Latest News
July 1, 2013
![]() Terry Stonehocker regularly relies on GradCAD to retrieve models of standard parts to jumpstart designs for his custom motorcycle business, including this design done in collaboration with fellow GradCAD member Gary Downer. Image courtesy of Terry Stonehocker. |
While the idea of 3D model reuse has always been of great interest, most engineering teams have attacked the practice on more of an ad hoc basis, not going far enough in prioritizing and facilitating an effort by putting the right tools and formal processes in place. Yet with product development cycles getting shorter and with engineering resources still tight, companies are doing all they can to make design practices more productive. This mindset has drawn attention to the importance of a well-conceived reuse strategy and ignited exploration into how to best repurpose existing 3D CAD models.
“The typical cost, time and quality pressures are driving interest in reuse,” notes Tom Gill, an independent consultant specializing in product lifecycle management (PLM). “Designing a new part, releasing it into production and ensuring it’s fully validated is a huge process in any company. If you can reuse something that’s already proven, you can save an enormous amount of time and reduce cost.”
Experts says a CAD model reuse strategy makes the most sense for standard parts, whether that’s for commodity supplier offerings or internally developed components that are used repeatedly across multiple product lines and different engineering groups.
“Companies want their engineers spending time creating the next great thing or focused on getting to market faster; they don’t want them wasting time searching for standard parts or supplier parts, because it doesn’t add any value to the company,” explains Tim Thomas, CEO of CADENAS PARTsolutions, which provides technology for creating centralized 3D standard parts catalogs.
![]() PTC Creo Advanced Framework Extension, tailored for machine designers and equipment manufacturers, is an intelligent library and set of automated drawing capabilities that enable structural framework design productivity improvements of up to 10 times when compared to standard design techniques. Image courtesy of PTC. |
The continuing trend around mass customization also underscores the importance of a well-functioning CAD model reuse strategy. Whether a manufacturer is designing a new tractor or household appliance, engineering teams are moving toward designing products as more of a modular concept. The goal is to take existing designs and adapt them only moderately to new use cases, according to Bob Noftle, chief evangelist for TraceParts, a provider of parts catalog technology serving up over 100 million 3D CAD models and 2D drawings.
“Companies are aiming to start with existing data whenever they can, and only ]model] a small percentage of the design from scratch,” he notes.
A Bevy of Options
In addition to the online 3D parts catalog services from companies like CADENAS PARTsolutions and TraceParts, there are a number of options to help engineers and designers jumpstart CAD model reuse. Most modern CAD tools offer fairly extensive capabilities for creating libraries of 3D models for subsequent reuse, although this approach is best suited for helping an individual take advantage of past work, not necessarily for promoting model reuse across a department or a global engineering organization. Product data management (PDM) and PLM platforms take the reuse value proposition further by providing repositories and search capabilities for storing 3D CAD models, but experts say that even those platforms have limitations in terms of usability and search capability.
“Even with PLM implemented, you hear those stories of the large automotive or airplane manufacturer who maintains a model of the same bracket designed 42 different ways,” Gill says. “Still, it’s much easier to query and manipulate the ]CAD models] if you have PLM vs. having data strewn all about the company, making it difficult to find something similar that will work.”
To address some of the shortcomings, PLM and CAD vendors are evolving these platforms with new meta data and geometric search capabilities aimed at making it easier to quickly find similar parts models, Gill says.
The combination of enhanced search capabilities and tight integration between the PLM platform and online parts catalogs like those sold by CADENAS PARTsolutions is one of the ways PTC is coming at the problem, according to Brian Thompson, the company’s vice president of product management. In addition to Advanced Framework Extension for Creo, which lets users bring a variety of standard component models into their designs, PTC is partnering with CADENAS PARTsolutions on a portal that supports a streamlined workflow for incorporating Creo models of more complex off-the-shelf components into designs, Thompson says.
By leveraging CADENAS PARTsolutions’ expertise in delivering geometrically accurate models, Creo users no longer have to spend time approximating the design of a commercially available off-the-shelf product. “They don’t have to do any work to validate the geometry, and it’s delivered right into their native CAD environment,” Thompson explains. “This can really streamline the design process.”
In fact, having a vendor-certified (and oftentimes, vendor-supplied) 3D CAD model is one of the primary advantages touted by online parts catalog suppliers like CADENAS PARTsolutions and TraceParts. Engineers downloading parts from these platforms should expect error-free models—unlike some of the newer community sites, where users are invited to freely upload and share 3D CAD models in the spirit of open source development, contends TraceParts’ Noftle.
“You’re at the mercy of the crowd, so you have to rely on what information is available to them at the time they’re creating the model,” he says. “They don’t have the benefit of a contract with the supplier.”
Mark Ortiz, vice president of engineering at Littleford Day, will attest to how the integration of the CADENAS 3D parts catalog is helping the processing equipment manufacturer wrest control over its design processes. The make-to-order shop was struggling to give engineering teams visibility into a burgeoning library of Siemens’ SolidEdge CAD models—a result of slightly custom designs. Moreover, if there was a mistake in a design that was subsequently fixed on the shop floor, it wasn’t always reflected in the latest CAD model, which could led to repetition of the same mistake.
“Because we had no control over this cloud of 60,000 CAD models, we had no idea what was good or bad, and the spare parts group who did the ordering didn’t know whether a part was in stock,” Ortiz says. “If you don’t have control, you can’t go forward.”
Now a year into its CAD reuse overhaul, Littleford Day is using CADENAS PARTsolutions’ platform to create and maintain a master catalog of 3D models for its standard parts—both internally developed and from suppliers. “It is critical for business efficiency and repeatability to have control over these CAD libraries,” Ortiz says.
At Kimball International, the CAD reuse value proposition is really more about repurposing older designs as a starting point for new models in its office furniture line. “We have a lot of new products, but many of the components are very similar,” explains Ricardo Espinosa, R&D engineering manager for the firm. “Instead of creating a 3D model from scratch, we want to call up existing components, make modifications, and create a new revision of an existing product without having to spend days or hours.”
To do so, Kimball is taking advantage of the Synchronous Technology capabilities in its SolidEdge CAD platform to modify 3D CAD models from its legacy I-DEAS CAD tool without having to deal with the complications of a history tree.
CAD Reuse in a Crowd
While 3D models of standard supplier parts are important to an overall CAD reuse strategy, there are additional use cases for redeploying CAD models. That’s where community sites like GrabCAD come into play. Say, for example, a designer is creating a bike headlamp and wants to showcase its offering to potential customers or suppliers, but doesn’t want to recreate the entire bike model, explains Sara Sigel, community manager at GrabCAD, which has more than 200,000 CAD models created by more than 600,000 members.
“Engineers don’t want to spend time recreating the other things that are part of the equation,” she says. “They want to set the scene and have all the parts they need to create the bigger picture.”
Sigel admits that engineers need to be diligent about checking a model for accuracy and to ensure it’s what they want. Depending on how they plan to use the model, there might also be a requirement to get signoff on intellectual property from the original model creator.
![]() Kimball International created a new metal drawer by reusing existing imported data from its old I-DEAS CAD system. Using synchronous technology in SolidEdge, the task took just minutes. Image courtesy of Kimball International. |
Despite any potential extra legwork, however, engineers like Simon Rafferty and Terry Stonehocker see huge benefits in leveraging the GrabCAD community to get a starting point for designs. Stonehocker, a mechanical engineer with a custom motorcycle design business, regularly leverages GrabCAD for models of electrical motors. “Most of the time, I can’t find exactly what I want, but I find something close and I can modify it quicker than starting from scratch,” he explains. “If you can find something that will save you time, that’s very important.”
Rafferty, managing director at X-Eng, which makes third-party parts for Land Rover vehicles, has used GrabCAD to download a variety of models. “Even if I have to do some rework, some things are just time-consuming to draw, especially if I don’t need them to be accurate,” he explains. “Less duplication of effort moves us forward faster, and is invaluable to making the design process easier.”
Beth Stackpole is a contributing editor to DE. You can reach her at [email protected].
More info
Subscribe to our FREE magazine,
FREE email newsletters or both!Latest News
About the Author

Beth Stackpole is a contributing editor to Digital Engineering. Send e-mail about this article to [email protected].
Follow DE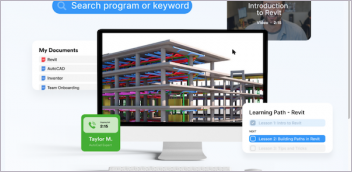

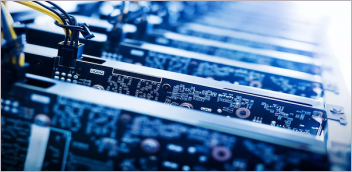
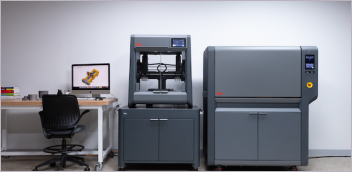