Rapid Rewards Come from System Gains
Part 1: Prototyping becomes more practical as developers fine-tune and increase the efficiency of their systems.
Latest News
May 1, 2008
By Pamela J. Waterman
![]() Mathematical sculpture artist Bathsheba Grossman uses ExOne’s ProMetal 3D printing system to create art in bronze.(Image courtesy ExOne and Bathsheba Grossman) |
Leapfrogging may be the best term to describe the progress seen recently in the tandem components of additive rapid prototyping (RP): machines and materials. Increased precision in layered-manufacturing techniques has opened up new possibilities for material use. Consequently, new materials, with such properties as increased strength, flexibility, and temperature-handling capabilities, have generated more interest in the machines, so system designers keep reaching higher to offer better speed, accuracy, and simplicity.
Users are the ultimate winners in this game, as competition and creativity have opened more avenues for successful applications. In this first part of a two-part series, we zero in on the ease-of-use features and resulting efficiency that are improving the RP experience for both new and seasoned users.
![]() 3D Systems’ ProJet HD 3000 3D Production System offers part-nesting and stacking capabilities to optimize build volume. Shown here are various stacked jewelry pieces and electrical connectors. The wax support keeps each layer separate, and the user can designate howmuch space is between each layer to minimize material usage.(Image courtesy 3D Systems) |
Looking at the Big Picture
How can you measure, and therefore improve, efficiency in the RP world? At ExOne, Vice President Howard Kuhn says that one way is to save energy by offering a new material in the ProMetal process. “We’re now using a lower-temperature alloy infiltrant, which puts you on the threshold of using cheaper furnaces. This ]new bronze material] lets you operate furnaces with carbon electrodes instead of molybdenum ones, which has a huge impact on the cost of a furnace and the electricity for its operation.”
ExOne/ProMetal is also about to market a new all-bronze material, instead of bronze-stainless-steel, that offers more end-use flexibility.
Jon Cobb, at Dimension 3D Printing Group, lists several ways Dimension systems operate with improved efficiency for faster throughput. The company’s machines build parts from extruded ABS plastic filaments. “On a typical part,” he says, “the Dimension 1200es performs 20 percent faster than the original 768 machine. It also produces parts that are more durable and with a 57 percent larger build space, or with many more multiple parts.”
![]() This “floating” ball in a 3-in.-diameter cage was formed as a single build on a Desktop Factory system.(Image courtesy Desktop Factory) |
Software Comes On Strong
As part of Dimension 3D’s efficiency improvements, Cobb says its Catalyst EX front-end software now generates a faster STL-to-process sequence. The method includes finding ways to decrease the number of supports required for building some part geometries. Fewer supports means faster postprocessing and greater ease of use for the system operator.
Stratasys, Dimension 3D’s parent company, took on a number of challenges over the past few years with its fused deposition modeling (FDM) systems. To simplify operations, it has improved front-end software so users don’t have to manually tweak build parameters. There’s also better feedback to the operator to help optimize multipart packing, and a new postprocessing technique that enables the operator to create ultra-smooth surfaces in minutes. By contrast, traditional painting can take 30 to 120 minutes.
![]() This prosthetic leg for a limb lost above the knee was created in two separate builds of plastic on EOS laser-sintering equipment.(Image courtesy EOS) |
Regarding efficiency, both the Stratasys FDM 400mc and FDM 900mc systems (average 29 percent faster) have gained better throughput. This speed comes from recent improvements in electromechanical control of the extrusion parameters and the x,y motion control without sacrificing accuracy or repeatability.
Objet Geometries has developed an optimization package for its photopolymer-jetting Eden350V and Eden500V printing systems. Comprising three hardware and software modules, the Optimax package automates resin management and improves resin use. It also reduces the risk of human error in loading and unloading material cartridges, and assures quality on long runs.
According to Adina Shorr, CEO at Objet Geometries, “The Optimax package will enable users to get even more out of their investment ]in the Eden systems], reducing their ongoing operational cost and increasing uptime.” For example, the software’s Image Processing Engine improves the interaction between the printing system and the material, and, using a smart algorithm, creates efficiencies in material consumption up to 15 percent.
The originator of the additive RP industry, 3D Systems markets products based on three different technologies. Its original stereolithography apparatus (SLA) systems build plastic parts from laser-cured liquid resins. The selective laser sintering (SLS) machines produce both metal and plastic parts by laser-sintering powdered materials, and the multijet modeling (MJM) line deposits fine liquid-plastic drops at several levels of feature definition. The company relies heavily on user input for continuous product improvement, especially when it comes to ease of use.
3D Systems offers several interactive customer features for its equipment, including online help and remote diagnostics. It also points to its new proJet HD 3000 as an example of better overall efficiency. 3D Systems says it is the first in its 3D Modeling family to have part nesting and stacking capabilities that optimize build volume as well as software-selectable definition styles to give customers two systems in one.
How Green is Rapid Prototyping? From a long-term perspective, Cathy Lewis, CEO at Desktop Factory, believes that most professionals don’t think about the end-use of their products. For parts produced on her company’s systems, Lewis says they are looking at ways to break down any support structures for easier recycling. Customers can mail unused powder back to the headquarters and get a discount on new material. Desktop Factory is also working to understand such questions as, how many times can unused powder be put back into the machine for reuse? Other RP companies are also thinking green. ZCorp systems can build with a composite zp140 material that is water-curable, and loose monochrome powder is collected for reuse. The Stratasys FDM process generates almost no waste compared to many other additive RP processes and avoids the scrap created by standard machining; a “sparse” fill option for parts also reduces material consumption. 3D Systems’ V-Flash units plug into a standard outlet and work with fully contained material cartridges for office-safe operation. Both Stratasys and its Dimension 3D division accept empty cassettes of ABS plastic via prepaid UPS label. The company then cleans them, inserts a new EPROM, respools the material, and resells the cassette. Users of EOS metal systems can sieve and reuse all of their powders. Jim Fenrick, VP of North American operations, says that EOS plastic materials are also reusable with a certain refresh rate (adding virgin material), but that the company has a third party working on 100 percent reuse. As ExOne’s Howard Kuhn points out, the simple fact that you’re making a prototype has a huge environmental impact because it saves mistakes. He explains, “You usually try out tools and try out castings, but ]with prototyping] you use only the material needed and avoid scrap.” Going digital all the way, he adds, from a 3D CAD design to an analysis of cooling flow to an RP part, represents the digital manufacturing future. Mcor Technologies’ CEO Conor MacCormack notes that selecting an adhesive to join the paper layers also depended on environmental issues. He says, “To avoid the use of solvents and extraction units we decided to use a simple polyvinyl acetate (PVA) or white glue similar to that found in any art shop or school room.” As a result, running water takes care of cleanup and all parts and waste are themselves recyclable in a standard paper recycling bin. In fact, Mcor may have the “greenest” system of all. Not only does the Mcor Matrix system build parts from ordinary office paper, it can even re-use any sheets that were previously run through a standard 2D printer or copy-machine. What a fitting contribution from the Emerald Isle. - PJW |
Hardware Continues to Deliver
EOS, manufacturer of laser sintering systems in Germany, continues to expand its plastics and metal system capabilities through hardware improvements. With a build volume of 29 in. x 17 in. x 22 in., its EOSINT P 700 saves users time and effort by producing larger parts in a single piece. An automated powder-delivery system that provides a consistent material mix also reduces time and cost of labor.
On a smaller scale, the EOS Formiga P 100 produces parts from polyamide or polystyrene while consuming energy in the 2kW to 5kW range, a much lower value than for most sintering systems. For ease of use, the operator interface is a touchscreen, considered a simpler input device than a traditional keyboard-plus-screen combination. Also, the system’s internal venting function enables direct use in an office environment such as a dental laboratory.
Desktop Factory, a newcomer to the RP world over the past few years, has based its entire system design on the dual qualities of efficiency and ease of use. The Desktop Factory uses an electrostatic process involving a powdered inert nylon material, a rotating drum, and a halogen lamp for “melting.” Operating software automatically orients the imported STL file, slices the data into appropriate layers, and calculates any necessary support structure that is formed in an easy-to-remove honeycomb pattern.
Now scheduled for a third-quarter 2008 release, the Desktop Factory system is initially targeted to professionals in the traditional prototyping environment who previously could not afford an RP system. The company’s ultimate market includes educators, students, and the do-it-yourself consumer, so one current project is devising a cartridge-based material system. Currently, an internal vacuum/filter system keeps loose powder issues to a minimum.
At Z Corp, the newest software package, ZEdit Pro, simplifies preparing 3D data files for full-color 3D printing. ZEdit Pro focuses on three tasks: optimizing geometry for 3D printing, applying color and images (such as labels) to 3D models, and segmenting or hollowing designs to accommodate oversized models and eliminate wasted material.
ZEdit Pro automatically “3D-Print enables” data produced by non-3D-CAD software packages. This feature accepts the digital visualization and rendering content that architects, animators, and gamers create, as well as the information generated by medical scans, all based on a four-button intuitive interface.
Innovation Keeps a Steady Pace
Continuous creative development is the hallmark of the RP world. In Ireland, newcomer Mcor Technologies hopes to bring 3D printing to a wide audience with its low-cost (about $22,000) layered-paper RP system. Though reminiscent of previous laminated-object-modeling (LOM) processes, the Mcor Matrix (currently in beta testing in Europe) uses a much more cost-effective and user-friendly approach to building models.
The Mcor process uses standard-size sheets of ordinary, consumer-supplied paper bonded layer-to-layer with carefully dispensed dots of water-based adhesive (think white school glue). A blade cuts the part according to the input STL file, which the company’s Slice-IT software prepares for building.
The support structure is simultaneously created from the same paper, but selectively adhered with lower-density adhesive for easy removal. Finished Mcor Matrix parts feel like carved wood. Users can harden them with cyanoacrylate adhesive, then sand and paint them. Loading the system with colored paper offers another way to produce colored parts.
As RP choices widen, the phrase “Paper or plastic?” will take on new meanings. With so many examples of improved efficiency and user friendliness, you may decide to be the next customer.
In part 2 of this series, we’ll focus on rapid manufacturing (RM) and the improvements seen in final-parts applications. Along the way, we’ll continue to ask vendors how their systems rate on an environmental scale.
Contributing Editor Pamela J. Waterman is an electrical engineer and freelance technical writer based in Arizona. You can contact her about this article via e-mail sent to [email protected].
Information:
3D Systems
Rock Hill, SC
3dsystems.com
Desktop Factory
Pasadena, CA
desktopfactory.com
Dimension 3D Printing Group
Eden Prairie, MN
dimensionprinting.com
EOS GmbH
Krailling bei München, Germany
eos.info
The ExOne Company
Irwin, PA
exone.com
Mcor Technologies
Ardee, County Louth, Ireland
mcortechnologies.com
Objet Geometries, Inc.
Billerica, MA
2objet.com
Roland Advanced Solutions Div.
Irvine, CA
rolanddga.com
Stratasys
Eden Prairie, MN
stratasys.com
ZCorporation
Burlington, MA
zcorp.com
Subscribe to our FREE magazine,
FREE email newsletters or both!Latest News
About the Author

Pamela Waterman worked as Digital Engineering’s contributing editor for two decades. Contact her via .(JavaScript must be enabled to view this email address).
Follow DE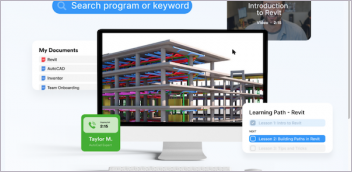

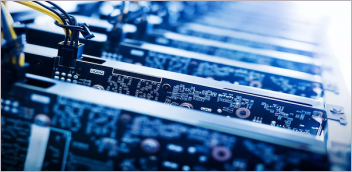
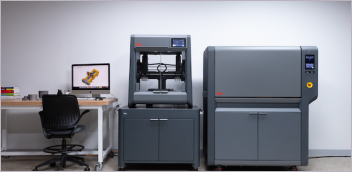