Latest News
December 16, 2013
A few weeks back, the Check it Out column looked at a fluid dynamics tech tip from ANSYS called “Do Not Remesh, Morph Instead.” Today’s Check it Out is like Part 2 of that column.
![]() |
I watched an on-demand webinar available on the ANSYS Fluid Dynamics Technology Tips web page called “Predicting the Performance of an Electric Motor via a Multiphysics Simulation.” You might really want to take this one in because it strives to answer the first question almost any engineer has when talking heads like me start waxing poetic about multiphysics analyses: What’s in it for me?
Now, your “routine” multiphysics demo, if there is such a thing, usually shows you some sort of fluid-structure interaction force/structure displacement study with weakly (1 “way) or strongly (2-way) coupled systems simulated. Good stuff, mind you, but this webinar’s demo is different. It looks at tightly coupled physics: electromagnetics and thermal. Key though is that it compares the results of a single physics analysis approach to a study versus a multiphysics approach. The results are enlightening.
The assumption of the study is that thermal management performance impacts the magnetic material temperature. Magnetic material temperature, in turn, impacts the electric motor’s performance. Performance is torque. The basic outline of the demo is that the magnetic field in the magnetic material heats the material. The heat is diffused, and air, water, or both cool the system. The stars of the demo are ANSYS Maxwell electromagnetic field simulation software and ANSYS Fluent CFD (computational fluid dynamics) software.
Now, one of the many things that make this demo so interesting is that it offers two sets of predictions. First, there’s what you can call the traditional analysis workflow, essentially this means single physics 2D-to-3D analyses of each phenomena assuming a magnetic material temperature. The second looks at coupled 3D-to-3D physics analysis of the phenomena including magnetic material property data and the coolants.
ANSYS Fluent handles the fluid and solid heat conduction computations—i.e., temperature—and ANSYS Maxwell does the electromagnetic forces and losses computations in both 2D and 3D, which forms the basis of the comparison. For good measure, ANSYS Structural could have been involved here to do deformation. For brevity it was not, although there’s a brief look at ANSYS Structural at the end of the main presentation. One interesting thing here is the ANSYS Workbench setup of this analysis project. It automates most of the setup, so you’re really just linking and looping analysis applications and results to solve your performance and thermal inquiries.
The demo steps you through what you’d do to perform single and coupled physics analyses for this job. The upshot of it all is that simplified 2D-to-3D simulation strategies can lead to errors in the prediction of the electric motor performance. The 3D-to-3D multiphysics approach exposed a 16% error in that strategy. How you are led to that result is what makes this such an interesting presentation.
“Predicting Electric Motor Performance with Multiphysics Simulation” runs for a well-paced 32 minutes. It is moderately technical, but very easy to keep up with. Registration will be required, but it is more than worth it. If you ever wondered what multiphysics analysis can potentially offer you, this is a must-see presentation regardless of your association with the phenomena at hand.
Thanks, Pal. – Lockwood
Anthony J. Lockwood
Editor at Large, Desktop Engineering
Predicting the Performance of an Electric Motor via a Multiphysics Simulation
Subscribe to our FREE magazine,
FREE email newsletters or both!Latest News
About the Author

Anthony J. Lockwood is Digital Engineering’s founding editor. He is now retired. Contact him via [email protected].
Follow DE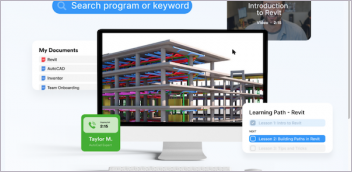

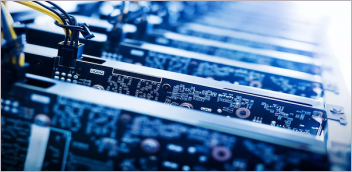
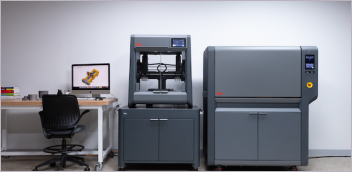