaders of most Track A teams (the teams building their own custom robots) say the real impetus for participating in the DARPA challenge has more to do with advancing robotics technology for the good of solving humanitarian problems. A competition serves as a forum to foster innovation and creativity, particularly when the technology challenge is so extreme, notes Anthony Stentz, Ph.D. Stentz is a research professor at Carnegie Mellon University’s Robotics Institute, the director of the National Robotics Engineering Center (NREC), and the lead of the CMU-NREC’s Team Tartan, which is working on the CMU Highly Intelligent Mobile Platform (CHIMP) robot.
“Challenges do a number of things: They install an element of excitement, and the competition builds lots of energy around a task or project,” says Stentz, adding that CHIMP is being designed specifically for the DARPA challenge, unlike some other challengers, which are building upon existing robot designs. “Challenges typically go after a very hard problem, but have a pretty fast-paced schedule. It forces one to take a big bite out of the problem—but not so big that it can’t be done.”
Meet the Contestants

CHIMP: CMU-NREC’s CHIMP depends on four rubber tracks in each of its limbs for locomotion, which affords it much better stability and dexterity when crossing rough terrain or navigating obstacles, Stentz observes.
“Instead of walking over debris, it can drop down onto all fours and drive over it like a tank,” he explains. “It’s a human form, but without the complexity of control required for a human-like robot.”
Specially designed drive joints on all four of CHIMP’s limbs support human-like grasping motions, allowing the robot to complete the DRC tasks like operating tools or turning valves, Stentz says. There are also on-board sensors that create a texture-mapped, 3D model of the environment, helping CHIMP maintain stability and avoid collision—while also allowing a human operator to visualize the robot’s orientation to aid in control.
“We’ve figured out what the robot must do automatically without human involvement,” Stentz says, explaining that CHIMP is designed with static stability in mind. “CHIMP can automatically detect if it’s likely to tip, and it will stop before a collision occurs so it doesn’t end up damaged.”
THOR: The Tactical Hazardous Operations Robot (THOR) is the Virginia Tech Robotics and Mechanisms Laboratory’s entry into the competition. It’s designed to look more like a human. The robot, which is based upon prior work, including VT’s SAFFiR robotics effort for the U.S. Navy, is battery-powered and employs high-end cameras for vision. It can operate without a control tether, according to Derek Lahr, a Ph.D. candidate in the university’s mechanical engineering program and a member of the THOR team, which is headed by Dennis Hong, Ph.D., an associate professor of mechanical engineering at Virginia Tech’s College of Engineering.

Not only does the Virginia Tech team see opportunity in creating a robot that can aid humanity, it views the DARPA program as a way to push robotics further into mainstream uses like in hospitals and manufacturing settings, Lahr says.
“What makes this unique is creating a robot to operate in environments that are designed for humans,” he explains. “The key is making the robot strong enough so it can operate without human intervention in a very challenging environment.”
The fact that DARPA is controlling the amount of bandwidth available for communication during the various events in the challenge presents a significant control problem, Lahr says, but there are also considerable obstacles in designing the mechanics and software.
“There is no easy task in this challenge,” he admits. The VT team is using Siemens PLM Software’s NX 8 and the Gazebo robotics simulation software as part of its development toolkit for creating THOR.
One key design point for THOR is its flexibility and high range of motion. “A lot of robots these days have smaller ranges of motion than humans because of limits on the mechanical design and the actuators,” Lahr explains. “We’ve been able to get a large range of motion while maintaining a lot of strength.”
At press time, THOR’s CAD model is about 90% complete. Lahr says the team has begun fabrication and aims to complete the physical prototype in August.
Hubo: Drexel University, which is part of a 10-school collaboration, claims to have a leg up on competitors because it is one of only two teams that is actually starting with a working robot, not a design concept. Hubo, which threw out the opening pitch at a Philadelphia Phillies baseball game last year, is a mature and tested design, according to Paul Oh, Ph.D., leader of the DRC Hubo team and a full professor in Drexel’s mechanical engineering department. With its hardware design formalized, the Drexel team is turning its attention to coupling its software with the hardware, using its own open source simulator and models to program Hubo.
“We have seven robots ready to go, which enables us to immediately begin programming, adapting and perfecting,” Oh says. Drexel’s partners in the DRC include Columbia University, Georgia Institute of Technology, Purdue University and the Korean Advanced Institute of Science and Technology (KAIST), which is a leader in electro-mechanical design.
Currently, Hubo has the form and function of a 10-year-old boy. The team is working to transform that design into something akin to a 19-year-old rescue worker. Says Oh: “We want to make it taller, give it stronger motors, and do the same thing with the hands so it can climb ladders and operate heavy tools.”

R2: NASA Johnson Space Center is developing a next-generation humanoid robot and control paradigm capable of performing dynamic, dexterous, and perception-intensive tasks in a variety of scenarios. The DARPA contender is based on NASA JSC’s prior work on Robonaut, which performed on the International Space Station in 2012.
Guardian: The inspiration for this self-powered, lightweight humanoid robot, to be developed by Raytheon, is based on the team’s experience with human-scale exoskeletons. The Guardian robot will expand Raytheon’s Exoskeleton (XOS) concept with new technologies in the areas of large range of motion, high specific torque/power actuators, and a rapidly modulated fluid supply for overall power efficiency.
Schaft: SCHAFT’s proposal is a bipedal robot based on mature hardware and software designed for its existing HRP-2 robot. SCHAFT will create an Intelligent Robot Kernel that will combine the necessary software modules for recognition, planning, motion generation, motion control, and a user interface.
RoboSimian: Of all the competing robots, the NASA/Jet Propulsion Lab entry into the DARPA challenge takes a different approach, eschewing a traditional humanoid design for a simian-inspired limbed robot. Called RoboSimian, the robot has four general-purpose limbs and hands, all capable of mobility and manipulation.
“One of the things that seems true from an engineering standpoint is there is no inherent proof that a more humanoid shape is better at getting tasks done than a less-humanoid shape,” notes Brett Kennedy, supervisor of the Robotic Vehicles and Manipulators Group at JPL.

While RoboSimian is apelike (like an orangutan, Kennedy clarifies), it has no head. Instead, it employs a camera system ringed around the robot to get visibility. It also has no preference for a bipedal form of mobility: The NASA/JPL design emphasizes stability over dynamics and deliberation over reaction.
“Our robot is patient; there is no penalty for it to stop and think about things before it reacts,” Kennedy points out. The four limbs, none specified as arms or legs, are arranged in a symmetrical fashion, so there is no front and no back to RoboSimian. It’s a design point that grew out of the lab’s orbital mobility work, Kennedy says, and one that gives the robot efficiency and minimizes risk.
RoboSimian’s design is also all about pushing robotics into the mainstream, so the team has opted to use no exotic materials. They’re emphasizing low-cost manufacturability and maintenance.
“We’re allowing ourselves to have lower performance componentry with the idea that this is something we can put in the field at the lowest cost as soon as possible,” Kennedy concludes.
More Information
Subscribe to our FREE magazine,
FREE email newsletters or both!Latest News
About the Author

Beth Stackpole is a contributing editor to Digital Engineering. Send e-mail about this article to [email protected].
Follow DE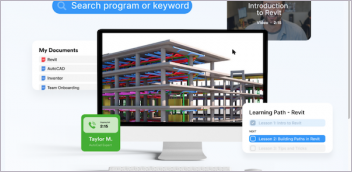

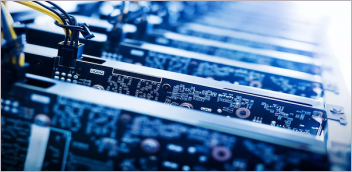
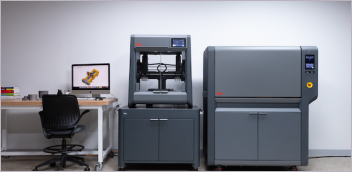