
An implant designed using Within Medical for 85% human facial restoration is pictured. Image courtesy of Autodesk.
Latest News
October 1, 2015

Common design exploration and optimization software tools today rely on simulation and analysis as a step separate from geometry creation. If it were a dance, we’d call it the Engineering Two-Step. First you design a part with CAD then explore options for improvement. Engineering workflows worldwide are based on this iterative dance.
The dance exists because of pre-existing conditions over which the engineer has no control. Such primary factors as material composition or manufacturing method are givens, not subject to modification or optimization. Now, a new set of software tools are coming to market that take advantage of both additive manufacturing and computational design algorithms to bypass the pre-existing conditions of material composition and geometry.Autodesk Within is the name of a new line of product development software that applies generative design algorithms to additive manufacturing. Originally developed for architectural design, generative design software would work as a parametric engine to find an optimal solution to a specific design challenge. Instead of trying to solve a topology challenge for an architect, Autodesk Within is intended to solve the challenge of designing the most efficient internal structure of an object to be 3D printed. By providing such inputs as desired weight requirements, maximum stress and displacement, Autodesk Within generates designs with variable density lattice structures and surface skins. The company says the resulting components are higher performing and can be considerably lighter in weight than traditional designs. The software is cloud-enabled, so the potentially millions of design iterations do not burden the local CPU.
The technology is currently available in two forms: Autodesk Within is for aerospace, automotive and industrial applications; Autodesk Within Medical is for the design of orthopedic implants. The ability to design lattice structures for additive manufacturing is crucial to both products, but the reasoning for them varies with the application.
Custom Implants
Within Medical allows biomedical engineers to create orthopedic implants with micro-lattice porous structures that help properly connect implants to living bone (osseointegration), and promote development of blood vessels in the surrounding tissue (vascularization) to facilitate healing.
“Because bone ingrowth is vital for many orthopedic surgeries, Within Medical uses various pore size configurations and rough lattice surfaces to help the porous implant integrate properly with the bone,” says Mark Davis, senior director of Design Research at Autodesk. “Within Medical designs are also optimized for specific 3D printing processes—such as direct metal laser sintering and electron beam melting—that allow for highly accurate manufacturing.”
More than 600 patients are now living with implants designed using Within Medical, including surgical repair of defects or deformities of the skull, hip joint replacement, lumbar vertebral replacement and facial reconstruction.
“Within Medical has contributed enormously to changing the way in which we design and manufacture implants,” says Daniel Fiz, CEO of Novax DMA, a company specializing in the R&D and production of innovative medical technologies and an early user of Within Medical. “It is a tool with which both custom made and standardized implants can be designed and developed in a much more biological and intelligent way. As both a surgeon and a designer, I believe this is the most important tool I have ever used, enabling us to make anatomic designs that would be impossible with other software.”

Titanium Automotive Roll Hoop
Early Autodesk Within user 3T RPD is a UK-based additive manufacturing production company that consults with manufacturers in a range of industries including aerospace, F1 motorsport and medical devices. For an F1 project 3T RPD co-designed a titanium alloy roll hoop that would be attached to a raised point of the vehicle. Typically roll hoops are heavy to withstand high stresses during a crash. But the weight normally required is not ideal for maintaining a low center of gravity, as needed on this project.
Autodesk Within was used to design a roll hoop with internal lattice structures that could only be fabricated using additive manufacturing, and reduced the weight considerably without compromising design specifications. When installed, only the underside of the hoop’s face required a small support structure to be added at final assembly; the remainder of the design was self-supporting.
Watch DE Senior Editor Kenneth Wong’s video overview of Autodesk Within:
More Info:
Subscribe to our FREE magazine,
FREE email newsletters or both!Latest News
About the Author

Randall S. Newton is principal analyst at Consilia Vektor, covering engineering technology. He has been part of the computer graphics industry in a variety of roles since 1985.
Follow DE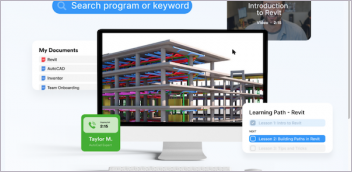

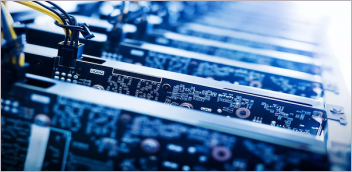
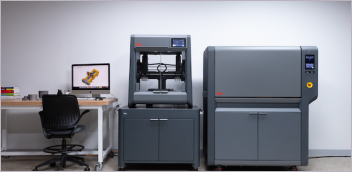