Rapid Parts Move into the Mainstream
No matter how you define it, many forms of Rapid Tooling & Manufacturinghave earned their place in the toolbox.
Latest News
December 1, 2004
By Pamela J. Waterman

From electronic dog collars to dissolvable bone inserts, real-worldparts are coming from rapid prototyping (RP) equipment, now sometimestermed rapid tooling (RT) or rapid manufacturing (RM) systems. Whetherthe parts are directly fabricated in a final material or indirectlycreated via a variety of methods, rapid tooling and manufacturing(RT&M) solutions are not only on the roster but playing firststring in a diverse arena of manufacturing applications.
One participant on the popular RP-ML listserv notes that successfulRT&M needs a slightly different manufacturing approach, but whenyou think outside the box, the approach can save time and money.Witness the enthusiasm for RT&M that ran high during a recentregional expo at the University of Arizona in Tucson. Several dozenvendors representing both RP system manufacturers and service bureauswere making deals with each other and more than 600 attendees. It willbe interesting to see if that continues at the annual SME RP&M showin Detroit this month.
Figure 1(left): When a cracked aluminum pulley idled its productionline, a manufacturer drew up a replacement and used a Stratasys FDMprinter to manufacture a working pulley from polycarbonate in less thanfour hours. It would have taken three days to get an aluminumreplacement.
Define Manufacturing
So, how far has additive processing moved into mainstreammanufacturing? Well, how many widgets per week does it take beforeyou’re considered a “manufacturer?” RT&M may never crank outthousands of parts per day, but for some producers, several hundredintricately detailed or difficult-to-machine parts a month constitutesa valid production run.
Figure 2 (above, left): A biomedical company called Therics turns outhundreds of FDA-approved bone-repair inserts per week. The inserts—madeusing a form of MIT’s 3D printing technology—help knit together brokenbones that don’t properly heal. The inserts are absorbed by the body asbones heal.
In Princeton, New Jersey, for example, a biomedical company calledTherics now turns out hundreds of identical, FDA-approved bone-repairinserts per week. The inserts are used by surgeons to knit together"non-unions” (bone breaks that don’t properly heal). Patients receivesurgical implants of scaffolding manufactured with Therics’s Theriformprocess (a licensing of MIT’s 3D printing technology) that is absorbedby the body as bones heal. The company has already produced more than1,000 standard parts and can also build custom bone implants based onCT scan data.
Other examples include the Parts Now service offered by Soligen. Itregularly fills orders for 500-600 exhaust manifolds each month. Andthousands of similar but customized RT&M parts are standardbusiness for Siemens and its individualized-fit hearing aid division.
Beyond sheer numbers of end product, manufacturing also entailsproduction for the tooling itself, which can be accomplished directlyor indirectly. In the RT world, direct tooling means creating theactual mold or mold inserts, while indirect tooling uses an RP part asthe master around which a mold is formed.
According to Wohlers Report 2004 (the annual progress report on thestate of the international RT&M industry), more than one-fourth ofall RP models are now used as patterns for prototype tooling, metalcasting, and tooling inserts. As Wohlers puts it, with more than 90percent of product development money going into tooling andmanufacturing, it makes sense to put your efforts into these areas tocut costs.
Figure 3:(left) A Solidscape T612 machine has just produced atooling-grade pattern of a fly-fishing reel. The red areas are thedissolvable support structure for the working blue parts.
Direct Fabrication
True end-function RT&M parts are cropping up all over, forming alarge part of business for many companies. Tom Gogoe at SynergeeringGroup says his company is the world leader in producing functionalintake manifolds for automotive testing and development. “We providenot just a functional prototype, but capture the production designintent itself,” says Gogoe. “The glass-filled nylon parts we create onEOS SLS systems work for flow, acoustics, and some durability testing;and we go from CAD to a working engine in four days, then ramp up to 10parts a week.”
Figure 4 (above, right) Soligen’s hybrid-manufacturing approach combines aconventional core method with its Direct Shell Production Castingprocess to create this engine cylinder-head mold.
Figure 5 (above, left): Surgical orthopedic patients are benefitting fromrapid partmaking in everything from titanium hip replacements to spinalcolumn support structures.
Stratasys, which now offers three versions of its upgradable FDM (fuseddeposition modeling) Vantage line, believes that RT&M is a good fitbetween prototyping and high-volume manufacturing. “There is always apoint where it makes sense to move into mass production usingtraditional methods,” observes Stratasys Product Manager Patrick Robb,“but for small batches where you don’t want to pay for a tool, our FDMsystems can produce finished products in real plastics such as ABS andpolycarbonates.”
A Stratasys customer, Bell & Howell, manufactures optically basedhigh-speed scanning and sorting equipment. Bell & Howell realizedthat using its Stratasys FDM system to test out a plastic hold-downbracket resulted in parts that actually exceeded their performancespecs. So instead of ordering from a molding company, they now rapidlymanufacture the brackets themselves in batches of 50, three or fourtimes a month.
Useful Applications
Aerospace and medical applications are particularly receptive toRT&M, as their quantities tend to be smaller than those in consumerproduct runs. Recognizing this opportunity, an innovative BoeingCompany subsidiary, called On Demand Manufacturing (ODM), is using 3DSystems’s SLS (selective laser sintering) machines to make parts thatsupport the military’s aircraft weight-saving efforts. Replacing metalair ducts with SLS nylon versions, and doing it with one part insteadof six, ODM expects to be on contract within the year for retrofittingAir Force transport aircraft. Company Vice President Dave Ciscel sayshis company can even plate the nylon parts for EMI shielding orgrounding.
Direct fixture production is another area. Phoenix Analysis &Design Technologies (PADT) has created its own complex fixtures using3D Systems’s SLA (stereolithography apparatus) because traditionalmachining simply cannot produce the shape needed to hold a complicatedarrangement of stator blades in place during assembly.
Another example came last year, when surgeons in Texas used Z Corpparts as “fixtures” for presurgery training on Egyptian twins conjoinedat the skull. Each of the 48 surgeons involved had their own ZCorp-produced plaster skulls to train with before the successfulseparation. And at Prototype Productions, where RT&M parts areintegrated into medical simulators, Program Engineer Scott Tiltoncomments that, “Any time our assembly group needs a small jig or atool, it can be made quickly and easily with our SLS system.”
One Of A Kind
And then there are the cases where you build just one of exactly whatyou want, when you need it. Theresa Crist, a manufacturing technicianat Raytheon Missile Systems, found a way to make sure that herassemblers had all the screwdrivers, power tools, and fasteners theyneeded for a specific job. She designed an award-winning tool cart withbuilt-in plastic pockets shaped and labeled for every item in the orderused, one cart per assembly. Crist created the pockets in 3D CAD, thenfabricated each insert in nylon on a 3D Systems Vanguard HS SLSmachine—an interesting complement to the more than 10,000 SLA/SLS partsRaytheon made just last year.
Indirect Tooling—Fine and Fast
Creating master parts from RP is becoming a common method for producinga true manufacturing tool. Whether the tooling process involves roomtemperature vulcanizing (RTV), epoxy-based composites, the variousspray-metal processes, or any other indirect approach, the mold or moldinserts are only as good as the original master part.
Many users create a master using a 3D Systems SLA machine, since SLAtechnology generates a smooth surface finish with fine detail insideand out. Rey Chu, one of four principals at PADT, notes that theyprobably turn out a tool a week based on an SLA part. For one product,a high-performance blower, they packed aluminum-filled epoxy around anSLA master to form an injection mold with good heat conduction. As aresult, PADT cut their process from ten weeks at $35,000 down to twoweeks at $5,000. It can shoot 5,000 to 6,000 parts per tool.
Left, Z Corp developed its Z Cast plaster-ceramic composite material fordirect metal casting in response to user requests. Molds includecavities and inserts.
In the world of consumable casting patterns, Z Corp offers starch-basedmodels, while Solidscape has sold more than 800 systems dedicated tohigh-precision, low ash-burnout jewelry patterns. Solidscape has alsoinstalled the 32nd of its ModelMaker RP systems running 24/7 in theproduction facility of Interpore Cross International, a medical devicecompany working with spinal implant and orthobiologic technologies.
Direct Tooling, Big Business
Soligen has led the way in direct tooling manufacture with its ceramicDSPC (direct shell production casting) process based on 3DP technology.But instead of calling it revolutionary, company President YehoramUziel notes that the business is evolutionary. “Rather than printingthe entire casting mold—an all-or-nothing approach,” he says, “wecombine four or five technologies—CAD, CNC, digital, and conventionalcasting, robotic welding—to provide a timely, cost-effective solution.For example, to cast an entire engine block is not practical when youcan use traditional machining to make 90 percent of it. We use our DSPCprocess to digitally print internal cores for the water jackets and oilgalleries, which are complex and whose design changes almost everyyear.”
Extrude Hone’s ProMetal division has customers running 100,000injection-molding cycles in ProMetal 3D-printed metal molds, and isworking with both toolless sand castings and printing gold for thedental industry. The company is now taking RT&M to the next (andnecessary) level. Dan Maas, in charge of technology transition atProMetal, explains, “You’re not going to make it until you havehardness, thermal conductivity, and fatigue life data, and use…analysis tools to understand the chemical, thermal, and metallurgicalprocesses enough to optimize them.”
These motorcycle racing valves are manufactured of titanium and were producedusing Optomec’s LENS system by ICE Motorsports.
Z Corp developed its Z Cast material for direct metal casting inresponse to user requests. Its plaster-ceramic composite is used todirectly print mold cavities and inserts, for casting near net-shapenonferrous metals. Customers like JL French and Caterpillar have said,“The last thing we want is for our competitors to know we’re using ]ZCast]—it gives us an advantage.”
Other companies in this field include Sanders Design International,with its Rapid Toolmaker system, and Precision Optical Manufacturingand Optomec, both of whom specialize in fine metal deposition for toolbuild and repair.
The Expanding Toolbox
Even more technologies, including Advanced Ceramic Research’s extrusionof ceramic-coated biocompatible plastic bone implants, offer intriguingpossibilities, but the devil is in the details. Users on the RP-MLregularly debate the fine points of both RP and RT&M machines andall that it can take to run them, from monitoring temperature profilesand efficiently orienting parts to experimenting with the ratio ofrecycled-to-virgin materials.
However, as Scott Tilton comments, “How many times has a designer comeup with something only to have a machinist come back and tell him whatfeatures are going to be difficult, if not impossible, to make? Thesame is true on RP machines; the difference is fewer people understandthem.” But, more and more are starting to, so manufacturing has gainedanother tool for its toolbox.
Contributing editor Pamela J. Waterman is an engineer and a freelancetechnical writer based in Arizona. You can contact her about thisarticle via e-mail c/o [email protected].
Education Key to Future RP
Just as RT&M systems “grow” parts, members of the technicalcommunity are growing new users from the ground up, starting with theengineers and designers of tomorrow. Dr. Ray Umashankar, assistant deanof the College of Engineering at the University of Arizona, Tucson,recently hosted more than 500 middle school students at his day-long RPExpo. His view, like that of many others in the RP community, is thatwe need to expose young people to the possibilities of this technology,along with solid modeling, so that they will view it as another toolwhen they enter the world of manufacturing.
RESOURCES
• User’s Guide to Rapid Prototyping, Todd Grimm, SME publications (2003)
• Wohlers Report 2004, Terry Wohlers, Wohlers Associates, Inc. (2004)
Company Information
Advanced Ceramic Research, Inc.
Phoenix Analysis and Design Technologies
Subscribe to our FREE magazine,
FREE email newsletters or both!Latest News
About the Author

Pamela Waterman worked as Digital Engineering’s contributing editor for two decades. Contact her via .(JavaScript must be enabled to view this email address).
Follow DE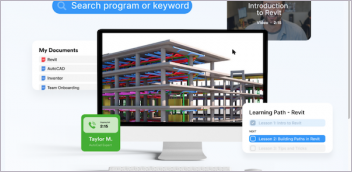

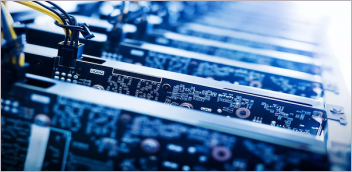
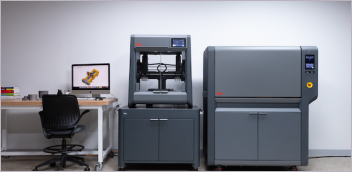