Latest News
December 1, 2004
By Sandeep Sovani
Figure 1: The imported surface model of the vehicle’s outer shape showing thewindow of interest for the wind buffeting simulation. |
Advanced simulation software is providing automotive engineers with a powerfulnew tool to reduce wind buffeting, the noise and pulsating forces that accompanydriving with windows open. While the frequency of the sound of the buffeting isoften below the range that can be heard by human ears, it can still be felt asa pulsating wind force, a phenomenon that can be very fatiguing.
It’s ironic that wind buffeting has become a significant factor in the overallpassenger experience in recent years precisely because engineers have been sosuccessful in reducing noise from other sources. Until recently, the difficultyin addressing this issue was that engineers had to build a particular design inorder to measure how it performed in wind buffeting tests, and these measurementsprovided little or no information to help improve the design. These days, however,automotive engineers are beginning to accurately simulate wind buffeting usingoff-the-shelf CFD (computational fluid dynamics) software.
Accurate simulation makes it possible to quickly evaluate the impact of variousdesign changes without the time and cost involved in building a prototype. Italso makes it possible to view important performance parameters such as pressureand flow velocity at any point in the vehicle and its surrounding air stream,providing an intuitive understanding that leads to better designs. In simulationsof a number of different designs under different conditions, results were foundto closely match actual measurements of prototypes. DaimlerChrysler plans to beginusing these methods on a regular basis both to help improve specific designs andto develop general guidelines for reducing wind buffeting in the near future.
Figure 2: A close-up showing the exterior and interior mesh refinements intendedto capture the wake behind the vehicle and wave propagation inside the passengercabin. |
Wind Buffeting
An unstable shear layer that is established at the forward edge of a window openingcauses wind buffeting. These disturbances (swirling wind or currents of differentspeeds and directions) travel along the side of the vehicle and, when they reachthe rear edge of the window opening, generate a pressure wave that propagatesboth inside and outside the passenger compartment. Outside the vehicle, this wavemoves both forward and backward along the side of the car. When the forward-travelingwave reaches the front edge of the opening, it triggers another disturbance thatmoves back to the rear edge. This process is repeated many times a second andcauses the shear layer to develop a characteristic buffeting frequency, whichdepends on the vehicle speed and the geometry of the opening.
The results of wind buffeting are easy to measure with microphones, but the complicatedpressure waves that cause it are very difficult to measure. In the past this meantthat engineers had to wait until relatively late in the design process and useprototypes to measure the phenomenon. And the measurements typically gave themlittle or no information to determine what areas of the design were affectingwind buffeting or how to reduce it. The only option was to modify and test prototypes.This trial-and-error process has become too costly and time-consuming to justify,especially when it remains difficult to identify changes that will improve design.
In recent years, dramatic reductions in structure-borne and airborne noise inthe passenger compartment have made wind buffeting more noticeable to driversand passengers. At the same time, the performance of simulation tools has advancedto a point where robust CFD solvers with accurate turbulence models, and computerswith the speed and memory to perform the complex computations required to simulatethis phenomenon, have become available. A CFD simulation provides fluid velocity,pressure, temperature, and other variables throughout the solution domain forproblems with complex geo- metries and boundary conditions. As part of the analysis,an engineer can change the geometry or the boundary conditions of the system,and observe the effect of the changes on fluid flow patterns or distributionsof other variables. CFD also can provide detailed parametric studies that significantlyreduce the experimentation necessary to develop new or modified equipment.
Figure 3: Pressure contours showing the wakes behind the A-pillar and side mirror. |
Simulating Wind Buffeting
For these reasons, DaimlerChrysler has a major effort underway to accuratelysimulate wind buffeting. Engineers selected Fluent CFD software from Fluent Inc.of Lebanon, New Hampshire, because of results they’ve had with it in simulatingother areas of vehicle design. Fluent also offers a range of turbulence models,which are relevant because of the important role played by turbulence in windbuffeting.
In a DaimlerChrysler study conducted in 2003 (On Simulating Passenger Car WindowBuffeting, SAE Paper No. 2003-01-1316), D. Hendriana, S.D. Sovani, and M.K. Scheimanndeveloped a model by importing a surface model of the outer shape of a vehicleand a CAD model of its interior into the ICEM CFD pre-processor. The simulationdomain was defined to include the entire passenger cabin, which is connected tothe external flow domain through the open window. Dummies representing the passengerswere included in the model to correctly represent the volume of the passengercompartment when occupied. The vehicle surface was modeled with attention to detailto capture flow development from the front end to the window opening (see Figure1, above).
Several levels of local mesh refinement were used. Two were applied outside thevehicle to capture the wake behind the vehicle; one was applied inside the passengercompartment to capture wave propagation inside the cabin. The finest refinementlevel was applied at the area of the opening to capture the shear layer. Modelswere developed for the case where the left side front window was open and allother windows were closed (see Figure 2, above) and for the case where the leftside rear window was fully open and all other windows were closed. These buffetingsimulations were also applied to noise levels for an SUV (SAE Paper No. 2004-01-023).
test results
The DaimlerChrysler engineers modeled the turbulent flow using the RNG k-e andLES turbulence models, both of which have been shown in the past to provide goodresults for a range of turbulent conditions. Interior surfaces of the vehiclemodel were assumed to be solid walls instead of soft surfaces such as carpetingor fabric. (Actual car surfaces are less reflective and more absorbent than solidwalls, giving the model a tendency to overpredict the wind-buffeting phenomenon.)A steady-state solution was first obtained for each case. The continuity and momentumequations were then converged until the residuals dropped more than three ordersof magnitude.
These results were then used as initial conditions for a subsequent series oftransient simulations that were used to capture the pressure fluctuations in thevicinity of the open windows. VI (virtual instrumentation) monitors were set upat the driver’s and co-driver’s ear locations and static pressure was recordedat these locations at every time step. The initial transients died down and thepressure traces reached a dynamically steady solution in roughly 300 to 500 timesteps (or from 0.60 to 1 second). Subsequently, pressure traces were recordedfor time periods between 1.0 and 2.0 seconds to obtain a sound pressure spectrum.The pressure signals were then converted to the sound frequency spectrum by takinga discrete Fourier transform using a Hanning window filter. The sound pressurelevel (SPL) was finally converted to dB units.
Figure 4: Pressure contours around the front window area illustrate a wave generatedat the B-pillar. |
Simulation Provides Diagnostic Information
The CFD predictions were validated by comparing them to measurements taken ina wind tunnel. Not only did the CFD simulations accurately predict buffeting frequencyand sound pressure levels, but the predictions also accurately matched SPL andfrequency variations observed in physical experiments.
The key advantage of simulation is that CFD provides far more diagnostic informationthan can be obtained from physical testing. For example, to investigate air pressurearound the critical front window area, engineers generated charts that displayedair pressure on the opening with filled contours, while line contours were usedto display air pressure on a plane parallel to the opening. A vertical stripeof low pressure followed by a high-pressure stripe was observed in the openingplane. The stripes indicated that a vertical vortex occurs behind the A-pillartheframe structure separating the windshield and the window (see Figure 3, above).
Animation of the transient solution clearly showed vortex movement with the localflow that impinges on the B-pillarthe frame between the front and rear windows.The wave generated at the B-pillar was also shown as it moved toward the passengercompartment (see Figure 4, above). Being able to visualize the formation of thepressure waves and detailed measurements of velocity and pressure at any pointin simulations such as these has the potential to help engineers understand exactlyhow wind buffeting is occurring in a particular design and quickly develop a solution.
These correlations give engineers confidence to use CFD results to investigatea much greater number of possible design alternatives than would be possible withphysical testing. The simulations showed that both the RNG k-e and LES turbulencemodels provide accurate results. The simulations correlated well with experimentalmeasurements by showing that as the vehicle speed is reduced from 60 mph to 50mph, the buffeting SPL and frequency go down 1dB and 1Hz respectively for thefront-window-open case and by 5dB and 1Hz for the rear-window-open case. The frequencyspectra and sound pressure level were very similar for all locations studied withinthe vehicle. An exhauster connecting the passenger compartment to the outsideatmosphere via a port was also evaluated and shown to have an insignificant impacton buffeting. Simulations with the left front window wide open and the right rearwindow open just 1 inch were also performed. These showed that buffeting was substantiallyreduced. Simulations with a modified side mirror design reduced buffeting by 13dB,which correlated well with experimental measurements.
DaimlerChrysler engineers are making use of these results by simulating othervehicles, evaluating the influence of more parameters, and evaluating differentmodeling techniques. As simulation is more fully integrated into the design process,this approach should make it possible to substantially reduce wind buffeting.
Sandeep Sovani, Ph.D., is a CFD engineer with the Automotive Industry Team of Fluent Inc. specializingin automotive aeroacoustics and aerodynamics. You can contact him about this articlevia e-mail sent to [email protected].
Product Information
Fluent, Inc.
Lebanon, NH
fluent.com
Subscribe to our FREE magazine,
FREE email newsletters or both!Latest News
About the Author

DE’s editors contribute news and new product announcements to Digital Engineering.
Press releases may be sent to them via [email protected].
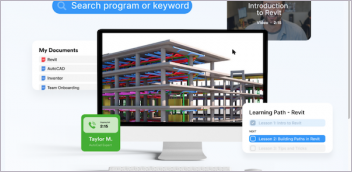

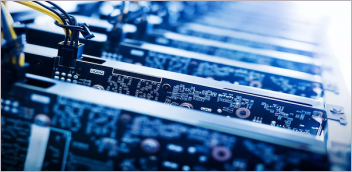
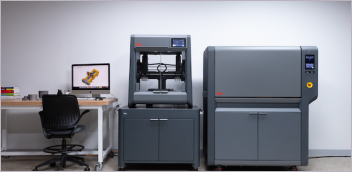