RIZE Inc. Introduces XRIZE Desktop Industrial Additive Manufacturing Solution
The new desktop industrial additive manufacturing solution from Rize is made for creating vibrant, full-color functional parts with minimal post-processing.

XRIZE enables users to manufacture functional polymer and composite parts in full color. Image courtesy of RIZE.
November 12, 2018
RIZE, a Boston, MA-based, additive manufacturing company, has announced new hardware, materials and IoT functionality: XRIZE, a color desktop industrial 3D printer, RIZIUM CARBON and RIZIUM ENDURA materials and the RIZE CONNECT cloud platform.
XRIZE enables users to manufacture functional polymer and composite parts in full color.
XRIZE is easy to use, safe and enables markup to provide much-desired IP security, traceability and branding.
Using the XRIZE 3D printer is as easy and safe as an office 2D printer. Providing a safe, clean process, minimal pre- and post-processing and minimal material management, users throughout the enterprise, from engineering to marketing to the manufacturing floor, can use XRIZE to easily manufacture full-color prototypes for FEA and stress analysis, tooling with safety instructions, consumer products, package design, GIS mapping, anatomical parts for patient/clinician communication, pre-surgical planning and parts for marketing and the entertainment industry.
“One of the interesting applications in the traditional design and engineering world is the ability to do full-color prototypes using FEA and stress analysis, showing a stressed part, and that’s one of the parts that we’re going to display at FORMNEXT,” says Andy Kalambi, RIZE president and CEO. “So you see the part not just in terms of its form and fit but also in terms of its functional characteristics with respect to stress and FEA.
XRIZE leverages RIZE’s Augmented Deposition process by extruding an engineering-grade thermoplastic and simultaneously jetting C, M, Y, K (cyan, magenta, yellow and black) inks through industrial printheads to achieve the full-color part. RELEASE INK is jetted between the part and the automatically-generated supports to enable the user to quickly peel the supports away from the part, leaving a smooth surface finish and eliminating the need for additional finishing. With RIZE ONETOUCH software, users can quickly and easily apply text, images and texture maps to monochrome part files and import color CAD files.
Key Features:
- Full, CMYK color 3D printing with best-in-class Z-strength
“CMYK has not been done before in this industry for full-functional parts,” Kalambi says. “It’s been in very high-end machines, in a different kind of process. First of all, getting the color palette was big—we’ve been working almost two years on this.
“Color is an evolution process but we wanted to ensure that we release the machine only when we feel the colors are really consistent. We’ve come up with a color palette that will address most needs and get most of the more difficult colors,” he adds.
- Runs multiple materials: RIZIUM ONE, RIZIUM BLACK and the new RIZIUM CARBON and RIZIUM ENDURA materials
- Minimal pre- and post-processing provide the fastest time to part
- Easy to operate with an auto-leveling build plate, automatic filament changeover and intuitive high-resolution touch screen for access to part library, build management and system diagnostics
- Heated build chamber for industrial part strength and accuracy
- Safe process and materials for office compatibility
- Secure; internet/cloud connectivity optional
Key Specifications:
- Four-channel color and dedicated Release Ink channel
- Device dimensions: 21.4” H x 36” W x 25.4” D (535 x 915 x 647mm)
- Build volume: 12”x 8” x 8” (310 x 200 x 200mm)
- Weight: 135 lbs (61kg)
- Layer thickness: .250mm or .125mm
- Resolution: x/y 300dpi; Z 200dpi at .125mm layer thickness
- Accuracy: X/Y: +/- 0.127mm, or +/- 0.003mm/mm, whichever is greater and Z: +/- layer thickness (0.250 mm or 0.125 mm)
With an MSRP of $55K USD, XRIZE will be available in 2019.
RIZIUM Carbon Material
RIZIUM Carbon is an engineering-grade thermoplastic filament reinforced with carbon fiber for a superior visual finish and higher modulus. RIZIUM Carbon is ideal for applications such as functional prototyping for manufacturing.
“This is a carbon-fiber-infused material [that is] very strong and suitable for applications in jigs, tools, fixtures, all high-strength-related applications; it has a beautiful finish; same as with RIZE ONE, you can drill it, sand it, tap it,” says Kalambi.
RIZIUM Endura Material
RIZIUM Endura is a fiber-reinforced filament providing high-accuracy and high-impact strength. It is ideal for large functional parts and is compatible with RIZE’s full-color inks.
“The ENDURA material will be available for both machines (RIZE One and XRIZE); our intent is to keep the two machines using the same systems as much as possible; we want a platform approach where people can have one machine and try out different materials depending on what their use cases are,” says Kalambi.
RIZE Connect
RIZE Connect enables users to remotely manage and monitor their RIZE One and XRIZE 3D printers from any location to improve production efficiency. Users can receive notifications, queue jobs and manage an enterprise print farm from desktop and mobile devices. Using RIZE Connect, users can also build greater security into their parts with digital part identification and other forms of part augmentation, such as QR codes and version control for part traceability, compliance and authenticity. RIZE Connect will be available in 2019.
“Our mission from the beginning has been inclusive and sustainable innovation,” says Kalambi. “With this approach, we can take additive manufacturing anywhere and to everyone. The way to do that is to make industrial 3D printing easy, safe and fully digital. Our innovative platform approach is the core to driving sustainable innovation. With the launch of XRIZE, RIZIUM Carbon, RIZIUM Endura and RIZE Connect, we are now realizing the potential of this platform, providing our customers with maximum flexibility, complete ease of use and quickest ROI.”
RIZE is demonstrating its comprehensive suite of new and existing products Nov. 13-16 at Formnext in booth 3.1/C28.
Foreseeing how RIZE's product offerings will be used, Kalambi says, “One interesting application we see coming up is engineers using color parts for communicating with different stakeholders in the enterprise. For example, the design engineers are very familiar with CAD tools and simulation tools, but if you want to send a part to a supplier or to a manufacturing engineer, and work on things like tolerancing, getting agreement on what should be the right final fit and tolerance on a part, that’s a cumbersome process. And we believe that the haptic experience that a physical part provides gives the ability for more people to come on the same page and make decisions quickly.”
Sources: Press materials received from the company.
More Info
Subscribe to our FREE magazine,
FREE email newsletters or both!About the Author

DE’s editors contribute news and new product announcements to Digital Engineering.
Press releases may be sent to them via [email protected].
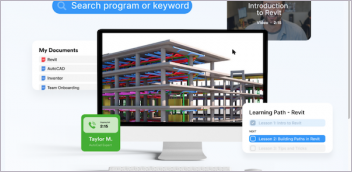

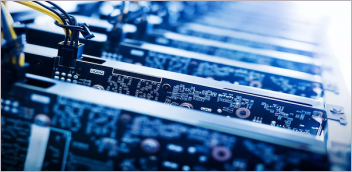
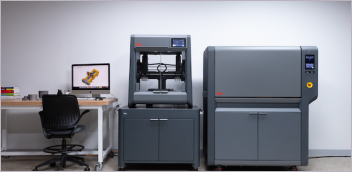