Reconfiguring Human Bones
Using reverse engineering and desktop RP&M, biomedical applications come alive.
Latest News
January 13, 2008
By Margaret S. Gurney
![]() The human hand has 27 bones that have been scanned,modeled, and reproduced by Dr.RichardSiderits using a Roland MDX15 CNC milling machine for various biomedical applications. |
Dr. Richard Siderits, head of the Robert Wood Johnson University Hospital’s experimental pathology division and an assistant professor at its medical school in Piscataway, NJ, is making a real difference in medical applications of rapid prototyping and manufacturing (RP&M) technology. After finding that other approaches to RP&M were either too slow, not accurate enough, or too expensive, he configured his own desktop RP&M laboratory using off-the-shelf hardware and software.
Siderits’ entire system fits on his desktop, cost him less than $8,000, and it creates accurate solid models and part molds (within 0.002 in. accuracy) from start to finish often in less than one hour. Accuracy is critical in Siderits’ projects, one of which is creating a set of openly available 3D files of human hand bones so researchers can develop more realistic robotic hand systems or use them for replacing destroyed bones in trauma patients.
Siderits was initially interested in growing artificial, or virtual, nervous systems to move robot hands in the real world. And what better mechanics to begin with than the multiplicity of the biological movements of the human hand? Yet Siderits’ research turned up not a clue of openly available 3D files of the 27 skeletal bones of the human hand. He would have to create the files himself.
![]() From left to right: 1) Modified bone with fixation “rides” (ridges) added with trueSpace (laser-scannedfinger bone). 2) Artificial joint for robotic hand (laser-scanned clay model). 3) Portion of prototype forsurgical instrument handle (laser-scanned clay model). 4) Prototype of a small specimen tweezer forproduction on Pinnacle-V laser cutter. 5) Gum from crime scene forensics for virtual model of toothimpression and additional models that will not deform in an evidence locker or if the original is destroyedfor DNA testing (laser scanned). |
The X-RP Process
To make either a robotic or prosthetic hand that ultimately had a similar range of motion as a real hand, Siderits obtained a skeletal hand and, using a NextEngine Desktop 3D Scanner, had an exportable 3D file of each bone in the human hand in 90 seconds.
He then “modded” (modified) a bone from each scan; using trueSpace from Caligari Corp., he created a DXF model that could be modified or reverse engineered as needed to add attachment points to the bone, similar to a bump or a post with a hole in it, through which superelastic Nitinol “muscle wires” would be attached. Siderits says trueSpace works well for him because of the flexibility he needs for both his medical research and X-RP ]Extreme Prototyping] needs.
He then created a physical model of the bones using a Roland MDX15 CNC milling machine and an attachment on a magnetic base from Fourth Axis to convert the x-y-z CNC milling to x-Rotational-z milling, which permits milling of a 360-degree object like a chess piece for example; the magnetic base allows a fast swap of milling blanks. Siderits then used DeskProto from Spline Systems to create the CAM code necessary.
![]() The Roland MDX15 includes an attachment on a magnetic base fromFourth Axis to convert the x-y-z CNC milling to x-Rotational-z milling, whichpermits milling of a 360-degree object and fast swaps of milling blanks.Siderits used DeskProto from Spline Systems to create the CAM code. |
Robotic Applications
“To create and modify in such a broad range of bioengineering functions is pure joy,” says Siderits, whose applications in the medical and forensics fields using RP&M technology were profiled on deskeng.com last October (see “Do-It-Yourself Desktop Modeling” deskeng.com/articles/aaafpb.htm).
Take, for example, a person who has just been admitted to the emergency room with a crushed finger. Using Siderits’ method, the same finger on the opposite hand is as good a model as any on which to base a surgical replacement part for the repair. MRI (CT scans) images scan within 1mm accuracy. Slicer Dicer from Pixotec, can view and analyze the scan as a 3D model, says Siderits, and trueSpace from Caligari Corp. can alter it to include anchor points for surgically attaching the ligaments, muscles, and tendons.
![]() This image shows a “modded”(modified) human hand bone with theattachment point. It was scanned, brought into trueSpace, and modeledto add an attachment point before heading to the Roland MDX15 witha Fourth Axis attachment. |
In the robotic or prosthetic application, these points would be attached by muscle wires. When an electrical current is introduced to Nitinol, the wire shortens just like a human muscle does when it contracts. When the current is removed, it relaxes back to its original length. The changing current can cause manufactured “bones” to behave as if they had muscles.
Once the scan was complete, the trueSpace 3D files were sent to a desktop CNC milling machine. Siderits suggests deposition or “additive” modeling might work just as well. He adds that a CNC milling machine, like the Roland MDX 15, is as small as a desktop printer and is relatively fast when working in softer materials.
With the project complete, Siderits offered his files as a resource through the PittsburghSupercomputing Center as an open resource for robotics engineers, telesurgical prototyping, and other medical research applications.
![]() This image shows fast 3D volume reconstruction of bone and soft tissue (not shown) with subvolumeextraction (less than two minutes on a standard PC).Volumes or sub-volumes can be saved as DXF forfast prototyping of lesions, defects, and masses. |
But this technology need not end here. Siderits explains that the same life-size model of a hand can be scaled up to ten feet, for example, and used with hydraulics to crush an automobile at a scrap yard; likewise the life-size model of the hand can be miniaturized to someday crawl inside a wound, administering such tasks as removing dead cells and applying medicine as needed. He refers to this as a modular active woundcare pod or MAWP.
Virtual Healing
“While using a laser cutter-engraver for materials like foam, wax, polymers, and plastics can be fun,” says Siderits, “laser scanning of biological subjects can take medicine to a whole new level.”
From Bones to Neural Networks According to Dr. Richard Siderits, the beauty of biomedical applications for RP&M and reverse engineering is endless. Ultimately, however, he is interested in creating a virtual nervous system and got started using an object-oriented computer language called Python to create objects in the program with specific attributes and behaviors. For example, a parabiotic neural unit, or an artificial neuron, can be created. Because Python is multithreaded, it can run many “threads” of programming at the same time, saving computing power and executing processes independently. In Siderits’ model, this virtual neuron can generate as many threads as it needs. Just like a real neuron in the brain, the threads act like dendrites and axons. When the threads (dendrites) pick up enough information from remote sensors or from each other, the nerve fires, and the message that the nerve has fired goes down the axon (another thread). On a large scale, Siderits calls this a Parabiotic Neural Construct. Just like real nerves, the dendrite threads can survive or die based on their experience. In other words, one can create a simple brain that grows and learns how to control a robotic hand from its own experience. The name of the parent project is GOLEM (Generationally Organized Latent Evolutional Matrix). In theory, the Parabiotic Neural Construct could control hand movements based on this learned experience (heuristics), Siderits explains. It can tell the Parabiotic brain to save information to files so that it can refer to experience; this approach would approximate a model known as an Adaptive Resonance Matrix. “You then would have this brain-like thing that learns from its experience,” explains Siderits. “Sadly, just like a real brain, it is the interaction between the components that not only defines the structural relationships but also the function, so turn it off and it dies.” —MG |
According to Siderits, the applications for this type of RP&M process are virtually limitless for anyone dependent upon scanning, modifying, and creating physical molds or accurate models.
This RP&M process could enhance the work of forensic scientists, archeologists, medical researchers, plastic surgeons, and even home-medical hobbyists. But regardless of the myriad applications unfolding, as engineering continues to slip into the medical field, the bridge between the two gets shorter.
More Info:
Center for Parabiotics
Newtown,PA
parabiotics.org
DeskProto
Delft Spline Systems
Utrecht, The Netherlands
spline.nl
Fourth Axis
NSW, Australia
fourth-axis.com
NextEngine
Desktop 3D Scanners
Santa Monica,CA
nextengine.com
Nitinol
Nitinol Devices & Components
nitinol.com
Pittsburgh Supercomputing Center
Pittsburgh,PA
psc.edu
Python Programming Language
Hampton,NH
python.org
RobertWood JohnsonMedical School
Piscataway,NJ
rwjms.umdnj.edu
Roland DGA
MDX15 CNC milling machine
Lake Forest,CA
rolanddga.com
Slicer Dicer
Pixotec, LLC
Renton, WA
slicerdicer.com
trueSpace
Caligari
Mountain View,CA
caligari.com
Margaret S. Gurney is the editor for new products at Desktop Engineering magazine. To remark on this article, send your comments via e-mail to
[email protected].
Subscribe to our FREE magazine,
FREE email newsletters or both!Latest News
About the Author

DE’s editors contribute news and new product announcements to Digital Engineering.
Press releases may be sent to them via [email protected].
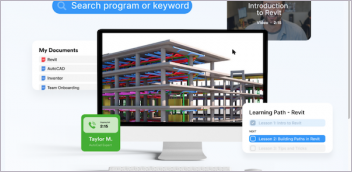

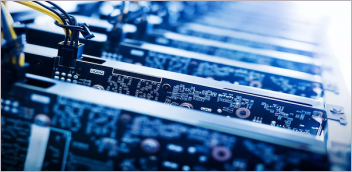
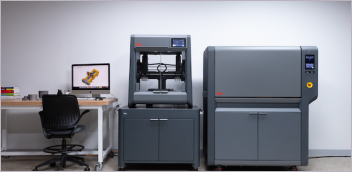