Latest News
October 1, 2005
By Ann Mazakas
The senior marketing engineer for Sescoi USA discusses challenges in the mold and die industry.
This is the eighth in a series of interviews with leaders in the CAM industry.—DE Editors
Jeffrey Jaje, a senior marketing engineer for Sescoi Inc. in Southfield, MI, first encountered CAD/CAM technologies while earning a Bachelor of Science degree in mechanical engineering degree from Kettering University in Michigan. At Kettering, the curriculum focused on both real-world job skills as well as academics. As a result, Jaje worked for a corporate sponsor in the machine shop running manual machines as well as programming NC mills.
After graduating, Jaje began his career at a CAD/CAM software developer eventually acquired by Autodesk. He then continued to gain valuable machining and CNC programming experience at mold and die shops. By keeping one foot in manufacturing while the other remained in the software field, Jaje formed a valuable perspective regarding the needs of the manufacturing shops as well as the capabilities of the software developers. Combining this experience with a marketing-focused Masters of Business Administration from Wayne State University in Michigan allows Jaje to be an ideal conduit between users and developers. While many products have come and gone, Jaje can attribute WorkNC’s success and staying power to some simple truths, “The CAM market has changed over the last 20 years, but some things have not changed, the need to make higher quality parts faster and for less money. WorkNC is an integral part of that process.”
Jaje: We see a real need to facilitate the programming of parts on the shop floor. I’d say that considerably more than half of our customers run WorkNC on the shop floor right next to the mill. We need to address the needs of the mill operator working in a manufacturing environment as well as an engineer or a CAD designer working in an office. Anything that can automate the job of that mill operator makes life a lot simpler. One key area for the mill operator is feature recognition that automates the drilling of holes. With the increasing use of solid models, our system can automatically find every hole and create machining processes based on the size and type of the hole.
We build in the logic for feature recognition so the user doesn’t have to spend a lot of time interacting with the system. In our recent release of Version 17 we introduced a new keyway feature that automates the machining of keyways. It makes the cutting of keyways quick and easy.
![]() |
Jeffrey Jaje, Senior Marketing Engineer, Sescoi Inc. |
Another trend is to really make use of the internet and HTML for online documentation. With so many companies using intranets now, it is helpful to be able to give the next shift your HTML-based documentation. If you’re ISO-9000 or QS-9000 certified, you have to document everything.
Right now our documentation is HTML-based, so it can be accessed from any computer with a Web browser. Our documentation is very simple and straightforward and it’s totally customizable so you can make it look any way you want. Now we’re going to start giving people the tools to customize the documentation any way they want even if they aren’t an HTML guru.
Just by making use of a company’s intranet and using tools in your CAD/CAM system like HTML documentation will result in fewer problems. Sometimes something as simple as being able to create good shop floor documentation with a CAD/CAM system can make a huge difference in eliminating mistakes.
What types of companies typically use your software?
Jaje: Our software is primarily targeted for the mold and die industry. Even though this involves complex surface machining, we have a lot of customers who want simpler automatic functionality as well. We’ve been responding by adding more automation. Two years ago, in Version 15, we introduced WorkNC-CAD. Prior to this we had no CAD capability at all, but we listened to our customers when they said they wanted basic CAD functions. Even though our customers just wanted simple functionality, we knew we needed to go deeper. We gave them CAD for the simple tasks and also expanded it to give them CAD for more advanced tasks like features.
What can you tell me about your recent release of WorkNC V17?Jaje: Our most notable change was the introduction of the WorkNC Auto 5 product, which is pretty revolutionary. It automatically generates collision-free 5-axis toolpaths from existing 3-axis toolpaths. Lots of mold shops have bought 5-axis mills, but didn’t have really good software to run them. Our goal was to give our 5-axis customers all the flexibility and power available now in our 3-axis software to make 5-axis programming just as easy to use. The more than 21 types of finishing cutter paths we provide in 3-axis can now be converted to 5-axis. We had two goals in mind with this product. First, we wanted to be able to finish the part with the shortest tool possible. For example, we have some customers who want to finish an entire mold with a 1-inch ball mill that extends out of the tool holder only 11/2 inches because they want improved tool rigidity during machining. You can’t do that with 3-axis without risking a collision between the tool holder and the part; you have to do that in multiple axes.
Second, our customers want to be able to get into deep areas of the part with short tools. Without Auto 5 you’d have to do that with electrodes. Just imagine the mill time spent cutting several pieces of carbon and then the time spent sinking them in. But if you could just mill that shape from the get-go you’d save a lot of time. We think our Auto 5 for mold and die is very novel. I can use my short tool and prevent the holder from colliding against the part. It’s automatic and it’s as easy to use as WorkNC.
Jaje: Auto 5 can be applied to any 3-axis cutter path as long as it was created in WorkNC. It’s very powerful and very easy to use and has a lot of useful utilities. Our developers are spending considerable resources looking at the machine dynamics and we’re testing this on a lot of different machines. They’re working on finding the smoothest 5-axis rotation because you don’t want the C-axis jerking back and forth. The goal isn’t necessarily to always have the tool normal to the surface or to always have the tool tipped at a defined angle. The goal is to keep the machine head from hitting the part. The system analyzes the geometry to minimize the number of rotations. The more rotation you have the more it slows you down and you lose some of the benefit in speed. Plus, if your machine can’t keep up with the rotation you might get a servo error. Our developers are developing new ways of optimizing and minimizing the rotation so you only rotate where you have to. Now, mold and die shops running 5-axis mills have a software product they can use to get the most out of their machines. That’s why they bought the machine in the first place.
What other enhancements were added in Version 17?Jaje: We have quite a few re-roughing cutter paths and Version 17 introduced a new function called Flat Surface Re-roughing that produces a constant stock allowance in corners. Let’s say you just roughed all the flat surfaces of a part with a tool that had a big corner radius. Flat Surface Re-roughing will detect the material left over from that cutter so you can go back with a smaller tool to cut the flat areas in a way that is safe for your tool. That way, you don’t start semi-finishing in a stock-heavy area where the tool vibrates and breaks. This function may cost you five minutes of time but save you $50 in cutters later on.
We also introduced more 5-axis functionality by adding six new traditional 5-axis functions. With 5-axis we have always had re-roughing, but now we are allowing automatic re-roughing from any angle. If you have multi-axis machines, you can rough at one angle and then re-rough at another. This is very useful when you have pockets at different angles. You can use the automatic re-rougher to go in at any angle you choose and it knows where the material is, where it is safe for the tool to come down, whether to ramp into the material or use a radial approach, and where the metal is heavy or light.
Jaje: Absolutely. Wherever there is enough space the tool is going to enter with an arc because that’s easier on the tool and faster than ramping. If there isn’t enough room to arc in, the system knows that the tool has to ramp in. It’s easier on your inserts and it’s faster to mill that way. As soon as you rough a part, WorkNC creates a stock model. It’s the same concept as verification software that shows you the stock after you run the cutter paths, except that in WorkNC it’s automatic. After updating the stock model with the cutter path, the system knows where there is metal and where there isn’t. Based on that stock model the system knows automatically where to ramp and where to arc for the most efficient approach. Because this is a 3D stock model, you can create re-roughing from any angle.
Jaje: There are going to be more and more features. You’ll be able to define more types of features, like our keyway feature, and there will be more automatic feature recognition. Obviously there will be enhancements in the 5-axis machining arena. We’re going to see new options added into software for people who need to cut really hard metal just like you saw new options added a few years ago for people using high-speed mills. The technology in mills will continue to advance. What you can get on a high-end mill ]vs lower-end machines] today differs on a scale similar to the difference between a formula race car and a minivan. People are still buying the lower end machines and they’re also buying these extremely high-end machines. We need to be able to tailor our functions for the different machines. You’re going to see options either in the form of special cutter paths or through the use of a configuration file where the cutter path will be able to adjust for the type of machine you’re running.
You see the same thing with tooling. Now there are these new roughing cutters that, instead of using a standard round insert, have inserts with a big and small radius. These new roughing cutters can cut at a 50% to 60% faster feedrate with the same depth of cut and step over simply because of the shape of the insert. From a cutter path perspective, our software has to be adaptable to each kind of cutter so we can produce different styles of output that take advantage of new technology as it’s introduced. This is especially important when a company upgrades equipment.
CAM software is not at the point yet where you can say, “I’m using this new machine, here are the parameters, now regenerate the toolpath,” but I think you’re going to see more of that in the future. You’re going to see more cutter paths that are intelligent, that know what type of machine they’re running on, and know what to output.
Ann Mazakas is the owner and president of Intelligent Creations LLC, a provider of services to the manufacturing industry. Send your comments about this article through e-mail by clicking here. Please reference “Jafe Interview, November 2005” in your message.
Subscribe to our FREE magazine,
FREE email newsletters or both!Latest News
About the Author

DE’s editors contribute news and new product announcements to Digital Engineering.
Press releases may be sent to them via [email protected].
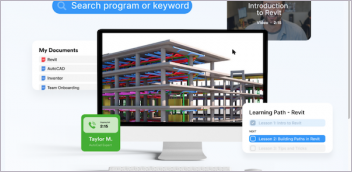

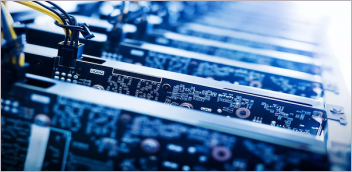
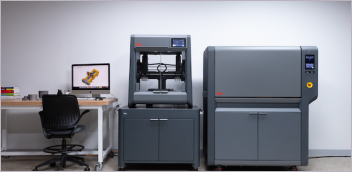