Latest News
October 1, 2004
By Laura Carrabine
B&B Molders of Mishawaka, Indiana, has always found success in making plasticparts for a variety of industries. And it has been able to do that by remainingcompetitive, which has meant keeping a focus on new technology.
At that time, Murphey set out to develop a state-of-the-art organization withcomplete in-house part and mold design and construction capability, an automatedraw material vacuum transport and loading system, the latest injection moldingmachinery, and a wide array of assembly and secondary operations processes. Nowthey produce plastic parts and assemblies 24 hours a day, five days a week withmore than 60 employees, and for a range of industries from recreational vehicleOEMs to medical implant companies and from makers of musical instruments to militarydefense contractors.
B&B Molders Design Engineer Adam Schramski uses Moldflow to close the design-to-manufactureloop by designing and then simulating its entire injection-molding process. Heensures that product molds work before reaching the shop floor.
According to Steve Rorie, B&B Molders’s operations
manager, there is a rangeof challenges in designing and manufacturing products for a diverse clientele,and there is also some common ground. “Challenges vary by industry and application,“he says, “but some of the common denominators are always quality, price, lead-time,flexibility, and responsiveness.”
Mold Adviser, a module of Moldflow Plastics Adviser, provides B&B with simulationcapability so its designers can evaluate its injection-molding process for eachnew product. It gives mold makers a high level of confidence in first-shot performance,saving on rework of the past, and giving the company a competitive edge in thebidding process.
Rorie, who’s responsible for all manufacturing activity at B&B includingproduction, engineering, and logistics, explains price ranks first. “Many customers… would dispute this in principle,” he explains, “but the reality is they maketheir decisions based largely on price. This is followed closely by quality andreliability. Finally, many look to partner with someone who can work with themfrom concept and design to mold construction and first articles, then full supplychain integration.”
Meeting Tough ChallengesAs you might expect, the company’s biggest challenge is meeting those price requirementsbecause of the many issues that factor into the problem. “As more and more industrieslook offshore,” says Rorie, “it’s difficult to compete with Asian or third-worldcountry labor rates and their propensity to copy or knock off our products. However,we refuse to be discouraged or intimidated. … Because we feel we are an industryleader in quality and reliability, we intend to be the same in the areas of scientificmolding, design technology, and process efficiency.”
Using those goals as a driving force, Rorie and his engineering team evaluatedseveral analysis packages to find one that would close the loop in the design-for-manufactureenvironment to streamline the entire process. “We didn’t want a hodge-podge ofsoftware for design, mold construction, process monitoring, production monitoring,process optimization, and quality control data,” says Rorie. “We felt it was importantto close the loop in terms of design for manufacture. In order to maximize valueto the customer and to B&B, we must have accurate part design, supported byaccurate tool design and construction, supported by an accurate process that’sin control time after time.”
Engineers looked at Moldflow and found “a system that interfaces all those aspectsand more,” says Rorie. He adds that the Wayland, Massachusetts, company’s sizeand support capability were the other driving forces. “If I have trouble reachingone person, there are a number of others I know I can call and get help fast.”
Shotscope allows for real-time process and production monitoring, and transferof all data directly to the shop floor via document viewer screens.
As a result of Moldflow Corporation’s design-to-manufacture approach to its softwareproducts, B&B Molders’s product design teams use a range of Moldflow softwaretechnologies, including Mold Adviser, Performance Adviser, Cooling Circuit Adviser,Shotscope, and Moldflow PlasticsXpert (MPX) optimization. B&B engineers alsouse Autodesk’s Mechanical Desktop and Autodesk Inventor for MCAD, CNC’s Mastercam(mastercam.com) for CAM, and VISUAL Manufacturing ERP from Lilly Software (lillysoftware.com) to electronically track up-to-date information related to jobs.
Moldflow BenefitsB&B Molders implemented Mold Adviser, a module of Moldflow Plastics Adviser(MPA), in 2000. Since then, they’ve upgraded the software with each new release,as well as added MPA Performance Adviser for fill, pack, and warp along with Moldflow’sCooling Circuit Adviser. Recently, the company completed the implementation ofShotscope for real-time process and production monitoring and added Moldflow PlasticsXpertfor manufacturing floor machine setup and process optimization.
“Our biggest concern of investing in process monitoring alone addressed the question,‘What will we do with all this information?’ ” says Rorie. “Process optimization(MPX) gives us the tool we need to make the improvements called for by the (Shotscope)monitoring system. The MPA tools provide simulation capability before we everstart to cut steel, thus giving the moldmaker a high level of confidence in first-shotperformance without all the rework of the past.
“The Adviser series of modeling and simulation capabilities have been instrumentalin helping us land a number of projects,” says Rorie. “One recent example wasa customer who received a request from his engineering group to send a part outfor Moldflow analysis due to recurring difficulties from their supplier. We performedthe in-house analysis as well as simulated the molding process driven by the MPXoptimization software. As a result, we showed the customer that we have a sizeablecompetitive advantage.”
Improving communicationsB&B Molders strives to continually improve communications alongside technologicalupdates. “We are able to import virtually any CAD software files,” notes Rorie.“3D renderings have replaced 2D drawings. The engineer walking the shop floorwith a D-sized drawing under his arm is pretty much passé. We are now able tocommunicate up-to-date, three-dimensional renderings and CAD data not only internally,but also back and forth between customers and secondary sources. In today’s supplychain, there are multiple tiers of vendors that are part of the communicationsloop. So, without the ability of electronically transferring all the updated project-relateddata, you’re fighting an uphill battle.”
Using Moldflow’s Shotscope, the B&B team is able to transfer all the datadirectly to the shop floor through document viewer screens. “Now we are able totake the data out of the design engineer’s hands and put it directly in the shopfloor technician’s hands,” adds Rorie. “Being an ISO-certified organization, oneof the things we rely on for quality control purposes is creating job books. Whenevera job order or production order hits the shop floor and goes to our presses foran injection molding operation, there is a job book associated with it. The jobbook contains the technical data for the processing parameters for the machines,as well as instruction criteria associated with quality control. In addition,job books contain all the photographs and prints related to the job. We can convertthe job book into an electronic file and keep it on the shop floor on our datacollection terminals.”
Using these steps, B&B Molders has enhanced its shop floor efficiency. Thefirm is moving from a paper-based organization to an electronic environment.
How does a 40-year old company stay on top of the technological breakthroughsthat surface on a regular basis? How does a progressive organization keep itsworkforce up to date on what’s current? B&B Molders endorses five core valuesthat Murphey established when he purchased the company from Harley-Davidson. Theyare: Be fair, Keep your promises, Respect the individual, Tell the truth, andStimulate intellectual curiosity.
To foster this last core value, the company offers two educational programs inorder to keep a qualified and well-trained workforce. To facilitate its implementation,B&B has become partners with a plastics technology program based at Lake MichiganCollege. The school’s professors teach classes at B&B Molders’s training site.In other words, the company requires ongoing training for its processors, processingsupervisors, and many of its management teams.
One program is a tuition-reimbursement program in which the company pays forcourse fees when trainees complete and pass classes. The other program is calledPay for Knowledge in which the company increases team members’ salaries when theysuccessfully pass one of the Lake Michigan College classes.
“By offering such incentives,” Rorie explains, “people’s minds continue to beopen to new technology. There is no old school way of thinking here because thepersona of our organization is so education-oriented. We know the only way tosurvive is by using the latest technology and educating our workforce. And,” hesays, “the only people who are willing to embrace technology are those who aretruly open minded and receptive to it … ongoing education is what helps keep people’sminds open.”
Laura Carrabine is a public relations consultant located in Cleveland, OH. You can contact herabout this article via e-mail at Desktop Engineering Feedback.
B&B Molders
Mishawaka, IN
bandbmolders.com
Moldflow Corp.
Wayland, MA
moldflow.com
Subscribe to our FREE magazine,
FREE email newsletters or both!Latest News
About the Author

DE’s editors contribute news and new product announcements to Digital Engineering.
Press releases may be sent to them via [email protected].
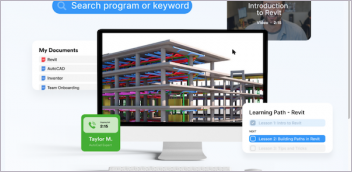

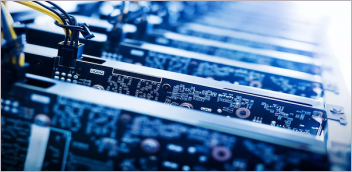
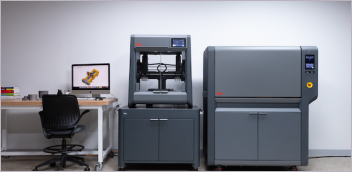