Rapid Manufacturing Ramps Up
Rapid prototyping enables companies to take a bite out of time.
Latest News
November 1, 2004
By Louise Elliott
The number of design iterations an engineering department needs and makes limits the market for rapid prototypes, as does the number of presentation prototypes needed by marketing, advertising, etc. On the other hand, many of the same machines that turn out rapid prototypes can also produce short runs of parts for finished products—say up to 1000 units—before it becomes more economical to create and use an injection mold. Even a cursory glance shows that the potential market for rapid manufacturing is much larger than that for prototypes.Stratasys and Z Corp. are two leading-edge rapid prototyping/rapid manufacturing companies with different products and somewhat different markets. Despite their differences—in terms of materials used and the markets those materials serve—both see trends toward more and better materials, increased speed, and greater demand for short-run manufacturing.
Materials Suit Inventions
Figure 1: This dinosaur head was made with PolyJet Eden 333 3D printer.
Z Corp., which uses 3D printing technology originally developed at the MassachusettsInstitute of Technology, has traditionally used plaster and resin powders onto which an inkjet printer sprays glue to create solid prototypes, and cellulose fiber bound with an adhesive for creating models used for investment and sandcastings.
The chief advantage of using powder and glue is speed, says Tom Clay, president of Z Corp. “This technology is faster than other RP technologies by an order of something between five and ten.”
Clay says that Z Corp. will soon introduce a new thermoplastic material material (see Figures 2 and 3). “Most parts using our technology now use plaster composite,which targets conceptual designs and presentation parts. Once the part is made,people usually paint it with resin to strengthen it. The thermoplastic will be much faster, and will be cured in an oven in about 30 minutes for finished parts.”
He describes Z Corp.‘s materials as falling into three application categories.“The first category is for the early stages of design, where use of RP is very iterative. That will be the area where the new thermoplastic material will be used most. The second category, prototypes for presentation purposes, calls for excellent appearance and accuracy, and our users prefer plaster and resin in that area. Our third category is a rapid manufacturing applications area that consists of manufacturing castings, and the best material for that is cellulose fiber and adhesive.”
Figure 2: An example of a painted prototype used with manufactured parts for the mockup of final design. Image courtesy of Z Corp.
Figure 3: A thermoplastic prototype not requiring any postprocessing. Image courtesy of Z Corp.

Figure 4: A coffeepot was made with PPSF (polyphenylsulfone) plastic on a StratasysFDM Titan system.
Clay of Z Corp. says that users of the company’s machines and processes often"create a digital data 3D printout of patterns for investment castings. The user coats the pattern with ceramic power and bakes it, ” he says. “During the process,the RP material—cellulose fiber and adhesive—bakes out, producing a ceramic investment casting mold. This replaces the old method of having model-makers create a wax pattern for making a shell for the mold, and saves three or four weeks in production time.”
He says that although Z Corp. has historically been geared more to the early development phase, they are hearing reports from service bureaus that use their processes that activity in short-run rapid manufacturing is growing. “The service bureaus say that they are now being asked to do more, including a transition into short-run manufacturing rather than just single prototype parts.“Z Corp. itself has been seeing more activity toward what Clay describes as “bridging manufacturing production. When companies are in a hurry to get products to market,and need fast results, they want to get a first run out while the eventual manufacturer is still gearing up. This represents a turnaround from recent ‘downturn’ days when companies were delaying manufacturing production.”
Figure 5: This functional prototype is made with a polycarbonate (PC) durable plastic called PC-ISO. PC-ISO meets both ISO 10993-1 and USP Class VI standards.Image courtesy of Stratasys.
On a recent trip to Europe, he says he encountered demand for flexible rapid manufacturing techniques for rapid tooling—which falls into his company’s area of expertise.
Like Z Corp., Stratasys has been receiving more requests for short-run rapid manufacturing from service bureaus. The company has its own in-house service bureau,called Build FDM, as well, which reports receiving multiple orders for both prototypes and rapid manufacturing.
Scott Crump, CEO of Stratasys, says that the company is aiming to grow its rapid manufacturing business. “Right now, less than 10% of business for RP machine manufacturers is rapid manufacturing—but the trend is toward major expansion of that segment.Up to a given level of parts manufacture, additive technology is more economical than making injection molds. Once you get into large-scale manufacturing, of course,the reverse becomes true.“He points out that to produce real products, the machines need to use real-use plastics that will stand up to the application. “We plan to develop systems that will excel at rapid manufacturing, and we will market them specifically for that purpose. It’s going to have to include fully automated support removal to drive down labor costs, if it’s to be economically feasible.“If rapid manufacturing can break the barriers of cost, speed, and improved surface finish of parts, Crump believes it will grow explosively. “Currently, while rapid manufacturing saves tooling costs, it has a high cost per part compared to injection molding—but given a better price/performance ratio, cost should drop dramatically.“At the moment, RP has a slow part-throughput capacity, compared to injection molding. “We’re moving in the direction of high throughput,” he says, “and, in fact, we’ve increased our throughput ninefold over the last seven years.“Stratasys is also putting efforts into improved surface finishing. “Currently,the areas where our customers want rapid manufacturing are for lots of one through 1000 parts, custom manufacturing, and pilot product runs before building the tools to make large quantities,” Crump says. “Volume beta testing is another current area of demand—before the final shape or details have been decided. Usually companies need hundreds of units for this purpose, not multiple thousands. And no one wants to invest in a mold before they’ve made final decisions.“RP seems to be pointing the way toward a new way of ramping up manufacturing quickly. Given the emphasis placed by competitive companies nowadays, that looks like a trend that can only grow.
Contributing editor Louise Elliott is a freelance writer based in California.Offer Louise your feedback on this article through [email protected]
Companies Mentioned
Subscribe to our FREE magazine,
FREE email newsletters or both!Latest News
About the Author

DE’s editors contribute news and new product announcements to Digital Engineering.
Press releases may be sent to them via [email protected].
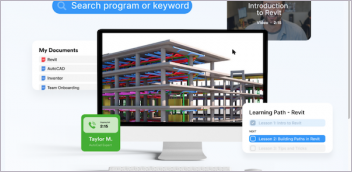

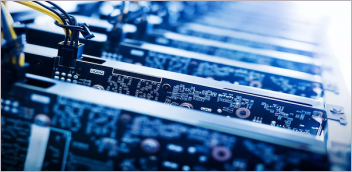
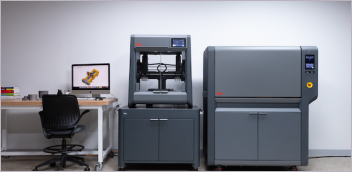